Development Status of Ammonia Combustion Technology
Various initiatives aiming to expand the use of ammonia fuel to reduce CO₂ emissions
IHI Corporation
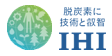
Ammonia is drawing attention as one of carbon-free fuels that do not emit CO₂ when burned, so various companies are examining whether to use it not only in boilers and gas turbines for thermal power plants, but in other various industries as well. IHI is carrying out development as a pioneer of ammonia combustion technology, and this article introduces the development status.
Introduction
There is strong demand not only for the power industry but for various other industries as well to reduce greenhouse gas emissions globally to curb global warming and create a sustainable society. In Japan, the government announced the Sixth Basic Energy Plan in October 2021, which says that the country aims to achieve carbon neutrality with net-zero greenhouse gas emissions by 2050. It also raises the target of reducing greenhouse gas emissions by 46% compared to the 2013 level by 2030 as a step toward reaching the ultimate goal. Furthermore, the Agency for Natural Resources and Energy’s “Energy Supply and Demand Outlook for FY2030” specified not only the increase in proportion of renewable energy but also the use of hydrogen and ammonia so that they will account for 1% of all power generation in 2030.
Considering the situation surrounding carbon neutrality and the characteristics of ammonia, IHI is currently planning and preparing equipment and considering various issues related to establishing an ammonia combustion technology in which ammonia fuel accounts for 20% of the fuel in existing thermal power boilers and demonstrating the technology with commercially operating boilers. In addition, we are developing a burner to further increase the utilization rate of ammonia fuel in boilers for thermal power plants.
We believe that ammonia combustion technology will be applicable not only to thermal power boilers but also combustion furnaces in various industries where fossil fuels are currently employed. IHI is proposing the use of ammonia as a fuel to customers who need to reduce their CO₂ emissions.
This article takes a comprehensive look at the information on ammonia fuel utilization technology that IHI is currently developing.
General characteristics of ammonia as a fuel
Ammonia, which is easily liquefied and has a high hydrogen content per volume, has excellent characteristics as a medium for transporting and storing hydrogen. Hydrogen stored in ammonia is easy to handle compared to hydrogen alone because ammonia’s boiling point is −33.4°C under atmospheric pressure. Although ammonia is a flammable gas and can itself be used as a fuel, it burns slowly with a low calorific value per unit volume compared to other flammable gases such as methane and propane. It may also emit an enormous amount of nitrogen oxide (NOx) when burned because it contains nitrogen in the molecule, represented as NH3. In developing a combustor fueled by ammonia, therefore, we need to be aware of the following two points: ignition stability and how to curb NOx emissions.
Application of ammonia 20% combustion technology to thermal power boilers
The technology for using ammonia fuel in thermal power boilers has been steadily developing since FY2016. The goal is to develop a burner powered by fuel comprising an ammonia content of 20% (on calorific basis), apply the burner to actual use, and evaluate the performance. We confirmed that the flame generated when a burner is fueled with a fuel comprising an ammonia content of 20% is stable on the burner while the swirling force of the combustion air is properly adjusted with vanes. The NOx concentration in the combustion gas was evaluated with figures measured when the two-stage combustion ratio was changed. We successfully controlled the NOx concentration measured within the two-stage combustion ratio of 25 to 35%, which is used in commercial boiler plants, to the same level as in conventional firing with a single fuel. In addition, we confirmed that the ratio of unburned content in the fuel during ammonia 20% combustion was almost equivalent to that in firing with a single conventional fuel within the same two-stage combustion ratio of 25 to 35%, even after taking into consideration the errors in measurement (refer to “Carbon-Neutral Thermal Power Generation Using Ammonia” IHI Engineering Review, Vol. 55, No. 1, 2022).
As the final stage of development, the demonstration test of the ammonia 20% combustion technology started in March 2024 using a large utility boiler, 1 million-kW output, at Hekinan Thermal Power Station Unit 4 of JERA Co., Inc. This is drawing attention globally because it is the first time in the world to conduct a demonstration test using large power generation equipment that is commercially operating.
Before the demonstration test, we evaluated the effect and commercial feasibility of operating the entire plant with this fuel, such as the effect on the fan and other boiler auxiliaries, the effect on boiler characteristics such as main steam and reheat steam temperatures, and the effect on the electrostatic dust collector and other exhaust gas treatment equipment. As a result, when conducting the demonstration test of ammonia 20% combustion technology at the plant, it was evaluated that there was no need to upgrade or remodel the main boiler auxiliaries and the associated costs were minimal. After having prepared and arranged devices for the demonstration test, we began the following evaluations and examinations:
- Performance evaluation of the entire boiler plant during ammonia 20% combustion
- Evaluation of operability and controllability under dynamic operating conditions such as startup and shutdown as well as load changes
- Examination of safety measures to be taken in the event of ammonia leakage
We anticipate that these results will be useful to establish ammonia 20% combustion technology for power generation equipment, and expect the technology to be applied to other power plants in the future.
Aiming to increase the use of ammonia
To further reduce the amount of CO₂ emitted from thermal power boilers, in FY2021 we began researching a burner and boiler system that would increase the use of ammonia in firing to 50% or more. As for a burner fueled mainly by ammonia, the design policy has been established and will be reflected in the entire boiler plant’s commercial feasibility study. If the percentage of ammonia exceeds 20%, the effects of exhaust gas and other combustion characteristics and the increased ammonia flow rate will be greater. These factors will further affect the performance of the entire boiler, such as main steam and reheat steam temperatures, and the increase of exhaust gas and pressure loss will further affect the performance of the induced draft fan. In addition, when applying the technology to thermal power boilers, it will be necessary to carefully examine the operating method because the increase of ammonia use may reduce the amount of coal supplied by the pulverizer to a level below the lower limit of the normal operating range.
At IHI, the design, manufacturing, and construction departments are working together to identify potential problems and discuss measures against them. The study and evaluation of the entire boiler plant are taking place with the cooperation of JERA, and we have begun a concrete evaluation of the plant’s commercial feasibility to conduct a demonstration test using an opposed firing boiler of 1 million-kW output at Hekinan Thermal Power Station Unit 5.
In FY2021, we also began developing a burner fueled by ammonia alone. In May 2022, we successfully operated a small combustion test furnace fueled by ammonia alone at IHI Aioi Works while controlling the NOx concentration characteristics. In the observation of the condition near the burner, the flame could not be seen visually because the fire-proofing material installed in the test furnace was red-hot, but we found a wavelength in the ultraviolet range using IHI standard flame detector and confirmed that the flame was detected.
Regarding the burner fueled by ammonia alone, we are examining how to optimize the burner’s structure using large combustion test equipment at the Aioi Works. This is because we need to evaluate the details in a scale assuming its use in a commercial boiler plant.
New installation of large ammonia supply equipment
To develop a burner fueled mainly by ammonia and a burner fueled by ammonia alone, we need to conduct a combustion test in a large combustion test furnace to obtain detailed evaluation results simulating their use in a commercial boiler plant. Because the existing ammonia supply equipment used in the burner’s development could not provide enough ammonia, IHI therefore constructed new large ammonia supply equipment at the Aioi Works and started operating it in September 2022.
This large ammonia supply equipment includes a tank that can store up to 20 t of liquefied ammonia and can vaporize and supply up to 2.4 t/h of liquefied ammonia. This has enabled us to conduct combustion testing consecutively for eight hours or longer in a large combustion test furnace.
The heat source for vaporizing ammonia in this supply equipment is steam supplied from a small boiler installed in the equipment and fueled by LPG. Hot steam supplied from the small boiler vaporizes ammonia by heating the liquefied ammonia with a vaporizer. The vaporized ammonia passes through the pressure-reducing valve and flow-regulating valve, after which it can be supplied stably at any pressure and flow rate required for combustion testing.
We thoroughly examine and consider safety, and have not only installed multiple ammonia gas detectors but also prepared emergency equipment, such as emergency sprinklers and emergency operating power for power outages. In the area around the tank, a dike has been installed that can stop the flow of all liquefied ammonia stored in the tank to prepare for the situation where liquefied ammonia leaks from the tank.
Application of ammonia combustion technology to industrial furnaces
Ammonia combustion technology will be applied to many industries other than the power industry. In the industrial world, companies are accelerating the pace to reduce CO₂ emitted from their product manufacturing processes and looking at technology that uses ammonia fuel as one way of doing that. Examples of such processes include ceramic sintering and heat treatment of metal surfaces.
In the petrochemical industry in particular, CO₂ is emitted from industrial furnaces that are adjusted to suit each process, since the oil refining process incorporates various heating and decomposition reactions. The fuels mainly used in these industrial furnaces for the refining process include heavy oil or natural gas in heating furnaces, and LNG in decomposition furnaces to heat and decompose naphtha. It is possible to drastically reduce CO₂ emissions by using ammonia to replace a portion of such fuels or by burning ammonia exclusively.
IHI has begun research into using ammonia fuel in decomposition furnaces and is planning combustion tests. An LNG burner for naphtha decomposition furnaces has a structure that differs significantly from the one employed for thermal power plants, and the fuel and air are supplied from the same nozzle after being mixed. The tip of the burner is a molded ceramic cone, and the fuel is injected from the nozzle to the cone. The cone is heated by radiation from inside the furnace, and the fuel contacting the cone leads to stable ignition. In order to use ammonia fuel in the burner, we need to review the fuel’s flow speed from the nozzle and swirling force to improve ignitability. We are currently working to reproduce the results of simulation study using a small test equipment.
Furthermore, we expect to see ammonia-fuel combustion technology applied to various processes in the chemical, ceramics, steelmaking, and other industries, which have conventionally used heavy oil, LNG and other fossil fuels. We will continue developing the ammonia combustion technologies in accordance with customers’ needs because each type of industrial furnace requires a different burner and furnace shape, as well as different temperatures for various uses and processes.