Catalytic Conversion of CO₂ to Lower Olefins and SAF for Sustainable Materials and Fuel Production
KAMATA Hiroyuki, MIZUKAMI Noriki, HASHIMOTO Takuya, TSUJIKAWA Jun, SATO Kentaro
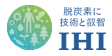
KAMATA Hiroyuki : Doctor of Engineering, Manager, Applied Physics & Chemistry Group, Technology Platform Center, Technology & Intelligence Integration
MIZUKAMI Noriki : Applied Physics & Chemistry Group, Technology Platform Center, Technology & Intelligence Integration
HASHIMOTO Takuya : Applied Physics & Chemistry Group, Technology Platform Center, Technology & Intelligence Integration
TSUJIKAWA Jun : Manager, Regional Innovative Solution Division, IHI ASIA PACIFIC PTE. LTD.
SATO Kentaro : Doctor of Science, Manager, Regional Innovative Solution Division, IHI ASIA PACIFIC PTE. LTD.
To realize a carbon neutral society to mitigate global warming, carbon recycling in which CO₂ is captured and converted to useful chemicals and fuel is an important option for us. The IHI Group is currently dedicated to developing the technology to convert CO₂ to lower olefins for resin and plastic productions and liquid hydrocarbons as a precursor for the sustainable aviation fuel (SAF). The IHI Group will continue proceeding to the social implementation of these technology to realize the carbon cycle. This will contribute to promoting the carbon neutrality even in the fields of chemical productions and liquid fuels, which have been considered to be difficult to reduce CO₂ emissions by using substitute for fossil resources.
1. Introduction
To overcome the crisis posed by climate change, it is necessary to reduce greenhouse gas emissions as well as to limit the temperature increase to below 2°C compared to pre-industrial levels, and below 1.5°C if possible(1). CO₂, a cause of global warming, is being emitted globally at 11 Gt-C/y on a carbon basis, of which CO₂ from utilization of fossil resources accounts for 9.4 Gt-C/y, or approximately 85% of the total. On the other hand, atmospheric CO₂ is absorbed into both sea and land area in amounts of 2.5 Gt-C/y and 3.4 Gt-C/y, respectively. The increase in atmospheric CO₂ is approximately 5.1 Gt-C/y, which is estimated as the emissions minus absorption, and this is responsible for the increase in CO₂ concentration over time(2). It is thus necessary to reduce CO₂ emissions resulting from the use of fossil resources and to shift to what is known as a carbon neutral society, where CO₂ emissions are balanced with fixation and utilization.
A shift from fossil resources to renewable energy sources is underway in various fields around the world. Especially in the power generation field, renewable energy sources are being introduced rapidly; with electrification’s increasing share of final energy consumption, it is projected that roughly 50% or more of primary energy will come from renewable sources in 2050(3).
To achieve the Japanese government’s goal of virtually zero CO₂ emissions by 2050, it is essential to significantly reduce dependence on fossil resources in addition to making significant progress in introducing renewable energy in the power generation field. Still, there are many fields in which fossil resources cannot easily be replaced by electrification or energy saving technology. For example, the field of materials, which includes resins and plastics, falls into this category. Resins and plastics are produced from lower olefins (ethylene, propylene, etc.) derived from naphtha, which is refined from crude oil, or ethane in natural gas. Renewable energy sources such as biomass are beginning to be utilized as alternatives to fossil resources, but these are difficult to supply in sufficient quantities, so the alternatives to fossil resources are extremely limited at present.
The CO₂ emissions intensity for producing ethylene, a typical lower olefin, from naphtha is estimated to be 1.8 to 2.0 t-CO₂ per ton of ethylene(4). The CO₂ emissions intensity is relatively low at 1.0 to 1.2 t-CO₂ when ethane in natural gas is used as feedstock(4), but it is estimated to be approximately 10 t-CO₂ when coal is used as feedstock(5), which results in a very high CO₂ emissions intensity. Resins and plastics are currently produced worldwide at an annual volume of approximately 400 million tons, and this volume is expected to increase(6). The carbon footprint of resin and plastic production can be significantly reduced by using lower olefins made from recycled CO₂.
In the field of fuels, such as aviation fuel, it is difficult to replace fossil fuels with other fuels. For short range commuter and regional aircraft, batteries and hydrogen are potential fuel sources, but for medium- to long-range flights, liquid hydrocarbon fuels with high energy density are indispensable. In response to this need, sustainable aviation fuel (SAF) is attracting remarkable attention. SAF is a generic term for low carbon footprint aviation fuels synthesized from renewable feedstocks such as biomass and waste oil. SAF is advantageous in that it can be blended directly with fossil fuel-based jet fuel because its properties are almost identical to those of the jet fuel currently in use. The International Civil Aviation Organization (ICAO) has set a long-term goal of achieving virtually zero CO₂ emissions by 2050 in the field of international aviation, and it assumes that jet fuel must be replaced by SAF and hydrogen(7).
As described above, it is difficult to achieve carbon neutrality by replacing fossil resources with electricity in the fields of materials made of hydrocarbons and fuels that require high energy density. Therefore, these fields require the supply of renewable hydrocarbons that are not derived from fossil resources. The process of synthesizing hydrocarbons using what is known as “green hydrogen” derived from renewable energy sources and CO₂ as the carbon source can provide materials and liquid fuels with a low carbon footprint, and this is an important technology to achieve carbon neutrality for resins, plastics, and aviation fuels(8)–(10). This paper describes technology the IHI Group is working on to synthesize lower olefins and liquid hydrocarbons which are feedstocks for SAF from CO₂.
2. Principle of hydrocarbon synthesis from CO₂
2.1 Catalysts and processes for converting CO₂ to hydrocarbons
Figure 1 shows a typical reaction process for synthesizing hydrocarbons as feedstocks for materials and liquid fuels from CO₂ and hydrogen. Reaction processes can be broadly classified into indirect processes, which involve CO or methanol as intermediates, and direct processes, which directly hydrogenate CO₂. These processes can be classified into Fischer-Tropsch (FT) reaction and its modified form and dehydration reactions of synthesized methanol.
Table 1 lists the characteristics of CO₂-derived hydrocarbon synthesis processes, including via methanol as an intermediate, FT reaction via CO, and direct hydrogenation of CO₂. Each process has advantages and disadvantages, but the direct CO₂ hydrogenation process can synthesize hydrocarbons in a single-stage direct process and is expected to improve efficiency with less loss per conversion. On the other hand, as described below, this process requires the activation of CO₂ with low reactivity and improvement of the selectivity to the target hydrocarbons, which requires the development of highly active and selective catalysts.
2.2 Hydrocarbon synthesis by direct hydrogenation of CO₂
Hydrocarbon synthesis by direct hydrogenation of CO₂ is expressed in Equation (1) using ethylene as an example. The reaction is exothermic with an enthalpy change of −128 kJ/mol.
The reaction is considered to proceed by the FT reaction between CO and hydrogen via CO that is intermediately generated on the catalyst surface. Therefore, the selectivity of the product hydrocarbon is expressed as the Anderson-Schulz-Flory (ASF) distribution(11) using the C-C chain growth probability α of the carbon intermediates on the catalyst surface as shown in Equation (2):
where xn is the fraction of hydrocarbons. The subscript “n” is the number of carbon.
Figure 2 illustrates the carbon number distribution of hydrocarbons as predicted by the ASF distribution. Figure 2-(a) shows the calculated values at chain growth probability α = 0.6 as a case in which the chain growth of carbon intermediates on the catalyst surface is relatively slow and more light hydrocarbons are produced. Figure 2-(b) shows the calculated values for a chain growth probability α = 0.9 as a case in which growth proceeds to produce heavier hydrocarbons. If the target substances are lower olefins, an α value of 0.5 to 0.7 is desirable to increase the selectivity to C2 to C4 hydrocarbons. The figure also shows that heavy hydrocarbons can be synthesized with a high selectivity when the α value is 0.9 or greater if the target materials are liquid hydrocarbons, which are precursors for SAF. The chain growth probability α value is determined by the reaction conditions, such as the catalyst type, temperature, and pressure, and it must be optimized for the target substance.
Meanwhile, to synthesize the final target substance, after CO₂ and hydrogen are converted to hydrocarbons by a catalyst, post-treatment and refinement are required as downstream processes. Figure 3 shows the overall process configuration of hydrocarbon synthesis for SAF production. Existing jet fuels have carbon numbers in the range of C8 to C16, so if hydrocarbons containing heavy components are synthesized as shown in Fig. 2-(b), for example, the hydrocarbons must be reformed to maximize the C8 to C16 components through downstream processes called cracking or hydrogenation in order to make the hydrocarbons lighter. After that, the components corresponding to SAF, the target substance, can be extracted by distillation. As shown in this example, for hydrocarbon synthesis from CO₂ and hydrogen, it is necessary to construct the entire process, including hydrogenation, cracking and distillation.
3. IHI Group’s approach to hydrocarbon synthesis from CO₂
3.1 Synthesis of lower olefins by a multi-stage reaction system
As mentioned above, one technical challenge in the production of hydrocarbons from CO₂ is the efficient reaction of CO₂, which has low reactivity. As shown in Equation (1), water is produced as a byproduct in the reaction to form lower olefins. By removing the byproduct water, the equilibrium should be shifted toward the product side, consequently the CO₂ reaction rate could be improved. To test this hypothesis, we built a prototype multi-stage reaction system consisting of three systems with heat exchangers in-between in series, and then cooled the product gas stream of each reaction system to remove the byproduct water along with liquid hydrocarbons. Figure 4 illustrates the performance of lower olefins synthesis in a multi-stage reaction system. The catalyst used was a highly active Fe-based catalyst developed in collaboration with the Institute of Sustainability for Chemicals, Energy and Environment (ISCE2) under A*STAR of Singapore(12), (13).
Figure 5 shows the CO₂ conversion rates and lower olefin yields at the outlet of each stage of the reaction system. As predicted, the CO₂ conversion rate increased along with the number of reaction system stages, with a conversion rate of 41% in the first stage, and as high as approximately 80% in the third stage. The yield of lower olefin also improved with each stage, eventually increasing about twofold. These results confirm that a multi-stage reaction system with the byproduct water removed can achieve high CO₂ conversion rates and lower olefin yields without the need for a recirculation process. During a long-term durability test for approximately 1 000 hours, both CO₂ conversion rates and lower olefin yields were observed to be stable in the multi-stage reaction system.
3.2 Synthesis of liquid hydrocarbons for SAF
Figure 6 shows the appearance of liquid hydrocarbons synthesized from CO₂ and hydrogen using the developed Fe-based catalyst and the results of analysis of carbon number distribution by gas chromatography using a hydrogen flame ionization type detector (FID-GC) as an example. The results of this analysis indicate that the synthesized liquid hydrocarbon product mainly contains hydrocarbons with carbon numbers ranging from C8 to C35. It was also confirmed that the product contained many components with carbon numbers from C8 to C16, which are main components required for SAF. Since the product also contains components heavier than those required for SAF, the fuel components equivalent to SAF can be synthesized by cracking and hydrogenation of this liquid hydrocarbons and a small amount of wax contained, as shown in Fig. 3, and finally extracted through distillation.
3.3 Toward implementation of technology to produce hydrocarbons from CO₂
Figure 7 shows a schematic of the main manufacturing flow from crude oil through to resin and plastic products. In a topper, crude oil is first separated and refined into naphtha, gasoline, kerosene, jet fuel, and other materials according to its boiling point. Lower olefins, which are feedstocks for resins and plastic products, are produced by cracking separated naphtha in a facility called a naphtha cracker and then separating and refining the naphtha. Ethylene and propylene, which are lower olefins, are further separated by distillation and polymerized to resin pellets, which are then processed and molded into the end-product.
The carbon neutral lower olefins synthesized from CO₂ and hydrogen that the IHI Group is working on can reduce the carbon footprint of end-product resin and plastic products by replacing parts of existing value chains. We believe that we can advance CO₂ reduction by increasing the amount of substitution and by making better use of existing naphtha-based facilities and commercial distribution.
Regarding SAF, the current quality of synthetic jet fuel is defined in the ASTM D7566 standard, which allows a certain amount of SAF to be blended with conventional petroleum-derived fuel, depending on the type of SAF. Making the most of this feature, SAF synthesized from CO₂ is expected to be increasingly introduced as an aviation fuel.
4. Conclusion
Materials made of hydrocarbons and liquid fuels for medium- and long-distance transportation are the most difficult to replace by electrification etc. This paper describes the principle and features of the processes for catalytic synthesis of lower olefins and SAF from CO₂ and hydrogen, as well as the development status and envisioned implementation of the processes within the IHI Group. To implement the technology, we will continue to evaluate fuel eligibility under the Carbon Offsetting and Reduction Scheme for International Aviation (CORSIA), which defines sustainability for SAF, as well as adaptation to ASTM D7566, the standard that defines quality for SAF. In the future, we will implement these technologies that can reduce society’s carbon footprint in order to realize the carbon cycle and to contribute to the advancement of carbon neutrality in the fields of chemical feedstocks and liquid fuels, which has been considered difficult to achieve with conventional technologies.
— Acknowledgments —
Part of this paper was commissioned by the New Energy and Industrial Technology Development Organization (NEDO) as part of the “Development of Technologies for Carbon Recycling and Next-Generation Thermal Power Generation / Development of Technologies for CO₂ Reduction and Effective Utilization / Development of CO₂ Utilization Technology for Chemical Products / Development of Lower Olefin Production Technology by Direct Synthesis Using CO₂” project, and we express our deep appreciation to all those involved.
REFERENCES
(1) UNITED NATIONS:PARIS AGREEMENT, https://unfccc.int/sites/default/files/english_paris_agreement.pdf, accessed 2023-03-01
(2) Global Carbon Project:Global Carbon Budget 2022, https://www.globalcarbonproject.org/carbonbudget/index.htm, accessed 2023-03-01
(3) BP p.l.c.:bp Energy Outlook 2022 edition, https://www.bp.com/content/dam/bp/business-sites/en/global/corporate/pdfs/energy-economics/energy-outlook/bp-energy-outlook-2022.pdf, accessed 2023-03-01
(4) T. Ren, M. Patel and K. Blok:Olefins from conventional and heavy feedstocks: Energy use in steam cracking and alternative processes, Energy, Vol. 31, Iss. 4, (2006), pp. 425-451
(5) Q. Zhang, S. Hu and D. Chen:A comparison between coal-to-olefins and oil-based ethylene in China:An economic and environmental prospective,Journal of Cleaner Production, Vol. 165, (2017), pp. 1 351-1 360
(6) R. Geyer, J. Jambeck and K. L. law:Production, use, and fate of all plastics ever made, Science Advances, Vol. 3, Iss. 7, DOI: 10.1126/sciadv.1700782, (2017)
(7) ICAO:Sustainable Aviation Fuel (SAF), https://www.icao.int/environmental-protection/pages/SAF.aspx,accessed 2023-03-01
(8) H. Kamata:Robust Catalyst for CO₂ Conversion to Synthetic Fuels and Chemicals,IHI Engineering Review, Vol. 54, No. 2, 2021
(9) H. Kamata:Development of Technology for Conversion of Carbon Dioxide into Fuel and Chemical Feedstock, Chemistry & Education, The Chemical Society of Japan, Vol. 70, No. 10, 2022, pp. 468-471 (in Japanese)
(10) H. Kamata: Synthesis of Fuels and Chemical Feedstocks by Catalytic Conversion of Carbon Dioxide, Catalyst and Reaction Engineering Contributing to Carbon Neutrality (Recent Chemical Engineering 71), The Society of Chemical Engineers, Japan, Vol. 71, January 2023, pp. 148-159 (in Japanese)
(11) J. Patzlaff, Y. Liu, C. Graffmann and J. Gaube:Studies on product distributions of iron and cobalt catalyzed Fischer-Tropsch synthesis, Applied Catalysis A:General, Vol. 186, Iss. 1-2, (1999),pp. 109-119
(12) H. Kamata et al.:OE402 Catalytic CO2 Conversion by Fe based Catalyst to Produce Lower Olefins for Greener Plastic Production, The 9th Tokyo Conference on Advanced Catalytic Science and Technology (TOCAT9),Fukuoka Japan,(2022. 7. 28)
(13) N. Mizukami, H. Kamata and T. Hashimoto : 2P57 Performance Evaluation of Catalysts for Production of Lower Olefins Using CO₂, “Carbon Dioxide Conversion” Session, 131st CATSJ Meeting, Yokohama Kanagawa Japan, 2023-03-17 (in Japanese)