Accelerating the Realization of a Decarbonized and Carbon Recycling Society with Carbon Recycling Technologies Integration of CO2 capture technology with CO2-to-valuable product conversion technology
IHI Corporation
We propose an economically excellent system that combines CO2 capture technology with CO2-to-valuable product conversion technology in order to accelerate the realization of a carbon recycling society in which the CO2 in various gases present on the earth’s surface is converted, as a carbon source, into valuable products, such as fuels and chemical products.
- ENDO Takumi
- Carbon Solution Department, Engineering Center, Carbon Solution Business Unit, Resources, Energy & Environment Business Area, IHI Corporation
Introduction
Given the global trend toward decarbonization, realizing a carbon recycling society is an urgent issue. As a means to do so, carbon recycling is attracting attention. Considering CO2 as a carbon source, carbon recycling converts CO2 into various valuable products (e.g., hydrocarbons) by reaction between CO2 and hydrogen (H2). The IHI Group is developing not only technologies to capture CO2 but also technologies to produce hydrogen efficiently and to convert CO2 into valuable products. Combining these technologies will eventually make it possible to realize a world in which the carbon sources present on the earth’s surface (CO2 emitted when biomass is used as an energy source and CO2 in the atmosphere) are used instead of using fossil fuels mined from the ground, thereby preventing the amount of CO2 in the atmosphere from increasing. This article introduces methanation and olefination as typical technologies for converting CO2 into valuable products.
In methanation, CO2 is converted into methane (CH4), which can be used as a fuel. This method produces methane gas, which is a primary component of city gas. Thus, CO2 emissions can eventually be reduced while using existing local infrastructure (e.g., the city gas network and residential gas stoves). This means that even in households and plants, CO2 can be reduced without introducing special facilities. However, the cost of methanation is significantly higher than that of natural gas because of CO2 capture costs and hydrogen supply costs; therefore, cost reduction measures are necessary. We propose a method for combining CO2 capture facilities and methanation or other valuable product conversion facilities into a single system to reduce total costs.
In addition, the details of technology to convert CO2 into lower olefins (olefination), which can be used as a raw material for plastics, will be described later. Lower olefins have a chemical structure in which two to four carbon atoms are connected (at least two are connected by a double bond). They include ethylene, propylene, and butene, which are used as raw materials for many major basic chemicals. For example, plastic bottles, polyester fibers, foamed polystyrene, and synthetic rubber are produced from lower olefins. In general, olefins are produced by decomposition of naphtha (light petroleum oil), but using CO2 as a raw material makes it possible to produce plastics with reduced CO2 emissions from their raw materials and production processes, thereby contributing to the realization of a carbon recycling society.
Integration of CO2 capture technology with valuable product conversion technology
Among the numerous CO2 capture technologies, the chemical absorption method is an excellent technology that uses an alkaline solution (e.g., amine solution) as a solvent, and captures CO2 from combustion flue gas by chemical absorption and desorption reactions. More specifically, as shown in the flow diagram for the integration of CO2 capture with CO2-to-valuable product conversion technologies, combustion flue gas from the power plant is attracted into the absorber and brought into contact with a CO2-lean solvent so that the CO2 in the flue gas is selectively absorbed by the solvent. The solvent that has absorbed CO2 is then sent to the stripper and heated in order to separate the CO2 absorbed by the solvent as a gas. Next, the gas is cooled and compressed to capture CO2 at a high purity of at least 99%. In this capture process, as shown in the CO2 capture cost structure chart, consumption of “regeneration energy,” which is required to strip CO2 from the solvent in the stripper, accounts for almost half the total cost, causing a great economic impact.
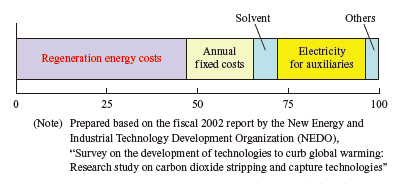
To address this, the IHI Group has developed a technology to reduce regeneration energy consumption, and has demonstrated with a pilot plant that it can reduce the regeneration energy cost by approximately 40% from that of the conventional process.
With a CO2 capture system alone, there is a need to procure regeneration energy for CO2 capture from an external system, but in a process that combines CO2 capture with CO2-to-valuable product conversion, the heat generated by the valuable product conversion reaction can be used as regeneration energy for CO2 capture. For example, in a process that combines a CO2 capture system with a methanation system, the CO2 captured by the CO2 capture system is introduced, together with hydrogen, into the methanation reactor in order to produce CH4 in the reactor. With this reaction, heat of 165 kJ is generated per mol of CO2 as expressed by the following reaction formula:
CO2 + 4H2 → CH4 + 2H2O ΔH0298 = -165 kJ/mol
Capturing CO2 with a CO2 capture system requires energy from the outside, but if this value is smaller than the amount of heat generated by the methanation reaction, combining the CO2 capture system with a methanation system enables a process that effectively requires no heat (steam) from the outside. With the regeneration energy reduction technology that the IHI Group has developed for the CO2 capture system, overall process efficiency can be enhanced with adequate thermal self-sustainability, thus significantly reducing running costs.
In addition, hydrogen production requires a process using thermal energy in which the heat generated by the methanation reaction can be used. Further cost reductions can be expected by effectively using thermal energy throughout the entire process of CO2 capture, hydrogen production, and valuable product conversion.
CO2-to-fuel conversion technology : Methanation
The IHI Group has been positioned to lead Japan in development of CO2 capture technology. The IHI Group started development of CO2 capture technology prior to development of valuable product conversion technology, and has completed demonstration of oxygen combustion technology and the aforementioned amine absorption method. For details on oxygen combustion technology, refer to Study Results in Demonstration Operation of Oxyfuel Combustion Boiler for CO2 Capture (IHI ENGINEERING REVIEW, Vol. 43 No. 2). Our development originally aimed at upsizing, assuming that the captured CO2 would be stored underground. However, many challenges remain to be solved, including economic performance, policies and systems, and public acceptance (the understanding and acceptance of local residents), solution of which is expected to take much time. Therefore, there is a need to develop a technology for converting captured CO2 into valuable products and to utilize such products instead of storing CO2 underground, and methanation is one such technology.
The IHI Group has developed a catalysis technology that converts a synthetic gas (syngas: a mixture gas of H2 and CO) produced by gasifying coal or biomass into methane. To apply this technology for carbon recycling, the IHI Group is developing a technology that captures CO2 contained in flue gas and reacts it with H2 in the presence of catalyst to produce methane gas. By converting CO2 from fossil fuel utilization (e.g., in thermal power plants, ironworks) into methane gas with this method and introducing the methane gas into existing city gas pipelines, CO2 emissions from households and plants can be significantly reduced, thus taking one step closer to carbon recycling.
To accelerate this research and development, the IHI Group began joint research with the ICES (Institute of Chemical and Engineering Sciences), an affiliate of A*STAR (Agency for Science, Technology and Research) of Singapore in 2011, and developed a highly active, long-life catalyst. We completed evaluation of this catalyst with test equipment in Singapore and at IHI Yokohama Works, and as of 2020, we are conducting research using CO2-free hydrogen and plan to conduct a demonstration test at the Soma IHI Green Energy Center.
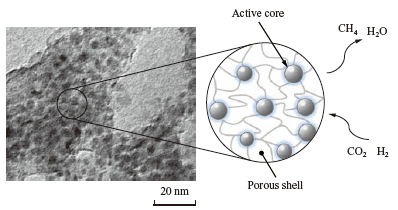
CO2-to-chemical conversion technology : Olefination
To convert CO2 into more valuable materials, the IHI Group is developing technology to convert CO2 into lower olefins, which are raw materials used for resins such as plastics.
Olefins are produced by the decomposition of naphtha (obtained by fractional distillation of heavy oil) with naphtha cracker, and are supplied to chemical plants. On the contrary, olefination technology enables the olefins synthesized by CO2 captured from flue gas to be used as an alternative to chemical raw material-derived olefins. This means that with olefination technology, like with methanation technology, products’ carbon footprints can be reduced without significantly modifying existing infrastructure, thereby contributing to reducing total CO2 emissions.
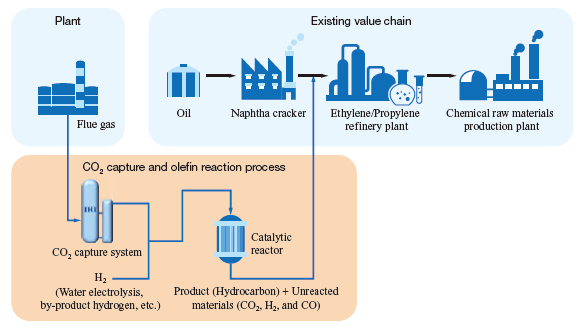
Olefins are produced from CO2 mainly by ① using CO2, which is not reactive, after converting CO₂ into CO by aqueous reverse shift reaction (FT (Fischer-Tropsch) reaction); ② converting CO2 to methanol and dimethyl ether (DME), then dehydrating them (MTO (Methanol-To-Olefin) reaction); or ③ directly hydrogenating CO2. The features of each method are described in the table. The IHI Group is developing a method to hydrogenate CO2 in a single step with Fe nano-catalyst and synthesize lower olefins (CO2- FTO (CO2-Fischer-Tropsch to Olefin) reaction), which is classified as ③ (a method for directly hydrogenating CO2). With this method, CO2 is synthesized directly into lower olefins without first converted into CO or methanol, which we expect can significantly reduce equipment and running costs. As for this catalyst, like the methanation catalyst, the IHI Group is conducting joint development with the ICES.
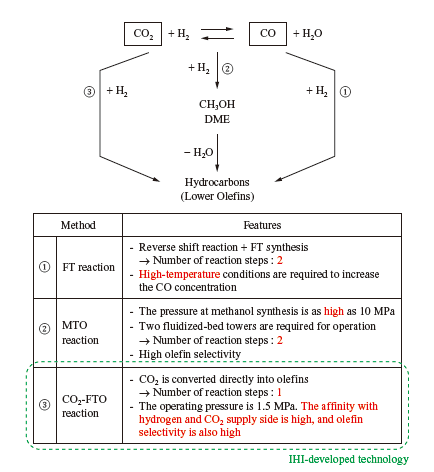
In general, in an FT reaction, which uses CO as a raw material, Fe catalyst has a higher olefination rate, and has high selectivity in synthesizing hydrocarbons, which are lower olefins. Therefore, Fe catalyst is expected to be used to synthesize lower olefins from CO2. The reaction for directly hydrogenating CO2 to synthesize olefins is expressed as follows:
nCO2 + 3nH2 → (CH2)n + 2nH2O
However, in the actual catalytic reaction, not only lower olefins but also heavier olefins (n in the above formula is 5 or more) and paraffin hydrocarbons (all carbon atoms are connected by a single bond) are generated. The carbon mole fractions of different hydrocarbons with the enhanced Fe nano-catalyst developed jointly by IHI and ICES are shown in the figure. Approximately 40% of the hydrocarbons generated with this catalyst (carbon mole fraction: 0.4) are lower hydrocarbons of C2 to C4, but the distribution differs greatly depending on the catalyst composition as well as the reaction temperature and pressure. In addition, the yield differs depending on the catalyst reduction and activation conditions. Therefore, we will study the catalyst composition, activation method, and operating conditions in order to maximize the yield of lower olefins and conduct demonstrations.
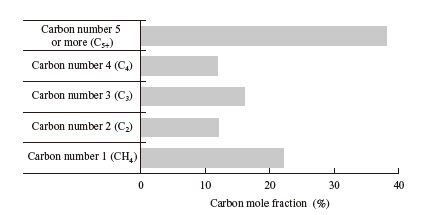
Future development of valuable product conversion technology
New value can be created for CO2 capture by converting CO2, as a carbon source, back into valuable products for carbon recycling instead of incurring capture and storage costs to reduce CO2 emissions. The IHI Group will continue to develop technologies and business for methanation and olefination to achieve their early commercialization. In addition, we consider the stable supply of hydrogen, which is another raw material for these technologies, to be essential. Using our technologies to make effective use of renewable energy sources around the world, the IHI Group will offer total solutions for reducing CO2 emissions, thereby contributing to the realization of a carbon recycling society.