Development of the Z-PELLER® for Electric Propulsion Vessels Aiming at electrification of marine propulsion units and utilization of renewable energy
IHI Power Systems Co., Ltd.
Development of an electric propulsion system and the building of a port and harbor system utilizing renewable energy are underway for decarbonization. This article introduces activities of IHI Power Systems Co., Ltd. as a System Integrator.

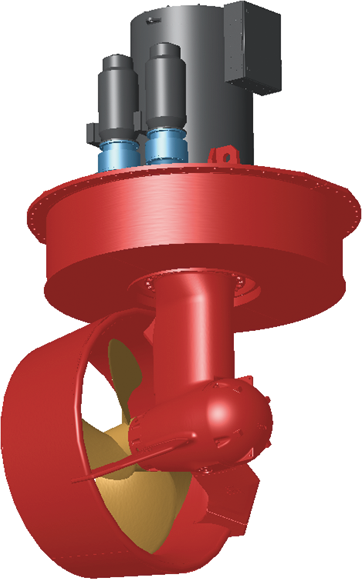
Introduction
As a measure toward decarbonizing the shipping industry, the IMO (International Maritime Organization) agreed to and adopted a commitment to reduce the industry’s GHG (greenhouse gas) emissions by 50% compared to 2008 by 2050.
The development of internal combustion engines is on-going to diversify into fuels such as hydrogen and ammonia amid an increased awareness of decarbonization. Moreover, there is growing demand for electrification in the marine propulsion unit market, which is being driven by falling battery costs in recent years. Furthermore, it may be possible to achieve complete decarbonization if electricity is supplied to batteries from renewable energy sources.
IHI Power Systems Co., Ltd. (IPS) is developing various types of equipment for creating an electric propulsion system and taking advantage of renewable energy. This article introduces its activities.
Electrifying Z-PELLER®
Z-PELLER made by IPS
One of the main products of IPS is Z-PELLER, a trade-marked 360-degree rotatable propulsion unit (azimuth thruster) mainly for tugboats.
Tugboats, which are small boats roughly 30 m long used in managing ports and harbors, help large vessels that can measure hundreds of meters long to dock at and leave ports by pushing or pulling them. Sometimes, the tugboats lead the sea route to offshore. Tugboats therefore require high maneuverability and significant power, and Z-PELLER gives them such abilities.
Z-PELLER is a propulsion unit that enables operators to adjust the propeller’s thrust direction in any direction (a full 360 degrees), thereby eliminating the need for a conventional rudder. The propeller is surrounded by a Kort nozzle, which has a wing-shaped axial cross-section that serves to generate high thrust.
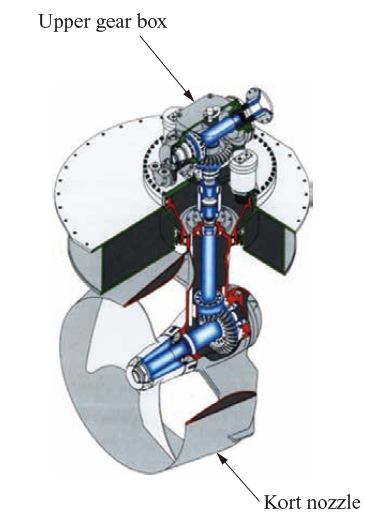
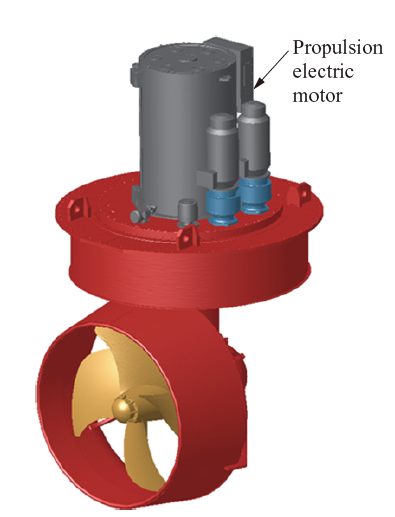
Z-PELLER equipped with an electric motor
IPS developed the electric-motor-equipped Z-PELLER to meet growing market demand for electrification. For propulsion, a vertical electric motor replaces the upper gear box that is directly connected to an internal combustion engine in a conventional Z-PELLER.
The electric propulsion motor is equipped with a permanent magnet motor (PMM) that uses permanent magnets in the rotor. Compared with induction motors, which have been the main conventional electric motors used to date, PMMs are smaller and more efficient. Mounting the PMM vertically eliminates the need for the upper gearbox, thus reducing mechanical losses. This results in a more efficient propulsion unit than the conventional one directly connected to an internal combustion engine.
Electric propulsion eliminates the need for the long intermediate shaft and upper gearbox required in the conventional directly connected to internal combustion engines, as well as their accompanying lubricating system and piping. The simplified mechanical configuration not only saves space but may also reduce the workload by removing the need for piping and shaft centering work.
Electric steering method
In line with electrifying the propulsion unit, IPS has also electrified the steering unit. Our conventional steering unit used a hydraulic pump and hydraulic motor. Changing to an electric steering method with a versatile induction motor and inverter shrinks the unit and makes it more efficient than that of the hydraulic steering method.
Whereas a hydraulic steering method comprises complex hydraulic equipment and piping laid out intricately, the electric steering method only requires an induction motor and inverter, which simplifies the unit and eliminates the workload for piping work — just as with electrification of the propulsion unit. In addition, the electric steering method requires simpler control logic than that of the hydraulic steering method.
A complex logic is needed for controlling a hydraulic pump and valves in a hydraulic steering method, whereas the electric steering method only needs an electric motor control with an inverter. Its characteristics include, because the induction motor and inverter are electrically controlled, electric motor control is much more responsive and easier to control and adjust than hydraulic control. In addition, general-purpose devices can be used for the induction motor and inverter.
As an Electric Propulsion System Integrator
Internal combustion engine-driven hybrid system
IPS has an internal combustion engine-driven hybrid system in which a small motor is added to the conventional Z-PELLER directly connected to an engine, and the small motor is powered by batteries and power generators. We have delivered a package of power generators and a battery, as well as a package of power generators alone, as a power source for a small motor for a tugboat. It has been more than five years since a vessel equipped with the internal combustion engine-driven hybrid system was completed, and it still operates smoothly.
The internal combustion engine-driven hybrid system, in which the engine is directly connected to the propeller through an intermediate shaft, becomes highly efficient when the engine’s load range exceeds a certain level due to the engine’s characteristics, which is a huge advantage. On the other hand, the presence of the intermediate shaft has the drawback of restricting the range of equipment configurations.
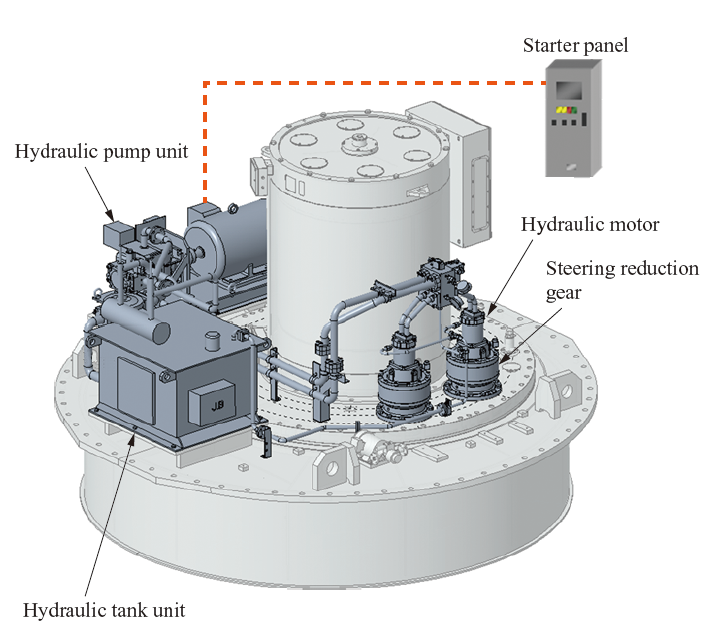
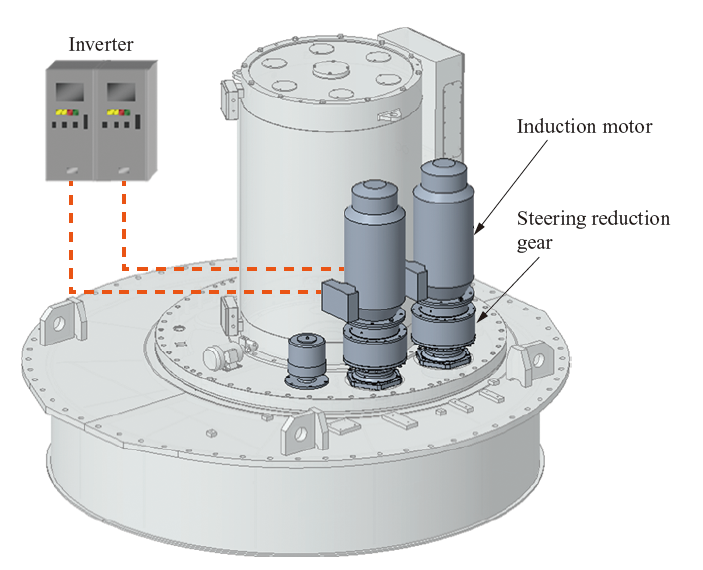
Electric motor-driven hybrid system
An electric motor-driven hybrid system, in which there is no intermediate shaft that makes the internal combustion engine-driven system disadvantageous, gives vessels more flexible equipment layout options. Another benefit of this hybrid system is that the motor of the electric motor-equipped Z-PELLER can be connected to various types of vessel’s internal power supply, just as various types of equipment can. This enables vessel owners to customize vessels to their needs. Whereas a conventional system uses an AC (alternating current) collective switchboard for its power source, this system uses a DC (direct current) collective switchboard, which is now becoming the mainstream. This will easily enable hybridization of various possible power sources in the future, such as power generators, batteries, and fuel cells.
The system also allows flexible changes to the equipment’s output balance according to the type of vessel, operating mode, and requirements. In the case of a tugboat, the system can optimize the output and quantity of the main power generators and battery capacity in line with the operating time and load.
- How the hybrid system works
- IPS analyzes the operating data from Z-PELLER-equipped tugboats and uses the results as feedback to develop an electric propulsion system. The results of the analysis show that most of the operations last for a short period of time. Most of the operation time is occupied by low loads, and high loads only account for a very small amount of the operation time.
In a zero-emission mode, the system can work with batteries alone when operating with a low load and the batteries providing extra power, thus eliminating the vessel’s GHG emissions.
In a low-load mode, the system runs the power generators to charge the batteries when the system operates under a low load and the batteries are empty. The system optimizes the number of working generators and their operating conditions to maintain high efficiency.
In a high-load mode, the system supplies the power needed by running power generators during high-load operations and charging/discharging power from the batteries.
As stated above, the hybrid system enables efficient operation suitable for load conditions. - Installing batteries and electric equipment in a tugboat
- Considering their durability and performance, most currently available batteries must be used at 25°C or lower. They are cooled with air conditioners in a battery room, since air cooling is generally used as the cooling method these nowadays.
Electric equipment, including air conditioners to cool down batteries, allows for flexible layouts. Accordingly, there are fewer restrictions on the vessel’s layout, and the hull shape can be optimized. As such, employing an electric propulsion system can increase efficiency not only for the propulsion system but also in systems throughout the vessel.
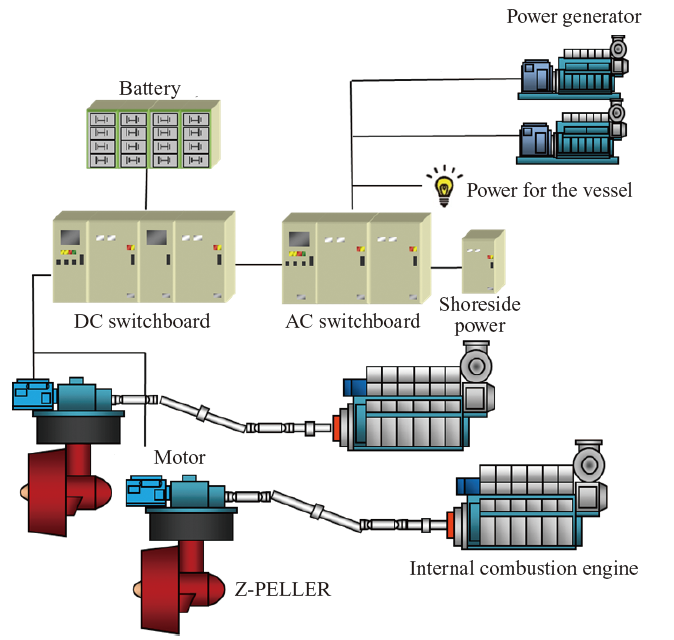
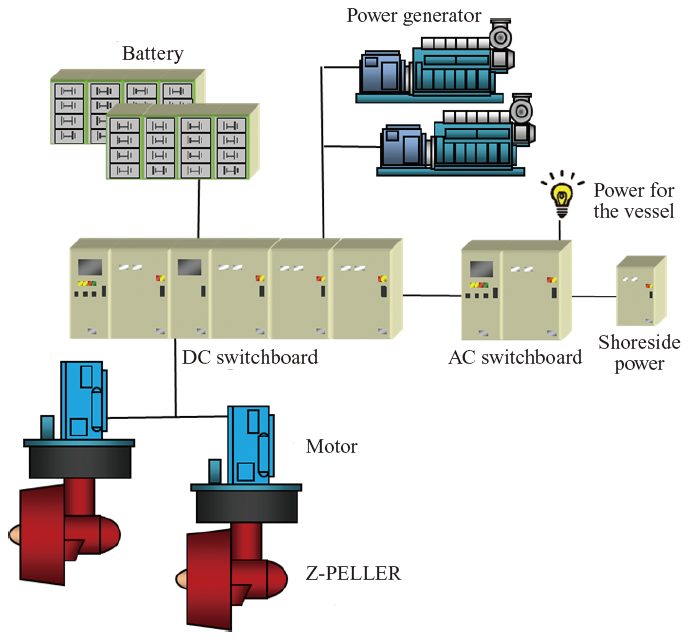
Battery-powered tugboats and use of renewable energy at ports and harbors
It can be said that tugboats are suitable to be powered solely by batteries due to how they operate. When it comes to costs, however, it is currently too expensive and impractical to supply all the necessary power with batteries. Further advances in battery technology are required to actualize this.
In general, batteries on vessels are charged by equipment on land when the vessels return to port. However, in the near future, if the renewable energy sources such as solar and wind power can be used to power the batteries, it will promote decarbonization.
Furthermore, it will also be possible to charge batteries onboard during break times between operations without returning to port if vessels can use seaborne power-supply systems such as wind-power and tidal-power generators, vessels equipped with solar power generators, as well as renewable energy systems on land.
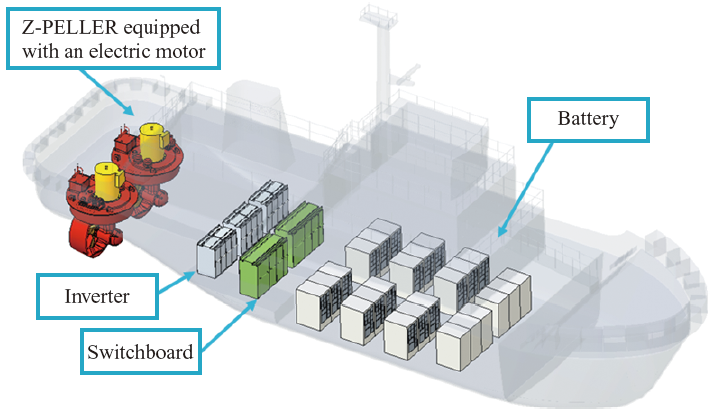
While various types of vessels equipped with batteries are now being built, they need batteries with excess battery capacity for fear of running out. Here is where IoT technology can be applied to manage power supply and operation to enhance operating efficiency. If the need for excess battery capacity no longer exists and the effect of reducing battery capacity is reflected in the hull price, the vessels completely driven by batteries will become widespread. Electrification of the entire port and harbor system, utilizing renewable energy equipment and IoT technology, will then be achievable.
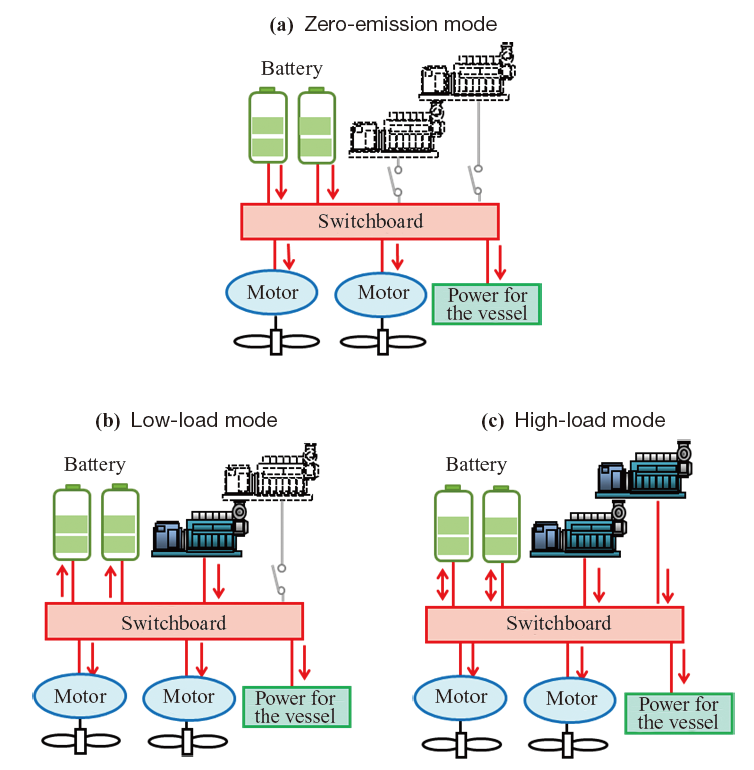
Conclusion
Technology for equipment that comprises electric propulsion systems has been advancing year by year and has been adopted in more and more places. No doubt, the day is coming when these systems will become common as their prices fall and efficiency rises.
Electrification has become widespread amid restrictions to reduce environmental burdens and increasing pressure from society at large. In response, IPS, as a System Integrator, must take the lead in the market and continue to put forward new technologies.
IPS will quickly complete a ship powered solely by batteries to achieve true zero-emissions. Furthermore, IPS will use green hydrogen, green ammonia-fueled power generation systems and renewable energy sources as power supply sources. We are hoping to advance the reality of decarbonized vessels with an electric propulsion system whose main equipment is Z-PELLER.