Historical Structure

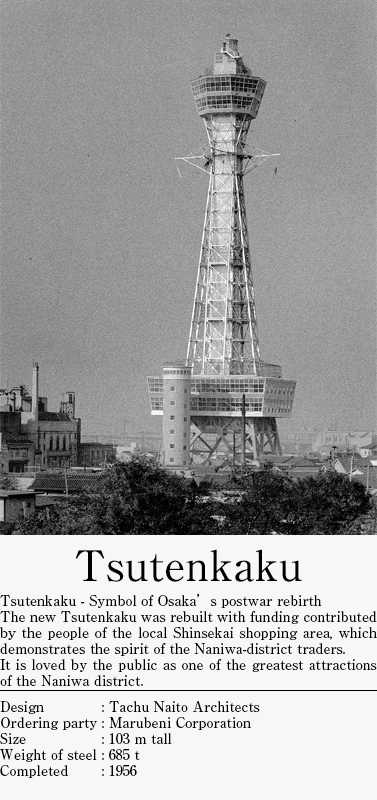
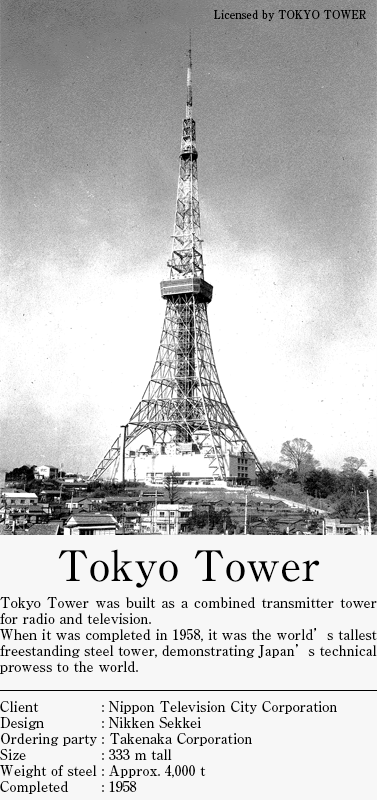
Tsutenkaku
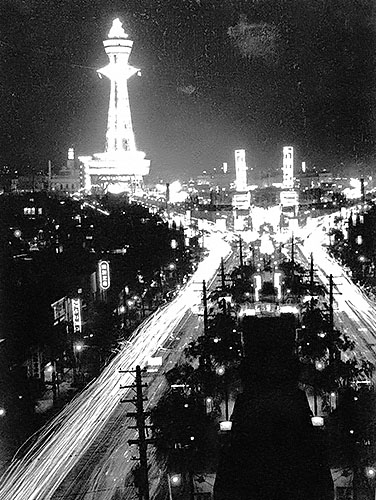
Tsutenkaku, which appears in the song “Osho” (King) about the shogi (Japanese chess) player Sankichi Sakata, stands right in the middle of the bustling district known as Shinsekai (New World).
The current Tsutenkaku is the second on the site. The original was built at the entrance of the Luna Park that opened on the site of the 5th national industrial exhibition. It drew many visitors as a famous Osaka attraction, but it was demolished during the war to provide metals for the war effort. The Shinsekai area, bereft of its symbol, faded after the war.
So the local traders of Shinsekai, hoping to recapture the bustle of years past, put their money together to build the current Tsutenkaku.
The rebuilt Tsutenkaku was 103 m tall, at a time the national building height restriction was 31 m, so it gave views of the Osaka-Kobe area, and even of Awaji Island in the distant Seto Inland Sea.
The overall construction was contracted to Okumura Corporation, and we built it entirely of steel frame, using 691 t of steel.
The steel used was mainly angles and other shaped steel sections, with riveting for all joints.
In the absence of technology to curve structural elements, their angles are varied a little at a time at their joints to assemble the shape.
There were no computers back then, so calculating points in three dimensions was a particularly tough struggle for those working on the project.
The positions of the numerous joints, and the angles of all the elements, mounted to follow inclines, had to be calculated manually. Working diagrams were drawn for each element, based on the calculations, and almost no parts were duplicated, so the volume of drawings to produce was enormous.
Parts were test-assembled before they were shipped, exercising extreme care over their fabrication. Despite these efforts, a major problem emerged once construction had reached 10 m above the ground.
One of the main columns was found to be tilted inwards by just 2 cm.
It had to be straightened up, but the structure had already been built up gradually from below, and its joints riveted. Surrounded by busy streets, there was no space to bring in heavy machinery or to install anchors, so it seemed that in the worst case, it might be necessary to cut all the rivets, temporarily disassemble the structure, and start over.
Just then, Yukio Shimada, in charge of the steeplejacks, noticed a sewer access cover in the road just 20 m from the site. An anchor was driven in at the bottom of the access hole and used with a winch and cable to the tilted column, to pull it up straight.
Yukio Shimada was a steeplejack working under Onishi Kensetsu, a longstanding and frequent visitor to our company. He later worked on the construction for the Symbol Tower at the Osaka Expo, and was the first steeplejack to be honored for his services. He was a legendary foreman who boasted that “someone who’d fall on the job is no steeplejack”.
Tokyo Tower
Tokyo Tower was modeled on the Eiffel Tower in Paris, but at 333 m, it stands 13 m taller, and was then the world’s tallest freestanding steel tower. Building a tower taller than Eiffel’s in Japan, one of the world’s most earthquake-prone countries and visited by many typhoons, using around half as much steel (3,700 t), and taking half a year less to build it (18 months), demonstrated Japan’s engineering strength.
When the construction plan was announced in the press, some experts questioned whether it could really be done.
People involved at the company remember a mood of unease, with some saying “can we build something with the required precision and quality, and get it done in the timeframe?”
Takenaka Corporation was the contractor for all works, and we worked with Shin Mitsubishi Jukogyo (now Mitsubishi Heavy Industries) to build the tower.
The portion we built went from the ground to 140 m (about 10 m above the first observatory), using 2,861 t of steel, about 75% of the total weight.
Those in charge of the work asked people who had worked on the earlier Tsutenkaku for advice.
The amount of calculation and number of pages for the working drawings expanded far beyond the work on Tsutenkaku.
To get a three-dimensional grasp of component shapes, we had to produce detailed, life-sized drawings from many directions.
At the stage of life-sized work, we had to devise construction methods and sequences.
For the fabrication work, we gathered together the leaders of the various task teams, and made sure everyone knew the overall structure, the position and purpose of each element, and the Relation / Overseas Basesship between each team’s work and the next process. In particular, the on-site joints of the main columns required metal-to-metal contact.
So the parts were assembled, all rivets were inspected, and any rivets which didn’t meet standards were cut and replaced.
To make the paint finish more uniform and raise its anti-corrosion performance, we shot-blasted all parts that had finished primary fabrication, immediately before assembly. After completely removing all rust and black scale, we applied the first primer coat.
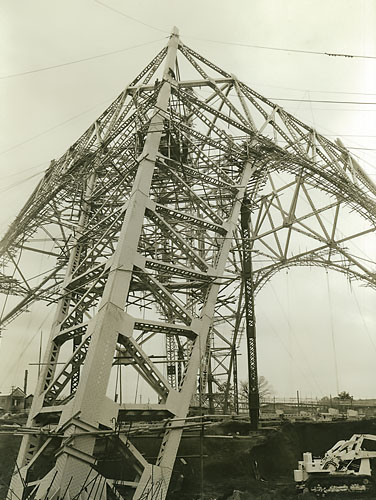