Toward Realizing Stable Commercial Operation of Biomass Power Plants Operation results of the biomass-fired circulating fluidized bed boiler and efforts to increase operating rate
IHI Corporation
In January 2019, the Nanatsujima Biomass Power Plant, which has an output of 49 MW, began its commercial operation on IHI’s premises in Nanatsujima, Kagoshima City, Kagoshima Prefecture. Biomass power generation has a shorter history than conventional fossil fuel-fired power generation. This article introduces our problem-solving efforts to achieve stable operation and the operation results.
YOSHIDA Takeshi Basic Design Department, Engineering Center, Carbon Solution Business Unit, Resources, Energy & Environment Business Area, IHI Corporation
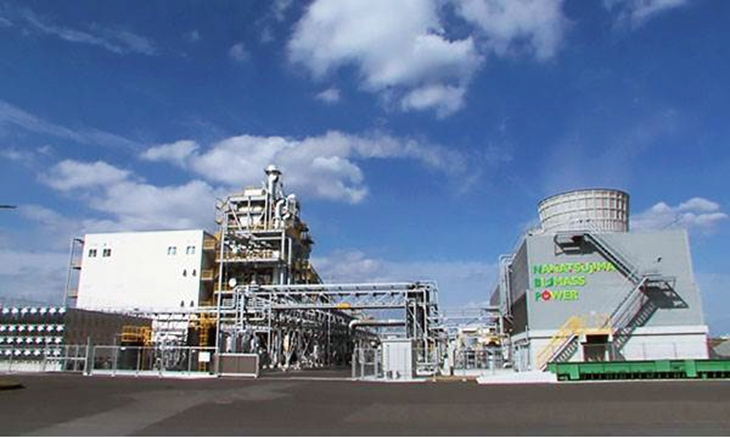
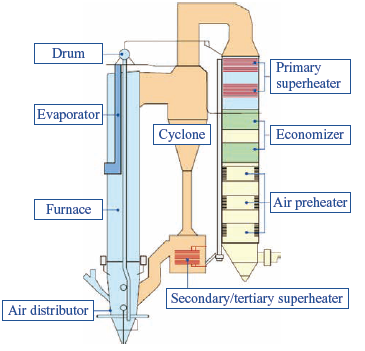
Nanatsujima Biomass Power Plant
In May 2016, the Nanatsujima Biomass Power LLC (NBP), which runs the Nanatsujima Biomass Power Plant, was established by IHI and eight investing companies. In January 2019, NBP started the commercial operation of this power plant. This power plant has an output of 49 MW, which can cover approximately 77 000 general households and contribute to an annual CO2 emissions reduction of approximately 200 000 tons. This power plant uses palm kernel shells (PKSs), wooden pellets, and forest thinnings. PKSs and wooden pellets are imported from abroad, but for forest thinnings, the fuel made in Kagoshima Prefecture is used. Approximately 15 000 tons of forest thinnings are consumed annually. Using forest thinnings contributes to revitalizing forestry and securing sustainable energy sources in Japan. IHI has been constructing coal-fired/waste-fired circulating fluidized bed (CFB) boiler plants for about 30 years. To operate this power plant, however, IHI has experienced various events unique to biomass fuel and acquired the know-how necessary for the maintenance. This article introduces our problem-solving efforts to increase the operating rate of the power plant.
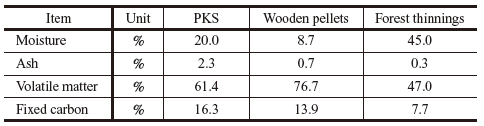
Abnormal combustion
This power plant adopts a CFB boiler. The CFB boiler increases the furnace temperature to 800°C to 900°C and concurrently sends combustion air to the bottom of the furnace to blow up fine sand in the furnace. This power plant, after increasing the furnace temperature in the same fashion, puts biomass fuel into the furnace and burns it. IHI’s CFB boiler operates simply in that fuel is supplied by means of gravity fall and at the same time pushed in by a sealing medium (e.g., air) for preventing the back flow of combustion air. Once fuel is put into the furnace, stable combustion is obtained with the heat held by a large amount of sand in the furnace, where even fuel with a high moisture content can easily be burned.
Biomass fuel is highly flammable especially in the dry state because it generally contains a lot of volatile matter. Biomass fuel sometimes turns into dry, fine particles in the process of drying, processing, or conveyance. We found that these fuel particles cause abnormal combustion in the fuel feed chute.
Through a detailed investigation, a cause of this abnormal combustion was presumed that some fuel particles accumulated in the fuel feed chute, which is exposed to radiation heat from the furnace (hot sand), and released volatile matter, eventually resulting in a fire.
Therefore, a basic measure to prevent such abnormal combustion is to ensure that fuel is fed smoothly into the furnace by eliminating the accumulation of these dry, fine particles in the fuel feed chute. To achieve this, we studied measures focusing on how to deploy the sealing medium into the fuel feed chute as well as the required amount of the sealing medium, and evaluated the effectiveness of these measures by means of flow analysis. Based on the evaluation results, we modified the equipment and improved their operation, and as a result, confirmed that safe, stable operation could be achieved.
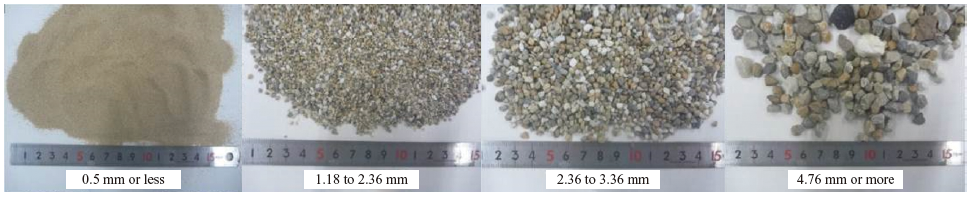
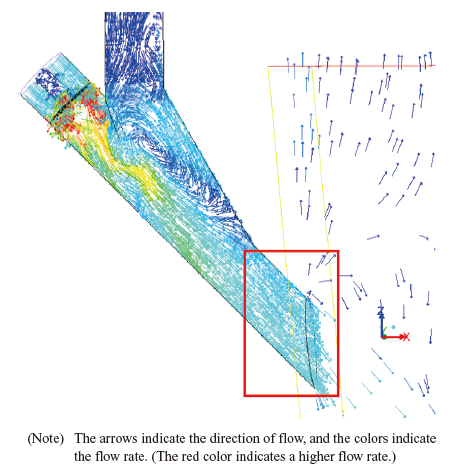
Changes in the sand in the furnace
In the combustion furnace of the CFB boiler, with the circulating fine sand and combustion gas, the fuel is ignited and burned stably, and the combustion heat energy is transmitted to the steam tubes (heat absorption). The hot sand, whose particle size has been adjusted appropriately, is kicked up by the upward gas flow in the combustion furnace. Some part of the sand falls while colliding with the heat transfer tubes around it and transmitting heat to the tubes. The other part of the sand flows along the gas flow, and is collected by the cyclone installed at the outlet located at the top of the combustion furnace, returned to the bottom of the furnace, and circulated repeatedly.
For conventional CFB boilers for coal-biomass co-firing, the sand is not replaced actively. The sand brought in with the fuel is screened with a vibrating screen to remove coarse sand, stones, and gravel, and only fine sand is used. However, the sand contained a lot of gravel and adequate heat absorption could not be achieved when this power plant was continuously operated without replacing the sand for several months after its commercial operation began.
In the initial stage of operation, silica sand consisting mainly of SiO2 (silica dioxide) was fed as fresh sand into the furnace after adjusting the particle size. We found that since combustion ash of biomass fuel contains a lot of alkaline metals (Na and K), alkaline components are concentrated in the fluidized sand bed and combined with silica sand, causing the sand to coarsen. The amount of fluidized sand that needs to be replaced depends on the concentration of alkaline components and the sand condition, but the equipment specifications and operation cost must assume sand replacement from the beginning.
For this power plant, we began replacing a certain amount of sand with fresh sand every day, since which gravel occurrence and poor heat absorption have generally been eliminated. However, especially when PKSs were used, the temperature distribution in the furnace sometimes changed depending on their origin. In addition, it was sometimes found at periodic inspections that sand particles or combustion ash became stuck and the size increased where their circulation was not smooth in the furnace. Although the operation is not hindered currently, if they become stuck and grow further, the circulation of the fluidized bed may be hindered, adversely affecting the operation. To address these events, it is necessary to establish a method for maintaining sand appropriately according to the type of fuel while monitoring the inside of the furnace and the condition of the fluidized sand.
Ash deposits in the flue gas ducts and economizer
The most difficult part we had is ash deposition in the flue gas ducts and on the heat transfer surfaces in the downstream side of the cyclone outlet, which has been lowering the operating rate since commercial operation began. The fuel gas ducts used in the CFB boiler, through which a gas with a high temperature of 800 to 900°C flows, are structured to have fire-resistant material with high strength and heat insulation on the inner wall of the casing. Combustion ash from biomass fuel generally contains alkaline components and is likely to form low-melting-point compounds. As the operation time increased, the ash deposits grew on the surface of the fire-resistant material of the fuel gas duct with low-melting-point compounds as binders. When this power plant had been operating for several months, the ash deposits grew several tens of millimeters thick. The ash deposits separated when the ambient temperature changed with the power plant output and fell onto the heat transfer surface immediately below them. The ash mass blocked the flue gas flow path, making continuous operation difficult.
As a result of flow analysis, the selective growth of ash deposits in the flue gas ducts where the gas flow rate was low was successfully reproduced. Therefore, we added a soot blower to spray steam over the areas where ash deposits rapidly to clean off ash and operated the soot blower at appropriate intervals, theeby reducing ash deposits.
Another thing that hindered operation is ash deposits in the economizer, which is located on the downstream side of gas flow. The economizer is a heat exchanger that recovers the heat taken by the combustion gas with a relatively low temperature into the boiler makeup water. The CFB boiler uses an economizer with straight fins, which can save space and provides a sufficient heat transfer area. However, economizers with straight fins have a disadvantage in their structure that it is difficult to obtain the desired cleaning effect of the soot blower due to the narrow flue gas flow path. We confirmed that in economizers with straight fins, biomass combustion ash deposits easily as well as ash from low-grade coal, such as subbituminous coal.
Currently, for the areas around the economizer with straight fins, where ash deposits are likely to grow, we have set the steam spray pressure of the soot blower and the spraying frequency to larger values. This has eliminated the need to clean off ash deposits except at semi-annual periodic inspections. Cleaning off ash deposits at periodic inspections requires a shutdown and takes a lot of labor, but is considered as an important item necessary not to lower the operating rate. Regarding this point, we are studying if there is any measure better than the current one.

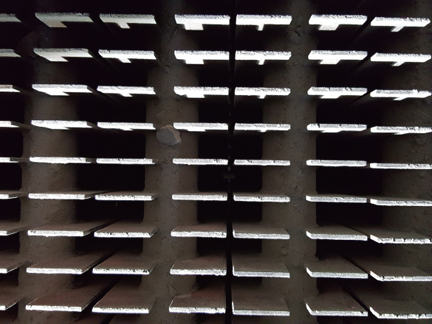
Measures for NOx emissions
On the island of Kyushu in Japan, a large part of the power demand is covered by the output of solar power generation. Therefore, in spring and fall, when the power demand is low, renewable energies may be subject to curtailment. CFB boilers have slow combustion at low temperatures of 800 to 900°C. Therefore, compared with conventional burner combustion boilers, CFB boilers emit less thermal NOx, which is produced when nitrogen and oxygen in the combustion air react at high temperatures. However, when the output is low, CFB boilers are operated with an excessive amount of air relative to the amount of fuel fed, and therefore, emit less NOx when the boiler load is low than when it is high. In addition, biomass fuel, which contains less fixed carbon than coal, reacts less to reduce NOx to Cl2 with unburned char. Therefore, CFB boilers are likely to emit more NOx when used with biomass fuel.
The NOx value of this power plant at the rated output is normally 80 to 100 ppm (corrected at 6% O2), which is higher than that of coal co-firing CFB boilers. The NOx emissions standard for this power plant is 150 ppm (corrected at 6% O2), and the NOx value at the rated output is sufficiently below this standard. Therefore, the boiler is not provided with NOx removal equipment, which requires chemicals such as ammonia. However, since 50% of load curtailment is expected in the future, we checked NOx emissions during low-load operation. For biomass fuel (PKSs, wooden pellets, and forest thinnings), we confirmed that, by adjusting the co-firing rate of forest thinnings, which contain a lot of moisture and have a low heating value, the NOx value at a load of 50% could be reduced to 130 to 150 ppm (corrected at 6% O2), below the control value.
Corrosion in the gas air heater (GAH)
The gas air heater (GAH) is a heat exchanger that recovers the heat taken by low-temperature combustion gas into combustion air to boost the boiler efficiency. CFB boilers require combustion air to be compressed and pushed into the furnace, and therefore, use a leak-free GAH consisting of many heat transfer tubes. The GAH is structured so that the air passes inside the tubes and the combustion gas, which contains ash, passes outside the tubes, and is provided with a soot blower to prevent ash from depositing on the heat transfer tubes. Since the combustion gas contains corrosive components, such as sulfur oxides, the heat transfer tubes around the air inlet, where the metal temperature is lowest, are likely to have low-temperature corrosion due to condensation of sulfuric acid or other chemicals. For this reason, measures against corrosion have been required, such as selecting sulfuric acid corrosion resistant steel for the heat transfer tubes and adopting a system for increasing the metal temperature of the heat transfer tubes to an appropriate temperature. However, it is difficult to prevent corrosion completely, and therefore, maintenance is scheduled assuming the need to replace the corroded parts in the medium-to-long term.
In November 2020, one year and 10 months after commercial operation began, we checked the corrosion condition of the GAH during periodic inspection. No signs of corrosion were confirmed when the heat transfer tubes were observed visually, and the wall thickness measurement results did not show any decrease in the wall thickness. The measures against corrosion for the GAH are considered to be effective and the biomass-fired CFB boiler has a milder corrosion environment than conventional coal-fired/waste-fired CFB boilers. The biomass-fired CFB boiler used in this power plant may have a varying sulfur content presumably because the sulfur content in biomass fuel is low, which will therefore be monitored continuously.
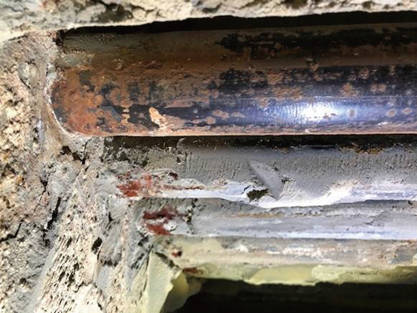
Future developments
About three and half years have passed since commercial operation began, and during this period, we have experienced various events unique to biomass fuel and acquired know-how on the planning, operation, and maintenance of biomass-fired power plants. As for the problem-solving efforts to increase the operating rate of the power plant, we have achieved some positive results. Meanwhile, as for ash deposits in the economizer with straight fins, we will study better measures and at the same time make proposals to improve feasibility and implement them.
Going forward, we will solve problems found in actual operation and obtain carbon-neutral, stable power sources, thereby contributing to realizing a carbon-free society.