Development of Diffusion Bonding Process by IHI Vacuum Hot Press
KAWAI Takuya, KONISHI Hiroyuki, NAKANOWATARI Isao
KAWAI Takuya : Business Solution Group, Product Solution Department, IHI Machinery and Furnace Co., Ltd.
KONISHI Hiroyuki : Manager, Business Solution Group, Product Solution Department, IHI Machinery and Furnace Co., Ltd.
NAKANOWATARI Isao : Manager, Process Solution Group, Product Solution Department, IHI Machinery and Furnace Co., Ltd.
In recent years, “diffusion bonding,” which enables precision bonding, direct bonding, and dissimilar material bonding, has been attracting attention. Diffusion bonding is a method of joining by bringing the components into close contact that cause as little plastic deformation as possible, thereby achieving a metallic bond between the bonded surfaces. IHI Machinery and Furnace Co., Ltd. (IMS) has been producing hot press equipment for diffusion bonding for nearly 40 years. There are two types of vacuum hot presses: a basic single-axis type and a multi-axis type for larger processed products and improved mass production. In recent years, IMS has been providing bonding process support service by developing not only vacuum hot presses, but also diffusion bonding processes. In order to expand the diffusion bonding market, this paper introduces the support system using IMS’s test equipment as well as support system.
1. Introduction
As part of the efforts toward a decarbonized society, advanced use of materials is expected to reduce material loss, reduce carbon emissions during processing, and improve productivity. Under these circumstances, “diffusion bonding,” which enables precision bonding, direct bonding, and dissimilar material bonding, has been attracting attention in recent years. Diffusion bonding technology has been used for a long time, but its unique features are now beginning to match the needs of the world, so people are taking a new look at this technology. This paper introduces the basics of diffusion bonding, development trends in vacuum hot presses, which are one of the main pieces of equipment needed for diffusion bonding, the development status of the diffusion bonding process, and the services provided by IHI Machinery and Furnace Co., Ltd. (IMS).
2. Overview of diffusion bonding
2.1 Positioning of diffusion bonding in joining technology
In manufacturing, joining technology is indispensable to assembling and bonding things together. Many joining methods have been developed, but each has its own advantages and disadvantages, and it is necessary to select the most suitable joining method according to the materials to be joined and the operating environment. Figure 1 shows the classification of joining methods. Diffusion bonding is classified as a material joining process that integrates the base materials to be joined, and is positioned as a type of solid phase joining. Solid phase joining is a method of joining base materials in a solid state without melting them during joining. The following sections describe the definition, principles, and features of diffusion bonding.
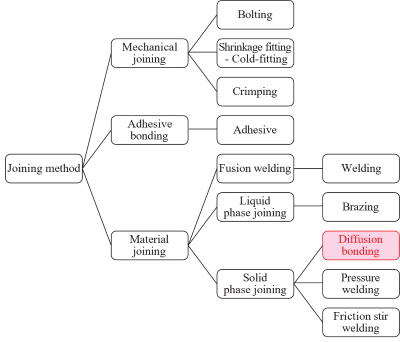
2.2 Definition of diffusion bonding
Diffusion bonding is a joining method specified in ISO/TR 25901-3 as “welding with pressure (2.1.2) whereby the workpieces are kept in contact under specified continual pressure and are heated either on their faying surfaces, or in their entirety at a defined temperature over a controlled time. This results in local plastic deformation and thereby intimate contact of the surfaces and diffusion of the atoms through the interface. This produces complete continuity of the material. The operation can take place in a vacuum, under a gas shield or in a fluid, preferably without the addition of a filler metal.” In addition, diffusion bonding is similarly defined as “diffusion welding” in ISO/TR 25901-3. It is also sometimes called “thermo compression welding” or “diffusion joining” and is a widely used method worldwide.
2.3 Principles of diffusion bonding
The diffusion bonding process can be roughly divided into the four steps shown in the schematic diagram in Fig. 2(1), (2)
. In Step 1, the materials to be bonded are stacked in air, and there are minute irregularities and air at the bonding interface. In Step 2, the materials to be bonded are placed in the diffusion bonding equipment and the atmosphere inside the furnace is evacuated to remove air from the bonding interface and prevent oxidation and the formation of voids (microscopic unbonded areas) in the bonded product. By starting pressurization and heating while evacuating the furnace, in Step 3, adherence (contact) progresses due to plastic deformation of the fine irregularities at the bonding interface, and bonding (adhesion) proceeds as the contact area increases. Subsequently, in Step 4, volume diffusion (intergranular diffusion) at the bonding interface progresses, and the bonding is completed when the bonded area finally integrates with the base material due to interface migration and the disappearance of voids.
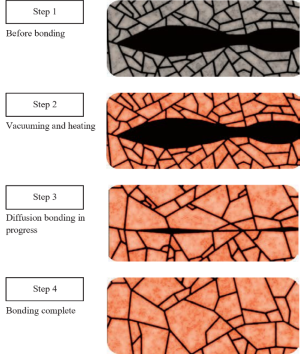
2.4 Features of diffusion bonding
Diffusion bonding has the following four features.
- High strength: Diffusion bonding can be expected to provide high strength because it is a surface-to-surface process that ultimately integrates the bonded area with the base material.
- High cleanliness: Diffusion bonding does not use any brazing materials or adhesives, and the bonded product usually includes no materials other than the base material, making it difficult for foreign matter to contaminate the bonded product and enabling extremely clean bonds.
- Low deformability: Diffusion bonding allows joining at a temperature below the melting point and minimizes thermal deformation of the bonded materials, resulting in high dimensional accuracy.
- Applicability to dissimilar material bonding: Diffusion bonding can be used to bond various dissimilar materials such as between dissimilar metals or between metals and ceramics with relative ease.
2.5 Key points of diffusion bonding
In general, to obtain sufficient strength by diffusion bonding, it is necessary to increase the contact area between the base materials to promote the diffusion of atoms. Table 1 summarizes typical bonding parameters for diffusion bonding. Since these parameters are interrelated, repeated bonding tests are necessary to find the optimal bonding conditions, depending on the desired bonding strength, deformation tolerance, and material type. Efforts are being made to obtain these conditions in various places.
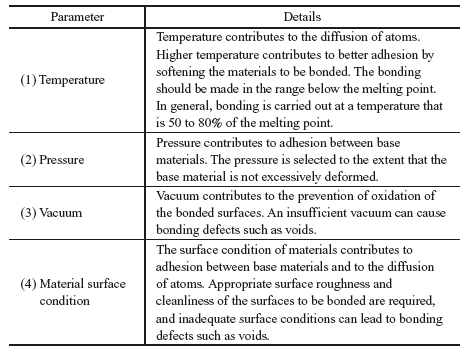
In light of the above, diffusion bonding equipment that can appropriately control temperature, pressure, and vacuum is required. IMS has developed and offers vacuum hot presses that meet these requirements. Details are described in Chapter 3.
2.6 Practical examples of diffusion bonding(3)–(6)
By taking advantage of the features described above, it is possible to bond components with microscopic shapes, and to manufacture products with complex internal channels by stacking many thin plates with grooves cut into them. In recent years, the range of applications for diffusion bonding has expanded, as shown in Figs. 3 to 5. Examples of industrial applications include hydrogen stations, compact and high-performance microchannel heat exchangers and reactors for offshore plants, and components for semiconductor manufacturing equipment that require high cleanliness. Examples of consumer applications include diffusion bonded copper and aluminum alloy cooling plates for electronic components and 5G/IoT-related components, and heat dissipation devices using dissimilar materials such as ceramics and copper. In addition, there are an increasing number of cases where diffusion bonding is being used to replace existing methods (brazing, 3D additive manufacturing, etc.) because it enables shapes that cannot be achieved with existing methods or simplifies the production process.
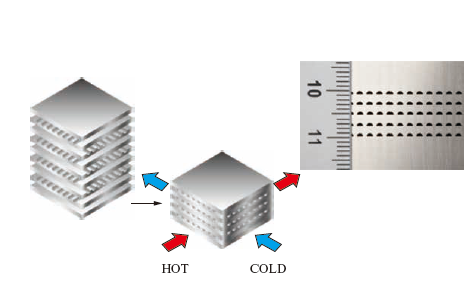
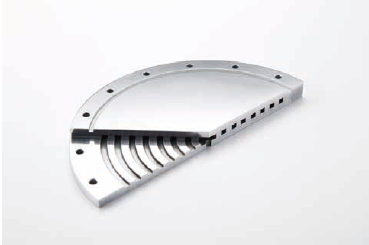
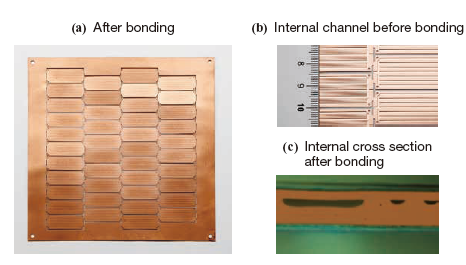
3. Diffusion bonding equipment (vacuum hot press)
3.1 Overview
Since 1984, IMS has been manufacturing vacuum hot presses that form products by applying pressure to articles to be processed under high temperatures and high vacuum. Diffusion bonding is performed using this vacuum hot press. The vacuum furnace has a heating chamber consisting of a heater and heat insulator inside a vacuum vessel made of steel, and a vacuum pump is used to create a vacuum inside the furnace vessel to raise the temperature to over 1 000°C to perform heat treatment of steel materials such as quenching and tempering. The vacuum hot press is a vacuum furnace with a press mechanism, and has the structure shown in Fig. 6. The main parameters listed in Table 1 are controlled in the IMS vacuum hot press as shown in Table 2.
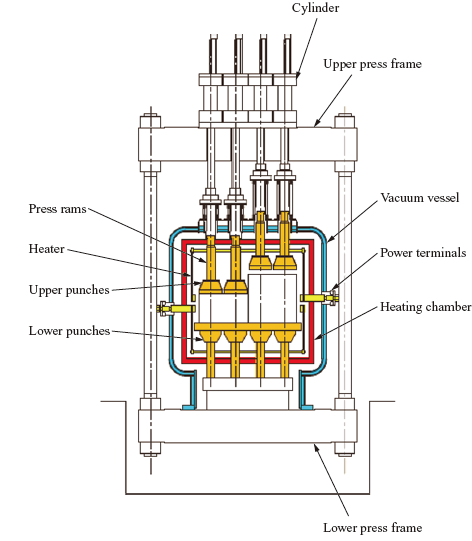
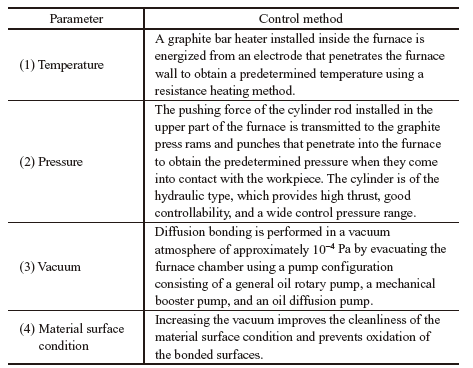
Since the temperature inside the equipment exceeds 1 000°C, heat insulator is used for the members in the heating chamber, and graphite material, whose strength does not deteriorate even at high temperatures, is mainly used for the heaters and other components. In addition, the press rams and punches, which require rigidity, are made of a special graphite material with high strength. For cooling, inert gas is introduced into the furnace and convection flow is provided by a fan for rapid cooling to improve production efficiency.
There are several options to satisfy the main parameters of diffusion bonding, such as temperature increase by induction heating or current heating, pressurization by spring force, and prevention of oxidation by bonding in an inert gas atmosphere. However, from the viewpoint of productivity, resistance heating vacuum hot pressing is industrially used as a typical diffusion bonding method, and IMS also uses it as a standard specification.
3.2 Single-axis and multi-axis type vacuum hot presses
IMS has been developing and improving vacuum hot presses specialized for diffusion bonding to meet customer requirements for larger sizes, higher surface pressures, and higher productivity. Figure 7 shows outside views of a typical single-axis type vacuum hot press (hereinafter referred to “single-axis type”) and a multi-axis type vacuum hot press (hereinafter referred to “multi-axis type”).
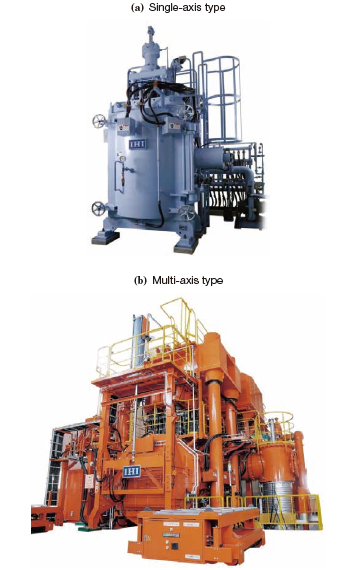
The single-axis type is a standard equipment with a single press axis, and the IMS Kakamigahara Works (Gifu Prefecture) has a test equipment at its Heat Treatment Technical Center for in-house research and sample tests from various customers. The main specifications of the test equipment are as follows: maximum pushing force 1 000 kN, maximum temperature 1 350°C, maximum mass of the bonded product 600 kg, and a work zone of 500 mm long × 500 mm wide × 500 mm high for one axis.
The multi-axis type has multiple press mechanisms in a single equipment, and either synchronous control, in which multiple axes are controlled synchronously, or individual control for each single axis can be selected. Synchronous control enables processing of large products over 1 m in length, while individual control of each single axis enables simultaneous mass processing of products of different sizes. The multi-axis type, intended for mass production, is in high demand by customers, and IMS has manufactured 2-, 4-, 6-, 8-, 9-, 10-, 12-, 16-, and 24-axis models. Although the size of the equipment itself becomes larger as the number of axes increases, the heater, vacuum pump, and cooling system can be enhanced to achieve the same heating, pumping, and cooling rates as the single-axis type. This design concept facilitates the improvement of mass production when shifting from a single-axis type to a multi-axis type. In cases where even higher productivity is required, the furnace body is constructed to withstand high pressure and is equipped with pressurized heating and pressurized cooling functions to improve the cycle performance. In another case, a continuous furnace type equipment is installed to enable continuous processing.
3.3 Ensuring heat and pressure uniformity
In particular, diffusion bonding requires uniform heating and uniform pressurization of the workpiece to improve its productivity. IMS vacuum hot presses mainly employ a resistance heating method to ensure good heat uniformity by heating the entire heating chamber.
Figure 8 shows the results of temperature distribution measured by placing dummy workpieces in a multi-axis type vacuum hot press as shown in Fig. 9 and inserting thermocouples approximately 10 mm inside the dummy workpieces. The workpieces were heated uniformly, and a temperature distribution within a range of 3°C was obtained.
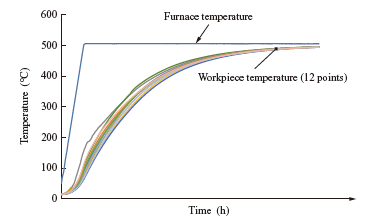
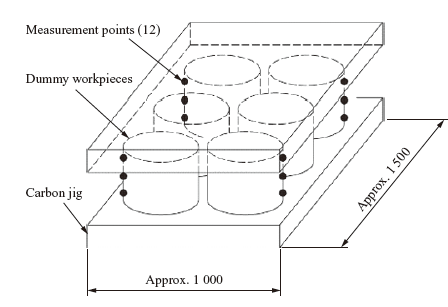
The press ram is designed to be rigid enough to ensure that the pressing force of the hydraulic cylinder installed in the upper part of the equipment propagates uniformly to the bonded surfaces. Furthermore, for workpieces with large area, multiple axes and IMS’s uniquely designed press system(7) are used to ensure uniform pressure. Figure 10 shows the surface pressure distribution on the workpiece as measured by pressure-sensitive paper. The pressure-sensitive paper was uniformly colored, confirming excellent pressure uniformity.
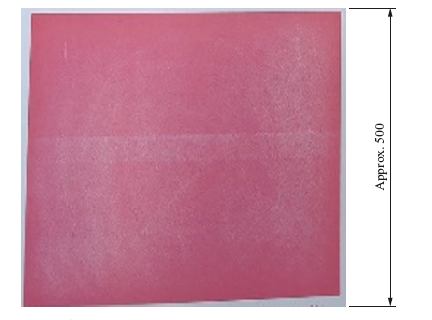
Thus, by continuing to develop technologies that improve productivity while guaranteeing heat and pressure uniformity, equipment with superior energy-saving performance can be developed.
4. Development of bonding process
4.1 Evaluation of bonding quality
As mentioned in Section 2.5, temperature, pressure, vacuum, and material surface conditions are the main parameters that determine bonding quality in diffusion bonding. In addition to these parameters, the bonding time must also be considered and controlled to satisfy the bonding quality and production volume required by customers. Therefore, the effects of bonding parameters on bonding quality were investigated using a vacuum hot press test equipment. Bonding quality was evaluated by three ways: cross-sectional microstructure observation to directly observe the presence of voids in the bonded area; tensile testing to evaluate static tensile strength, which is closely related to bonding quality; and ultrasonic testing, a non-destructive testing method.
4.2 Diffusion bonding between stainless steels
The following is an example of an evaluation of bonding stainless steel (SUS304) with different bonding pressures.
Figure 11 shows a photograph of the cross-sectional microstructure. Figure 11-(b) shows that the voids at the bonded surfaces observed under the low surface pressure condition shown in -(a) disappeared when the surface pressure was increased. Therefore, the tensile strength of the diffusion bonded SUS304 shown in Fig. 11-(b) was evaluated. As a result, as shown in Fig. 12, it was confirmed that the bonding strength was equivalent to that of the base material.
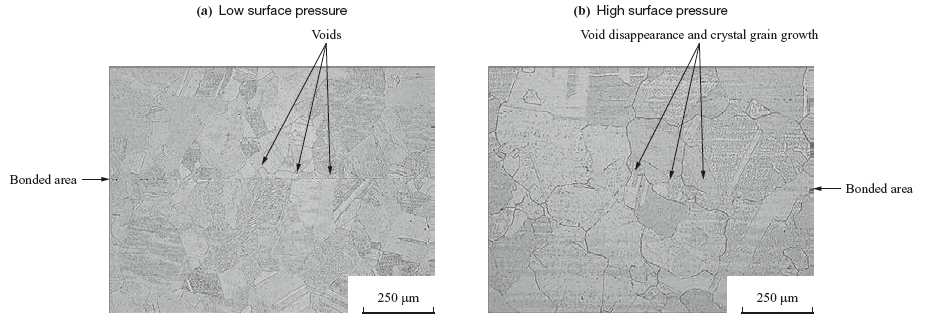
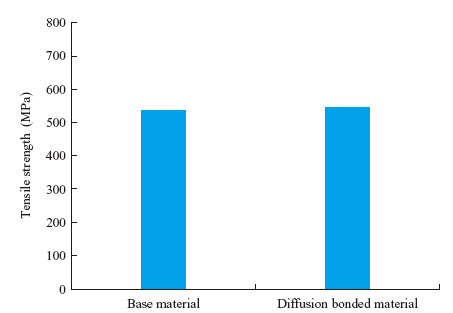
Figure 13 shows the results of ultrasonic testing of a diffusion bonded area. The normalized intensity of the reflected echoes from the bonded surfaces is shown in the contour map. Smaller reflection echoes (closer to white) indicate smaller voids and better bonding quality. Reflected echoes on the bonded surfaces observed under low surface pressure conditions disappeared under high surface pressure conditions, and bonding quality was improved. The results were consistent with cross-sectional microstructure observation and tensile strength evaluation.
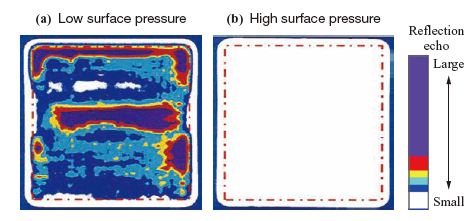
4.3 Diffusion bonding between oxygen-free copper and aluminum alloys
The following is an example of an evaluation of bonding oxygen-free copper (C1020) and aluminum alloy (A6061) at different bonding times. In this dissimilar material bonding process, brittle intermetallic compounds are formed at the bonding interface, making it difficult to create a sound bonded product(8).
The effect of heating time on the thickness of the intermetallic compounds that grow at the bonding interface was evaluated while searching for bonding conditions that can suppress the growth of intermetallic compounds and confirming the bonding properties. Figure 14 shows photographs of the cross-sectional microstructure of the bonding interface after long and short heating times. These photographs show that the layer between the A6061 and C1020 materials is an intermetallic compound and that the thickness of the intermetallic compound layer can be adjusted by adjusting the heating time.
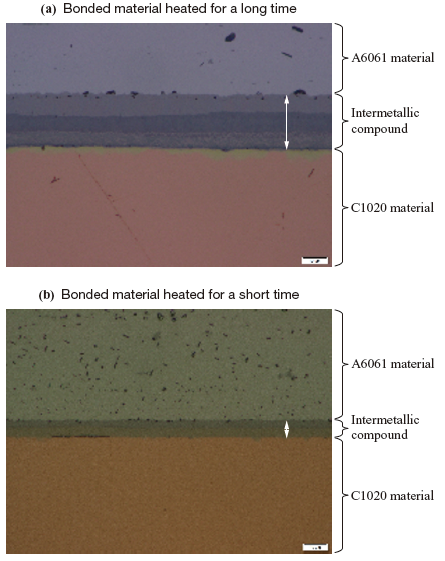
Tensile tests were performed on the bonded materials heated for long and short times. The bonded material heated for a long time failed at the joint interface during processing of the bonded material for tensile testing, so the bonding strength was low and could not be evaluated. On the other hand, tensile tests were able to be successfully performed on the bonded material heated for a short time, and as shown in Fig. 15, a tensile strength equivalent to that of the base material of A6061 material was obtained. This is thought to be because the fracture probability was suppressed by controlling the thickness of the brittle intermetallic compound with heating time, thereby ensuring strength equivalent to that of the base material.
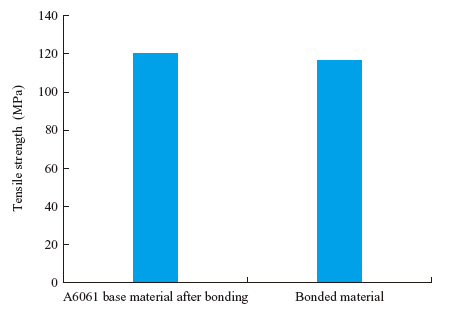
5. Future efforts
5.1 Process and product development
The results of the validation of each bonding process were presented in the similar and dissimilar materials. As shown in Fig. 16, bonding validation tests are underway for a wide range of material combinations. Recent trends in diffusion bonding technology require extremely high-precision bonding in applications such as jigs for manufacturing electronic components, electrical and electronic components, and ultra-precision filters. In addition to metal-to-metal bonding, demand for bonding new materials such as ceramics and metals is also increasing. In order to meet these requirements, in addition to the optimization of the bonding process, improvements in equipment are also necessary, and there is still much room for technological development. IMS aims to continue to expand the market by taking advantage of its ability to propose not only hardware, such as equipment, but also software, such as processes.
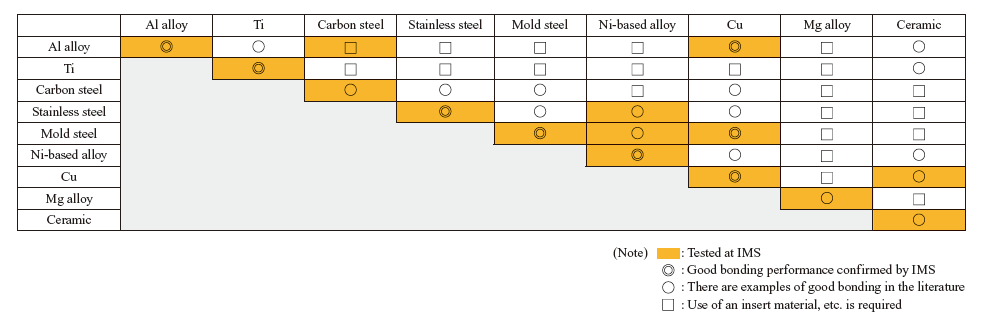
5.2 Process development support
IMS has mainly been engaged in the design and manufacture of bonding equipment. As diffusion bonding technology has spread, demand has increased in a wide range of fields, not only the equipment but also the bonding process. In response to this, IMS has started a diffusion bonding test service as shown in Fig. 17, in order to respond to customer requests for the best bonding method. Based on its accumulated know-how, IMS provides services for each customer development stage, from trial testing to Research and Development (R&D), business studies, and mass production launch.
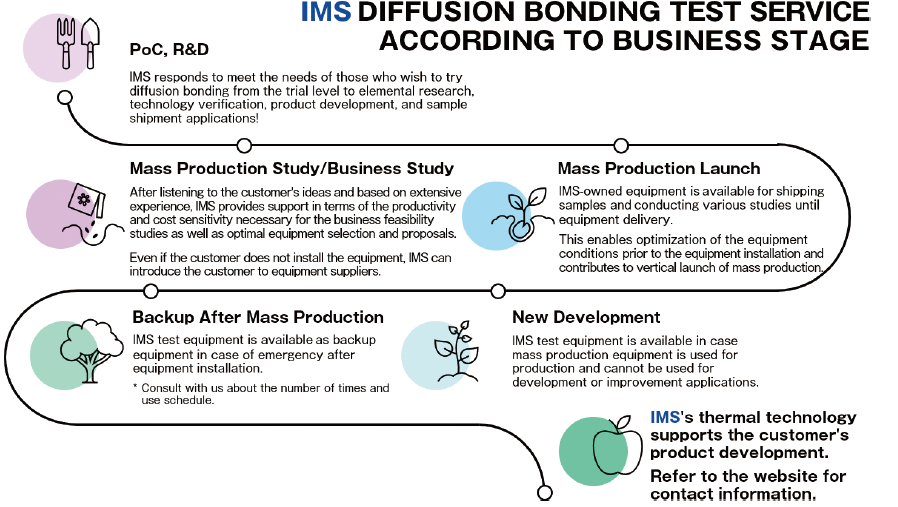
6. Conclusion
This paper introduced diffusion bonding technology, the outline of vacuum hot press, which is a diffusion bonding equipment, and efforts to develop the bonding process. Even though diffusion bonding technology has been receiving more attention recently, there are still many potential needs and innovative applications. As an equipment manufacturer, IMS is taking advantage of its information network to develop applications from the standpoints of both equipment and process development, with the aim of expanding the diffusion bonding-related industry as a whole.
REFERENCES
- O. Ohashi and T. Hashimoto : Study on Diffusion Welding (Report 2), – Effects of Welding Temperature, Time and Pressure on Welding Process –, Journal of the Japan Welding Society, Vol. 45, No. 4, 1976, pp. 295-301 (in Japanese)
- O. Ohashi and T. Hashimoto : Study on Diffusion Welding (Report 3), – Effects of Surface Roughness on Welding Process –, Journal of the Japan Welding Society, Vol. 45, No. 6, 1976, pp. 485-491 (in Japanese)
- O. Ohashi : Diffusion Welding 1, – Trend and Application of Diffusion Welding –, Materia Japan, Vol. 57, No. 9, 2018, pp. 443-447 (in Japanese)
- IHI Corporation : A Low-Carbon Smart Society Realized by Locally Distributed Production for On-Demand Use, IHI Engineering Review, Vol. 53, No. 1, 2020
- Y. Miwa, M. Azuma and K. Noishiki : Expanding Application of Micro Channel Equipment (Diffusion Bonded Compact Heat Exchanger; DCHE™), KOBELCO TECHNOLOGY REVIEW, No. 39, 2021, pp. 13-19
- A. Sasaki : Three-Dimensional (3D) Products by Photoetching +diffusion bonding, Die and Mould Technology, Vol. 37, No. 3, 2022, pp. 26-29 (in Japanese)
- IHI Corporation, IHI Machinery and Furnace Co., Ltd. : HOT-PRESS DEVICE, U.S. Patent 20200215781, 2020-07-09
- O. Ohashi and T. Hashimoto : Study on Diffusion Welding (Report 4), – Diffusion Welding of Copper to Aluminum –, Journal of the Japan Welding Society, Vol. 45, No. 7, 1976, pp. 590-597 (in Japanese)