SIS plus burner / injector
The SIS plus burner / injector, a highly efficient the combination of burner and injector technology developed by SMS Group, has the following characteristics:
-
Burner mode
- The SIS plus burner forms a long flame from combustion of natural gas (CH4) and oxygen, to efficiently pre-heat and melt the steel scrap. Furthermore, it reduces electrode consumption by avoiding breakage in the scrap column.
-
Injector mode
- The SIS plus injector features a specially shaped Laval nozzle for oxygen, as well as a ring gap for combustion of gas (natural gas and compressed air) which envelopes the ejected oxygen jet. The ultrasonic oxygen jet, enveloped by ejecting combustion gas, ensures an excellent straightness, so that the oxygen jet is up to 40 percent longer.
- The SIS plus injector uses compressed air for combustion of natural gas, to generate an enveloping gas. This reduces the consumption of high-pressure oxygen and therefore operational cost.
- When compared to conventional systems, the oxygen jet penetrates the slag layer with increased force. Consequently, the heat decarburizes rapidly and forms slag faster.
- Shorter power-on time leads to shorter tap-to-tap time and lower consumption of oxygen, natural gas, compressed air, and electricity.
The SIS plus burner/injector is registered as “Advanced facilities / systems” under the Japanese Advanced Energy-Saving Investment Promotion Support Project (2022)”
CONDOOR® - Automatic slag door
-
Outline
CONDOOR® is an automatic slag door for automated cleaning of the EAF sill-breast area and can be installed on new and existing EAFs.
Pushing of scrap remaining in the door sill and de-slagging can be done safely by the automated door, installed in the EAF slag door area. Automatic operation of CONDOOR® enables optimization of the door opening/closing time and a reduction of the power off time.
Moreover, through combination with TS-Pro Sampler, it is possible to automate the entire operations in the slag door area, thus removing operators from the most dangerous operating area of the EAF.The slag door is a part of EAF, which has remained mostly unaltered for many decades, except for a few minor changes in dimensions and construction. Looking at the way EAF slag volume has gone up in the last few decades and the process time has been drastically reduced, it is surprising that the method of de-slagging has not gone through any major upgrade. One of the basic limitations of the classic slag door lies in its poor control of de-slagging, which still depends on the Operator’s skill and judgement. With little control over its shape, it is nearly impossible to know how much slag has been lost or retained at any point of time.
Nowadays, many automatic machines and equipment are found on the working platform close to the EAF, concentrating on the slag channel area. Sampler, oxygen lances, carbon injection, hot metal launder require the slag channel to keep a proper shape, as incorrect sill profiles may result in incorrect or unsuccessful operations, thus in an increased power off time.
CONDOOR® can push any jam on sill to the inside of the shell with a hydraulic force of 24 tons at 120 bar. Its water-cooled pusher not only cleans the opening, but actually sits on the door opening, sealing it completely. It can withstand mechanical erosion of slag and the radiation from the arc. The operator can choose the exact time of de-slagging, as the door can be opened in a few seconds. Forklift and/or operators do not need to be present in front of the slag door any longer. The control over slag is possible with the capability to control the door opening from 0 to 100% and back to 0% by the pusher, which is designed to withstand direct contact with steel and slag.
-
Achieving carbon neutrality (Reduction of electric power consumption)
Removal of adherent slag from the slag door area ⇒ Improvement of slag door sealing ⇒ Reduced ingress of air ⇒ Less heat loss for EAF off-gas ⇒ Lower electric power consumption
-
References:
Over 20 references worldwide
-
Benefits
-
CONDOOR® reduces:
By improved slag practice
- Current
- Electrode consumption
- Energy loss
- Electricity consumption
- FeO loss
- NOx
- Need of any other Oxygen lance
-
CONDOOR® improves:
- Arc utilization
- Electrical stability
- Life of water cooled parts
- Yield of metals injected carbon & lime
- De-slag regulation
- Interface with other automation
- Overall safety
-
CONDOOR® reduces:
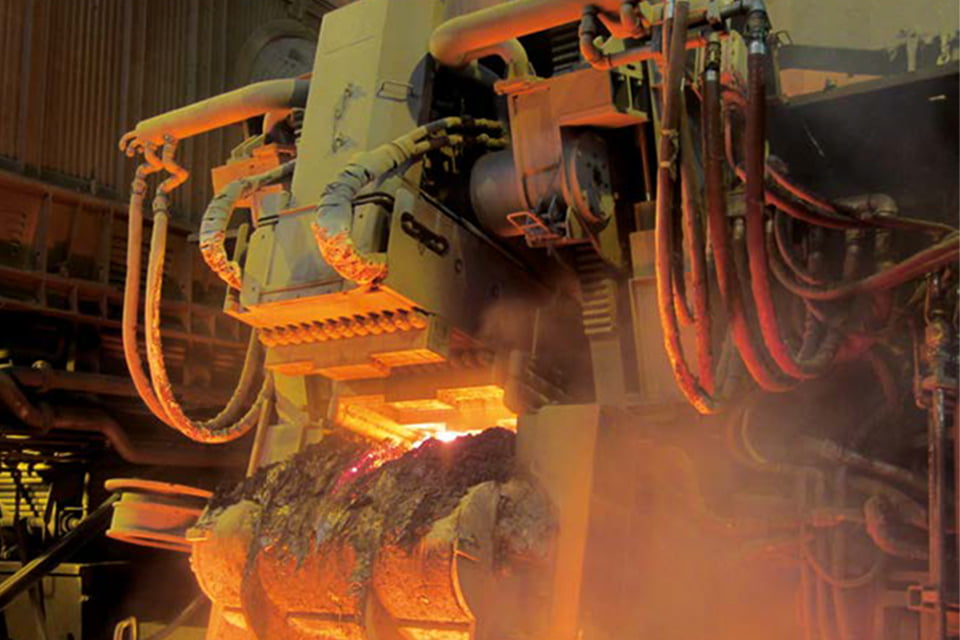
X-Pact® Sampler - Robotic sampling application
-
Outline
The X-Pact® Sampler, an anthropomorphic robot with six-axes, performs automatic sampling and temperature measurement of the heat. It is specially designed for the rough conditions around the EAF. Unlike mechanical samplers, TS-Pro Sampler can achieve full automation, ranging from measuring the temperature at various points, determining the classification of sparks to automatic cartridge exchange.
-
Achieving carbon neutrality (Reduction of electric power consumption)
Reduction of measuring time ⇒ Shorter slag door opening time ⇒ Reduced ingress of air ⇒ Less heat loss for EAF off-gas ⇒ Lower electric power consumption
-
References:
Over 20 references worldwide
-
Benefits
- Full automatic operation in EAF and LF
- No operators on the floor
- Automatic temperature taking and sampling operation
- Fit to different probes and cartridges available on the market
- 360º refractories view inside the Electric Arc Furnace
- Consistent and repeatable operations to stabilize the overall process time
- Steel bath level detection
- Automatic handling of probes exchange operation
X-Pact® AURA - Advanced Unit Rectifier Assembly
-
Outline
The X-Pact® AURA System, power digital controller for DC EAFs, was developed by SMS Group to lower the electric power consumption based on IGBT technology. With the AURA System, higher power factor and higher productivity can be achieved at the same time.
- Thanks to a multi-winding transformer and diode uncontrolled rectifier, outflow of harmonics to the electrical network can be suppressed.
- The power factor of the EAF on the electrical network side is always above 0.95 in the full power range.
- With the chopper technology, there is no need of post treatment of line disturbances to the electrical network anymore, e.g. EAF electrical design + SVC; disturbances are cleared at the source.
- The AURA System can effectively buffer and smooth the power grid side, isolate the impact and non-linearity of EAF power consumption and effectively reduce the flicker on the power grid side without the reactor on it.
- The AURA System combines the characteristics of a power supply device, high current conductor and arc controller, which can maintain the constant current or power of the arc.
- By adjusting the output voltage of the power supply device, it can produce a very fast arc current control and keep the arc steady, allowing improvements in energy and electrode consumption.
- An output reactor is integrated in each modular unit and can be directly connected to the electrode, therefore no extra-large DC reactor is needed.
- Built-in redundancy, thanks to a modular design
- Highly modular transformer configuration
- Furnace type transformer NOT necessary
- Transformer on-load tap charger NOT necessary
- Spare transformer NOT necessary
- Large reactor to control flicker or arc stability NOT necessary
-
Achieving carbon neutrality (Reduction of electric power consumption)
Less IGBT power loss than SCR ⇒ Lower electric power consumption
-
References:
The AURA system has been included on all recent SMS DC EAFs projects. Manufacturing of 8 units is currently underway.
-
Benefits
- Always higher power factor than conventional AC and DC solutions (≥ 0.95)
- SVC compensation system NOT necessary (Grid power has to be verified)
- Medium voltage switchgear breaker NOT necessary
- Reduced maintenance
- Minimized energy losses
- Minimized electrode consumption
- TCO (Total Cost of Ownership) 10 years, reduced by 30% compared to conventional AC operation
- A reduced requirement of short circuit capacity at PCC is ensured.
- The rectifier transformer does not need any on-load voltage tap charger, it is under lower harmonic stress and has a low harmonic coefficient. The transformer capacity can be reduced by approx. 20%, compared to a conventional AC EAF.
X-Pact® SynReg – Advanced Electrode Regulator
-
Outline
X-Pact® SynReg, a system to control raising/lowering electrodes, is designed to contribute to production cost reduction through its optimum control of electrodes. Superior melting can be achieved, whatever the charge material is.
- Easy integration into any existing automation system
- Available for AC or DC electric arc furnaces
- Equally suitable for electric arc or ladle furnaces
- Featured with dynamic compensation if primary voltage changes, full spectrum harmonic analysis, short circuit detection, and power demand control
SMS group Advanced Electrode Regulator system, SynReg, ensures that the electrodes deliver the required melt performance. Fully configurable and incorporating an extensive historical database, SynReg delivers consistent and optimal melting. It controls the electrode performance in the arc furnace, for all charge materials (scrap, DRI, HBI, hot metal) and targeted steel qualities. SynReg ensures consistent, repeatable day by day performance.
[Spec]
- Trend sampling rate: 50 ms
- Operating system: Windows 10, PLC: Siemens (Fuji Electric), Rockwell, Beckhoff, remote assistance, stand-alone or integrated with external control systems (selectable)
- Slag control and detection system (EAF only)
- Cycle time: < 3 ms
- Parameters: 100 sets
-
Achieving carbon neutrality (reduction of electric power consumption)
Improvement of power input efficiency ⇒ Shorter tap-to-tap time ⇒ Lower power consumption
-
References:
Over 100 references worldwide
-
Benefits
SynReg can achieve highly efficient conversion of input power to melting energy, through electrodes regulation on the case-by-case basis. As a result, the following benefits can be achieved.
- Reduction of energy consumption - less power on time
- Reduced electrode consumption, due to smart and steady regulation
- Lower maintenance costs, due to efficient and self-explaining troubleshooting tools
- Electrodes balance / unbalance
- Electrode anti-breakage