Green Steelmaking Technologies
- Aiming to realize hydrogen-based direct reduction iron (DRI) production plants based on process knowledge of Paul Wurth S.A. and insights gained through collaboration with its partners over the years
- Planning, study and optimization for green steelmaking through a combination of highly-efficient hydrogen production plant and DRI production plant
- Green hydrogen production using green electricity in a highly efficient high-temperature electrolyzer as well as waste heat generated from industrial process. In 2019 Paul Wurth S.A. became a lead investor for Germany-based Sunfire GmbH, a global leader in developing and producing high-temperature electrolyzers (SOEC) and high-temperature fuel cells (SOFC).
- Offering concrete and specific proposals for realizing customers’ zero-carbon target by bundling the technological competences and strengths of both Paul Wurth S.A., focused on the primary phase of steelmaking, and SMS Group, specialized in the downstream part of the steelmaking process
Coke Oven Gas Injection Technologies
- Technology for stepwise reduction of CO2 emissions from conventional iron-making processes, with an aim to achieve ambitious environmental targets balanced with economic constraints.
- Injection of coke oven gas into blast furnace
- Via tuyeres (Operation of industrial blast furnaces with COG injection via tuyeres has already started)
- Via blast furnace shaft (To be commissioned in 2023) - Development of coke oven gas reforming technology based on the reforming and partial oxidation of the coke oven gas – Currently being validated in a pilot plant
- Developing the technology to transform blast furnace gas and coke oven gas into a hot synthetic gas (a mixture of carbon monoxide and hydrogen) by means of a modified hot blast stove based on dry reforming
- Developing the technology to efficiently use more and more hydrogen into the blast furnace / basic oxygen furnace process by using not only syngas but also biomass in replacement of fossil fuels
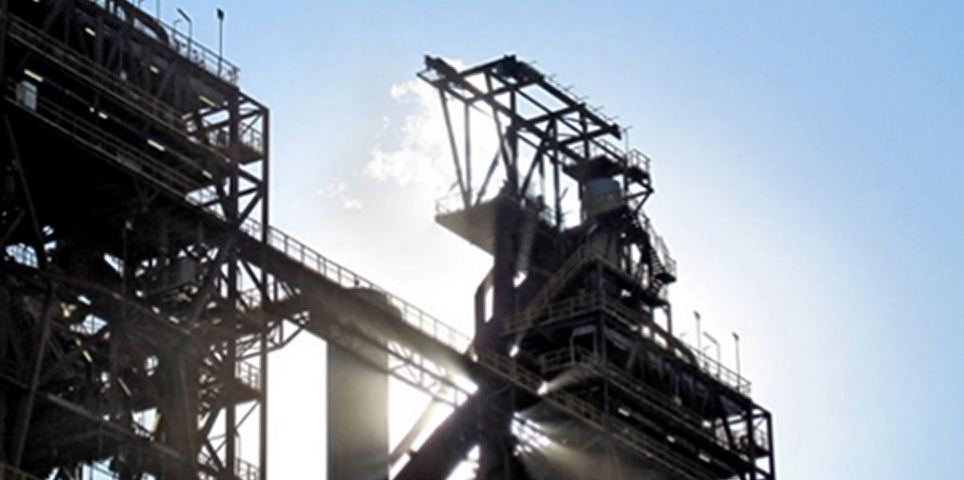
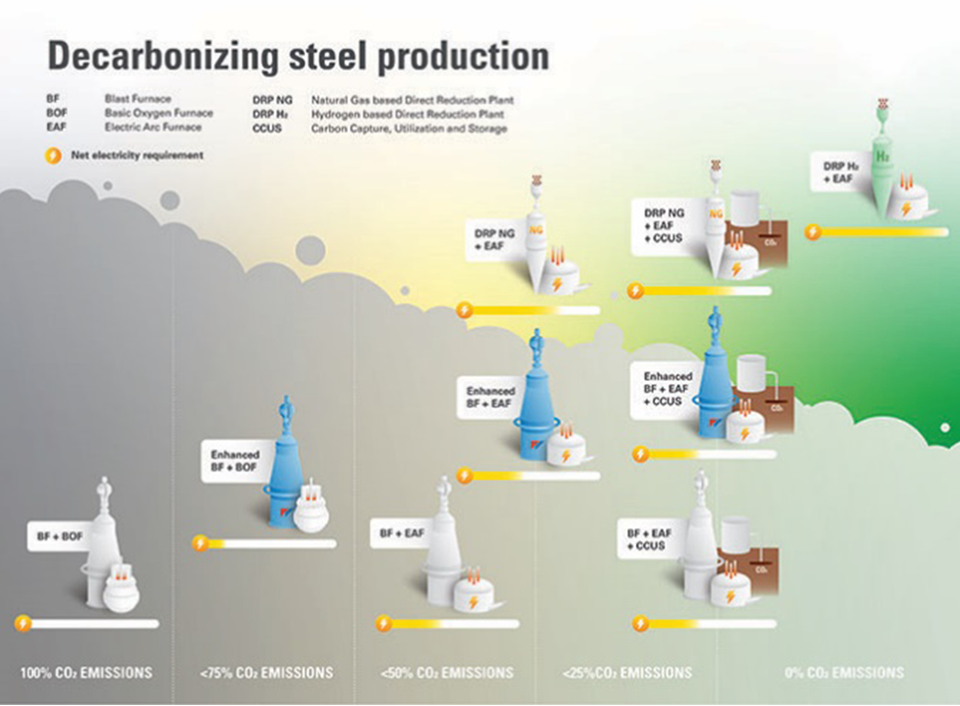
Electric Steelmaking Technologies
As replacement of blast furnaces, electric arc furnaces have been attracting more attention from steelmakers to become carbon neutral. Paul Wurth IHI Co., Ltd. can meet the needs for large-scale electric arc furnaces based on our extensive experience in the global market. Moreover, our electric arc furnaces with 100% direct reduction iron (DRI) charge have already been in operation.
Recently, submerged arc furnaces which can use auxiliary blast furnace plants and low grade DRI were added to our product portfolio. Our offering also includes a number of state-of-the-art equipment to contribute to reducing electric power consumption of the existing furnaces. We are pleased to introduce some of these equipment below.
IHI-based technology
Aluminum electrode arms and holders for reduction of electric power consumption
-
Compact design to reduce electric power consumption
- Weight of aluminum electrode arm - Half of the conventional steel arm
- Faster electrode ascending/descending speed
- Increased response resulting in lower reactance
-
Enhanced arc stability
- Faster vibration absorption to stable arc compared to steel arm
-
Low impedance
- Higher power factor
- Less circuit loss
- Increased effective power
-
Increased input power
- Shorter tap-to-tap time
- Less heat loss
- Lower electric power consumption
- Reduced electrode consumption
-
Longer campaign life thanks to our proprietary aluminum welding technology cultivated from IHI shipbuilding technology
- Over 28 years of continuous use
- No weld cracks
- No blowholes
- Lower maintenance cost
- Less maintenance workload
SMS-based technology
Achieving carbon neutrality for EAF operators
Reduction of electricity consumption is the most effective way to achieve carbon neutrality for EAF operators, the users of electricity for steelmaking. Paul Wurth IHI Co., Ltd. contributes to achieving zero carbon steelmaking of our customers through the state-of-the-art energy-efficient equipment of SMS Group (Germany).
GRITZKO® Valve for Pulverized Coal Injection
- Over 1500 references for 30 years of experiences in coal injection
- High resistance to abrasive material
- For global flow control on conveying line or individual flow control on distribution hopper or static splitter
- Best distribution accuracy through individual flow rate control
- Equal distribution onto all the Injection Lines by means of a coal flow rate measurement device, a coal flow rate control valve and a closed loop control installed in each Injection Line
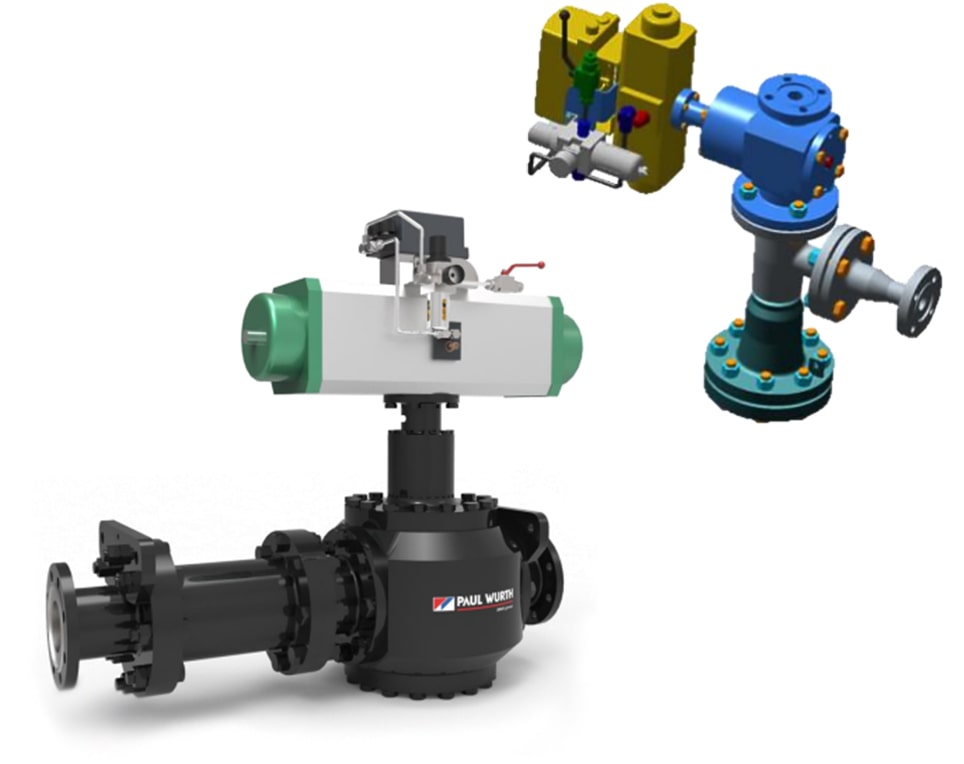
Top Combustion Hot Stove
- No circumferential ring walls in burner
- Proper refractory support
- Proper mixing and combustion already in the dome (no cooling of dome refractory)
- Easy up-scaling possible in vertical direction (more nozzles)
- Self-supporting conical dome
- Dome is highly self-supporting
- Bricks have no intention to tilt
Reference plant has shown excellent results in terms of:
- Stove performance
- Reliabilty/Availability
- No vibrations of burner and flame
- Good offgas values in regard to CO
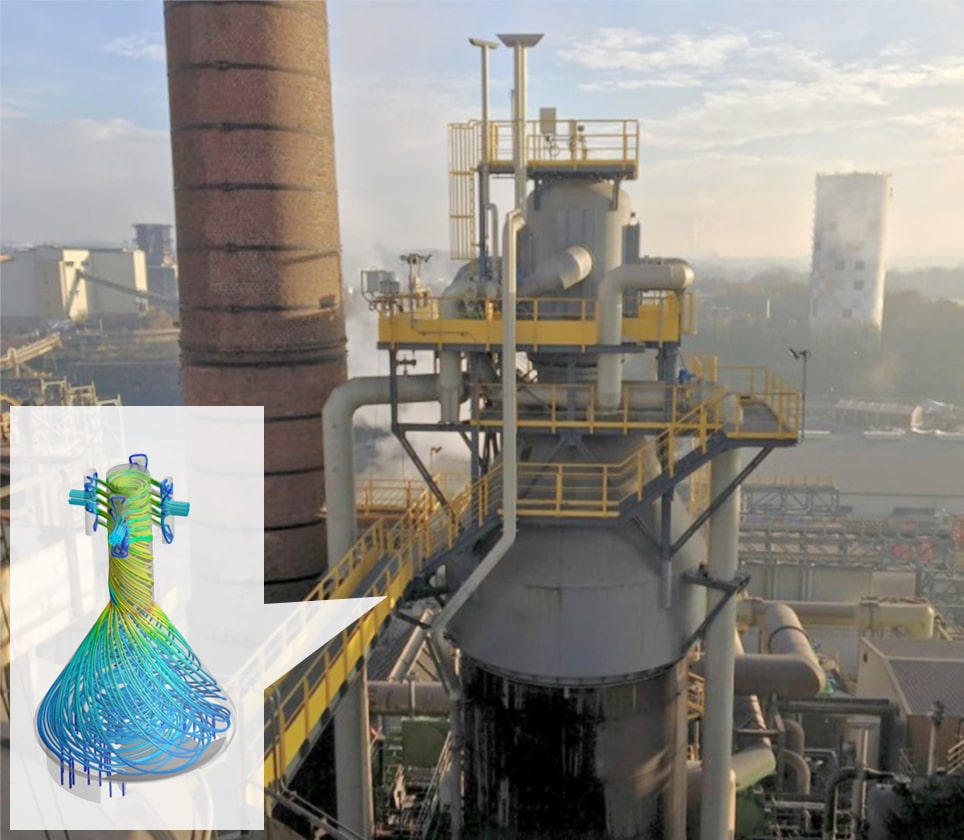
Cyclone Dust Catcher
- Axial Type Cyclone
- Proper refractory support
- Efficient dust separation: 80 - 90 %
- Increased recirculation of dust via sinter plant
- Separation of zinc and lead out of the system
- Decreased water consumption in wet stage
- Higher gas outlet temperature for TRT operation
- Less operational cost
- Less sludge to be deposit
- Fits ideally in existing plants for replacement by re-use of the existing supporting structure, foundation and downcomer
- Less space & cost required versus conventional dust catchers & tangential type cyclones
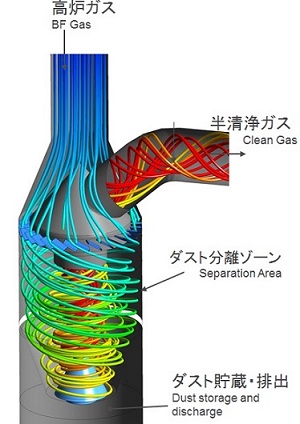
Generation 3 Bell Less Top®
- Closed loop pressurized cooling circuit
- Closed chute for higher rotation speeds & more accurate charging
- Extended greasing autonomy
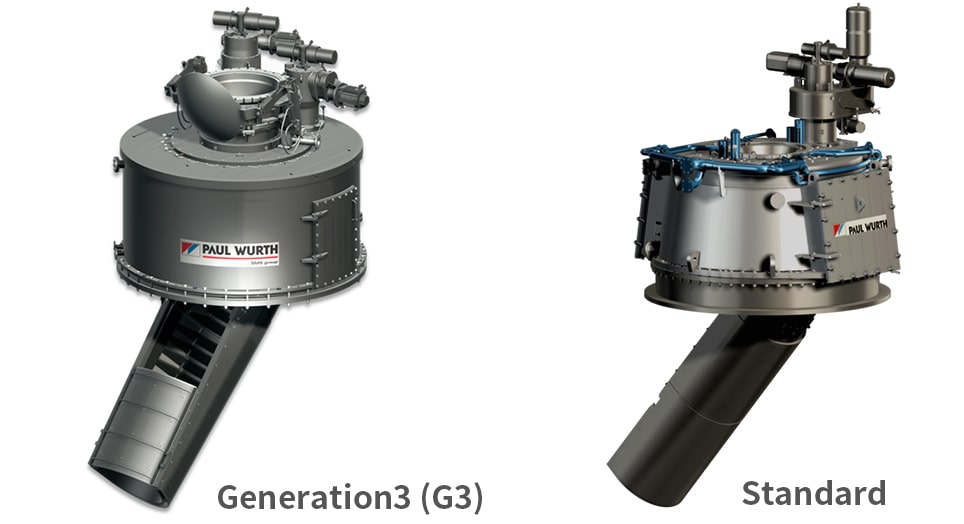
BF Xpert™
- Integrating the full range of proven BF process models & expert systems
- User-friendly due to tailor-made design (modular system concept)
- Open interface for full compatibility with existing software systems
- Savings in production costs achieved through increased process & energy efficiency, increased operational safety and extended equipment lifetime
SOPRECO® Single Oven Pressure Control System
- Able to regulate the pressure inside the ovens individually
- Avoiding gas leakage from the doors
- Preventing air suction into the ovens at the end of the distillation process & thus increasing coke quality
Energy Recovery System
- No leakage between both gases
- No moving parts
- Virtually maintenance free and easy to inspect
- High heat transfer efficiency and low pressure loss
- Suitable for a large range of heavy-industrial applications
-
BF1, CSC, Taiwan -
BF2, CS Tubarao, Brasil BF B, Hüttenwerke Krupp Mannesmann, Germany