Case studies
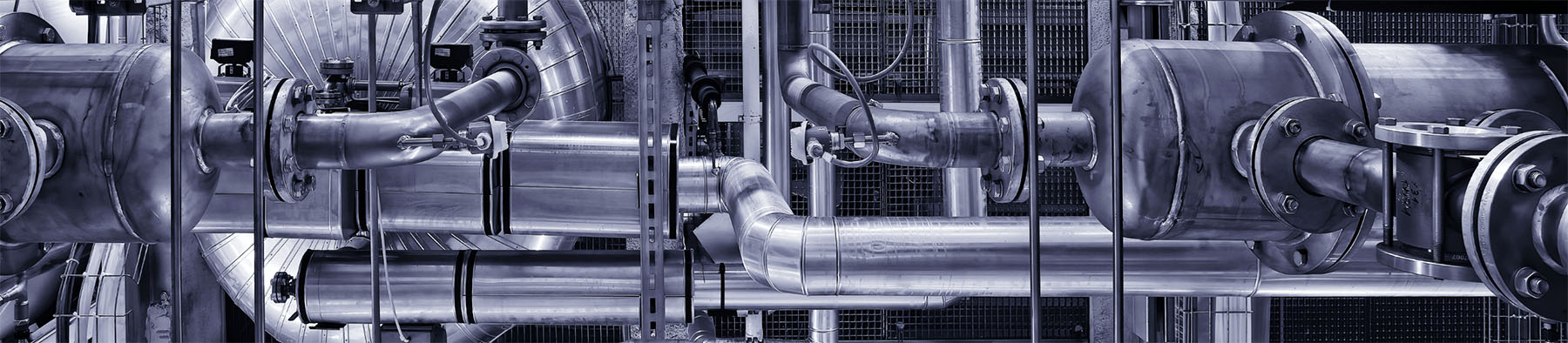
- TOP
- Case studies
- Kashima Plant, Asahi Tostem Exterior Building Materials Co., Ltd.
- Screw Decanter Centrifuge > HS-L Type
Kashima Plant, Asahi Tostem Exterior Building Materials Co., Ltd.
Application example of centrifuges: Treatment of highly abrasive slurry. Resulted in annual reduction of 30 million JPY in wastewater treatment costs.
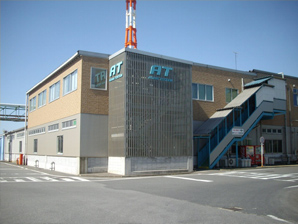
Asahi Tostem Exterior Building Materials Co., Ltd. is dedicated to elevating the value of homes with "Beautiful Walls." We visited their facilities to conduct an interview to learn more about the background leading up to the adoption of our centrifuge (HS-L Type) as part of their factory equipment and how the product has been integrated into their operations.
Company Overview
Kashima Plant, Asahi Tostem Exterior Building Materials Co., Ltd.
- Year of Establishment
December 1, 2004
- Products
1. Exterior building materials
2. Ancillary materials related to exterior building materials
3. Construction paints
4. Roofing materials
- Head Office
Emachu Kinshicho Bldg., 1-19-10 Mori, Koto-ku, Tokyo 135-0001
- Website
- Products
Ceramic siding
Ceramic siding commonly used as residential exterior material.
Asahi Tostem Exterior Building Materials is dedicated to the concept of providing "Beautiful Walls," and with this idea, they have released AT-WALL Guardenal, the top-of-the-line exterior wall material that offers protection against harsh conditions. With their "sealing-less" technology, which minimizes the visibility of joints between panels, they offer a lineup of products with enhanced visual aesthetic and durability. They strive to offer solutions to elevate the value of homes. For further details, please visit the link below.
http://www.asahitostem.co.jp/product/atwall/
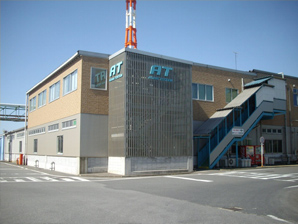
Company
overview
Established in 2004 after the merger of Tostem (currently LIXIL) and Asahi Glass's exterior building material division, Asahi Tostem Exterior Building Materials Co., Ltd. is a comprehensive manufacturer of exterior building materials.
With the accumulated trust and achievements from both companies, they assist in creating new homes, communities, and everyday living environments through "Beautiful Walls."
Background
- Q What were the issues behind considering the upgrade of a centrifuges? What were the problems and needs with existing equipment?
Our ceramic siding production line generates a substantial amount of wastewater. We have previously treated this wastewater through gravity thickening using a 170m3 storage tank, and natural dehydration with a 250m3 dehydration tank. However, this method resulted in low treatment capabilities that became a significant obstacle to increasing our production lines. Moreover, discharging the concentrated and dewatered sludge required the use of vacuum vehicles and great manual labor, resulting in increased treatment costs. Additionally, our company's reinforced environmental commitment made it an urgent necessity to reduce discharge weight by further improving the sludge dehydration rate.
To overcome these issues, we decided to consider the introduction of new equipment capable of dewatering the production line wastewater.
This is Mr. Nakamura, the one in charge. He's holding the liquid before separation in his left hand and the liquid after filtration in his right hand.
Determining Factors
- Q With the various challenges you were facing, could you please share the reasons for choosing our centrifuge? And what were the deciding factors in choosing our product?
We were in search of dehydration equipment that can be operated within limited, confined spaces, didn't require a lot of effort to maintain, and enabled continuous processing instead of batch processing. This led us to IHI's Screw Decanter Centrifuge.
We conducted lab-scale experiments and mid-scale testing using a demo unit, and IHI was instrumental in identifying a dehydration condition that exceeded our initial requirements in a swift and logical manner. The dedication and commitment of IHI's technical team was also a deciding factor.
Another aspect that influenced our decision-making was the fact that IHI's equipment was more superior in wear resistance compared to other manufacturers, which is crucial as we handle highly abrasive wastewater.
Outcome of Application
- Q Have your challenges been resolved after utilizing our centrifuge? How has the system been received within your company?
By improving our wastewater treatment capacity, we were able to improve the production line performance by approximately 5%.
Furthermore, the improvement in sludge dehydration capacity resulted in a 50% reduction in discharge weight, which we anticipate would lead to annual cost savings of 30 million JPY in treatment costs.
Actual Installation of HS-L Type Centrifuge
Future prospects
- Q Please share your future outlook and plans regarding filtration systems.
We are conducting experiments to optimize operational conditions based on the properties of wastewater that is treated using the centrifuge toward additional energy efficiency.
We are also considering to expand our centrifuge installations to further realize the creation of added value through "Beautiful Walls," which is the core concept of Asahi Tostem Exterior Building Material.
Our Procuct
![[製品写真]](https://images.microcms-assets.io/assets/cca16cef653746d78130436ed648fc63/edbb5ff7593e4d9a8a511dab82bbeec7/hs-l-topimage.jpg)
- Screw Decanter Centrifuge > HS-L Type
To date, we have produced over 15,000 centrifuges that have been applied in various fields.
The HS-L series is the most versatile of all IHI's screw decanter centrifuges. It is ideal for use in a variety of applications from wastewater treatment to manufacturing processes. The model adopted by Asahi Tostem Exterior Building Materials Co., Ltd. features super-hard chip applications for enhanced wear resistance.
(Posted on June 18, 2012)