Glossary
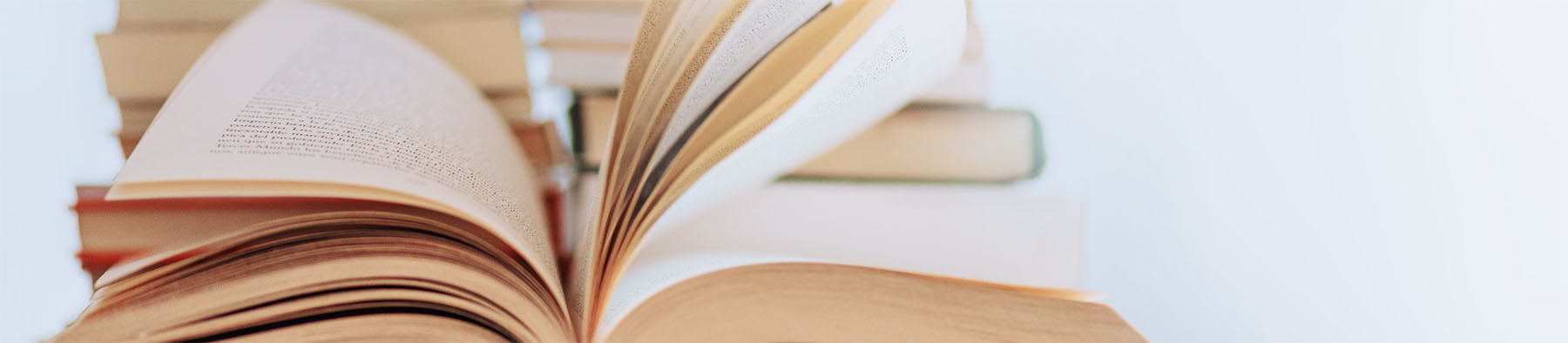
Raw Material
Material that is fed to Centrifuges or Filters for separation or filtration.
Mother Liquid = Solution of raw material
Related links:
Separators & Dehydrators, Filters
Slurry
A thick, watery mud or mixture of insoluble matter. In the field of Centrifuges & Filters Raw Material means Slurry.
Related links:
Separators & Dehydrators, Filters
Cake
Dewatered solid material after separation or filtration.
Related links:
Separators & Dehydrators, Filters
Scum
A solid matter that floats on the surface. Scum in human waste disposal is a dried solid matter on the surface containing methane gas, etc. that settles once in the digestion tank and then floats on the surface.
Related links:
Screw Decanter Centrifuge, PD Dehydrator, Belt Press Dehydrator
Sludge
Accumulated and concentrated solids. When you treat heavy oil, Sludge is generated by storage or heat treatment of furnace oil including residual oil.
Related links:
Screw Decanter Centrifuge
Flock
Collections of smaller particles agglomerated into larger, more easily settleable particles through polymer flocculation generally.
Related links:
Screw Decanter Centrifuge, PD Dehydrator, Belt Press Dehydrator
Emulsion
A heterogeneous liquid mixture of two or more liquids such as fat, fatty oil, and essential oil that are not typically dissolved in one another and emulsified.
Related links:
Separators & Dehydrators, Filters
SS (Suspended Solids)
Insoluble solids that float in liquid. Visible solids in Slurry.
Related links:
Separators & Dehydrators, Filters
DS (Dissolved Solids)
Solids dissolved in liquid.
Related links:
Separators & Dehydrators, Filters
TS (Total Solids)
The sum of Dissolved and Suspended Solid constituents in Slurry. Visible solids included. TS = SS + DS.
Related links:
Screw Decanter Centrifuge, PD Dehydrator, Belt Press Dehydrator
MLSS (Mixed Liquor Suspended Solids)
The concentration of suspended solids in activated sludge mixed liquor in an aeration tank. MLSS is used to measure the condition in an aeration tank during biological treatment, while SS concentration commonly measures disposal performances (load of solids) of a separator/filtrator.
Related links:
Screw Decanter Centrifuge, PD Dehydrator, Belt Press Dehydrator
VTS (Volatile Total Solids)
Total amount reduced after heat treatment. A volatilizing amount when the residue of evaporation is heat-treated, mainly the amount of organic matter. The smaller the figure is, the better the dehydration performance. When residue and volatile matter are separated after the residue is heat-treated at 600℃, VTS is measured.
Related links:
Screw Decanter Centrifuge, PD Dehydrator, Belt Press Dehydrator
Alkaline Rate
Alkaline rate of sludge. The higher the rate, the greater the progress of anaerobic digestion.
Related links:
Screw Decanter Centrifuge, PD Dehydrator, Belt Press Dehydrator
Fiber Content Rate (%)
The rate of fibers contained in sludge. The higher the rate, the better the dehydration performance. 100 mesh (the amount caught with a net of 100 mesh) is the Fiber Content Rate in the case of sewage sludge.
Related links:
Screw Decanter Centrifuge, PD Dehydrator, Belt Press Dehydrator
Particle Content Rate (%)
The rate of fibers/sand/etc. contained in sludge. The higher the rate, the better the dehydration performance.
Related links:
Screw Decanter Centrifuge, PD Dehydrator, Belt Press Dehydrator
CST (Capillary Suction Time)(sec)
CST measures for evaluation of filtration performance of sludge by measuring the time during which liquid spreads by the capillary phenomenon. The larger the figure, the larger the amount of viscous matter, therefore the worse the dehydration performance.
Related links:
Screw Decanter Centrifuge, PD Dehydrator, Belt Press Dehydrator
Colloid Level (meq/l)
The electric charge of colloidal matter contained in sludge. Cationic matter such as polymer flocculants are reacted and consumed with negatively electrically charged matter. Therefore Colloid Level has correlation with flocculant addition rate. Normally sludge is negatively charged.
Related links:
Screw Decanter Centrifuge, PD Dehydrator, Belt Press Dehydrator
SVI30 (Sludge Volume Index)
Sludge Volume Index. Sedimentation sludge volume (cm³) of dried sludge left untouched per gram. This expresses how much sludge sedimentation in an aeration tank is in progress. In the case of fine activated sludge the figure is less than 120. If the figure is over this level, bulking may be occurring because of growth of a filamentous fungus, etc.
Related links:
Screw Decanter Centrifuge, PD Dehydrator, Belt Press Dehydrator
Effects of Metal Chloride (PAC etc.) Addition
- 1.Neutralizing negative electric charge of viscous matter in sludge (contributes to dehydration).
- 2.Reducing or removing negative electric charge of matter in liquid (an amphoteric polymer flocculant is necessary).
Related links:
Screw Decanter Centrifuge, PD Dehydrator, Belt Press Dehydrator
Particle Classification
Classifying particles according to size.
Related links:
Screw Decanter Centrifuge, Guinard Centrifuge
Flocculant
A chemical generally used to flocculate minute particles in order to raise the separation/dehydration effect when treating sewage. There are inorganic flocculants and organic polymer flocculants.
Related links:
Screw Decanter Centrifuge, PD Dehydrator, Belt Press Dehydrator
Inorganic Flocculant
Though applicable to a wide range of raw materials, the strength of flocks produced is relatively weak and small. If you add an Inorganic Flocculant for dehydration, the amount of dewatered cake to be disposed of increases. Therefore there has been a tendency to use this as little as possible. When using an organic polymer flocculant only and it is incapable of forming flocks, adding Inorganic flocculant enables you to change the characteristics of the liquid and to form large flocks.
PAC (Polyaluminum Chloride), Ferric Chloride, Polyferric Sulfate and Slaked Lime are Inorganic Flocculants. Available normally as a 10~20% concentrated liquid.
Related links:
Screw Decanter Centrifuge, PD Dehydrator, Belt Press Dehydrator
Organic Polymer Flocculant
This is the most popular flocculant in the field of sewage treatment because the volume of Organic Polymer Flocculant that needs to be added is less than that of Inorganic Flocculant. As well, its stronger flocculating effect enables the formation of larger flocks.
It is classified into three groups according to the electric charges of the ions: Cationic, Anionic and Nonionic. Cationics have positive electric charge, Anionics negative and Nonionics have none. Cationics are generally effective for organic sewage and Anionics for inorganic. Nonionics are used where neither Cationics nor Anionics are effective.
Organic Polymer Flocculant used to be available as a powder, but the demand for a liquid flocculant as an emulsion (40%) has been rising because the powder is difficult to dissolve."
Related links:
Screw Decanter Centrifuge, PD Dehydrator, Belt Press Dehydrator
Flocculation
Separation/dehydration using flocculants. There are three flocculation methods. The Tank Mixture Method is to mix raw slurry and a flocculant in a mixture tank. The In-Line Flocculation Method is to add a flocculant into the slurry supply pipe. The Flocculant Feed Pipe Method is to add a flocculant into the decanter.
Related links:
Screw Decanter Centrifuge
Sewage, Night Soil (Human Waste), Agricultural and Fishery Wastewater
The raw materials are the same but the authorities concerned are different. Sewage: Ministry of Land, Infrastructure and Transport (Japan Sewage Works Agency). Night Soil (Human Waste): Ministry of Health, Labour and Welfare. Agricultural and Fishery Wastewater: Ministry of Agriculture, Forestry and Fisheries.
Related links:
Screw Decanter Centrifuge, PD Dehydrator, Belt Press Dehydrator
Primary Sedimentation Tank
The first settling tank used for the removal of a considerable amount of organic floating matter only by self-weight settling and natural rising. Oils and fats are removed as a scum.
Related links:
Screw Decanter Centrifuge, PD Dehydrator, Belt Press Dehydrator
Aeration
The main process of sewage purification. If you add air to sewage, aerobic bacteria grow and dissolve organic matter, and photosynthesis of new cells occurs.
Alternately, there is another way of oxidization of inorganic drainage. If you blow air into sewage containing ferrous hydroxide, it becomes ferric hydroxide oxide, which results in a better separation/dehydration performance.
There are two methods of aeration: underwater aeration and surface aeration.
Related links:
Screw Decanter Centrifuge, PD Dehydrator, Belt Press Dehydrator
Final Sedimentation Tank
As the aerobic microbes in an aeration tank or a trickling filter grow, they come off one after another and are washed away. The Final Sedimentation Tank is used for collecting them in order to use or dispose of them.
Related links:
Screw Decanter Centrifuge, PD Dehydrator, Belt Press Dehydrator
Final Filter Bed Method
If you trickle sewage or factory drainage (organic) over the filtration tank in which filter materials (crushed stone etc.) are stuffed, gelatinous membranes (biomembranes) on the filter materials make contact with the drainage. Then organic matters in the drainage is dissolved by aerobic bacteria in the biomembranes.
Related links:
Screw Decanter Centrifuge, PD Dehydrator, Belt Press Dehydrator
Anaerobic Digestion Method
In the process of sewage and human waste disposal, Anaerobic Digestion dissolves (digests) organic matter only by the behavior of enzymes secreted by anaerobic bacteria in the absence of oxygen.
There are two stages in the digestion process: liquefaction and gasification. In the liquefaction process, enzymes secreted by anaerobic bacteria hydrolyze organic matter, which changes into various acids (carbohydrate into simple sugars, protein into amino acid, fat into fatty acid). In the gasification process, fatty acids generated in the liquefaction process change into methane gas and carbonic acid gas. As a result of these two processes, organic matter changes into inorganic matter.
Related links:
Screw Decanter Centrifuge, PD Dehydrator, Belt Press Dehydrator
Aerobic Digestion Method
By blowing air into sewage or human waste and mixing them, you can reduce and dissolve organic matter using bacteria, oxygen or dissolved oxygen and then change them into various acids or inorganic matter.
Related links:
Screw Decanter Centrifuge, PD Dehydrator, Belt Press Dehydrator
Activated Sludge Method
This is a method for biological sludge purification that involves mixing sludge with aerobic bacteria and aerating the mixture. The sludge formed by this method has a strong flocculating effect and good settleability. Many sewage treatment plants and private factories adopt this method.
Related links:
Screw Decanter Centrifuge, PD Dehydrator, Belt Press Dehydrator
Excess Sludge
If you use the Activated Sludge Method, by aerating only, aerobic bacteria increase too much. Therefore you have to remove the sludge so that there is a suitable amount of bacteria. The sludge to be removed is called Excess Sludge.
Features of Excess Sludge
- 1.The diameter of the particles is relatively small.
- 2.The fiber content rate is lower than that of raw sludge because bacteria dissolve the fibers.
- 3.The rate of organic matter is high and the water that cannot be removed by mechanical methods is contained in the cells.
Features of Raw Sludge
- 1.The diameter and specific gravity of the particles are relatively large.
- 2.Sludge contains many Fibers and slimy matter.
- 3.The rate of organic matter is lower than that of Excess Sludge therefore Raw Sludge is easier to dehydrate
Related links:
Screw Decanter Centrifuge, PD Dehydrator, Belt Press Dehydrator
Coagulation Sedimentation Method
This is a method for forming flocks, coagulating and settling out by adding inorganic coagulants or organic polymer coagulants to the particles that are relatively large or have large specific gravity differences. The concentrated sludge that has settled out is "coagulated sludge".
This method is more effective to use for matter left unremoved after the preceding activated sludge treatment than for sludge itself. Because the coagulants to be added are smaller and the process is more efficient, the method is used together with the activated sludge method. In that case the sludge fed into a separator is a mixture of excess sludge and coagulated sludge.
Related links:
Screw Decanter Centrifuge, PD Dehydrator, Belt Press Dehydrator
Pressure Flotation Method
If you make froths absorbed to minute particles in sludge, the apparent specific gravities become smaller and you can separate thicker floater mixture liquid. Matter in which the specific gravity difference from water is relatively small or in which sedimentation separation is very slow are easy to separate and remove. Less space is required compared to gravity sedimentation.
Related links:
Screw Decanter Centrifuge, PD Dehydrator, Belt Press Dehydrator
Standard Nitrogen Removal Method
A standard treatment method that was most widely used. Also called the low dilution two-stage activated sludge treatment. After diluting raw materials by 5~10 times, they are treated using the activated sludge method and coagulation sedimentation method and then sludge is dehydrated.
Related links:
Screw Decanter Centrifuge, PD Dehydrator, Belt Press Dehydrator
High Load Nitrogen Removal Method
The developed version of the Standard Nitrogen Removal Method. Also called the non-dilution treatment. With the Standard Nitrogen Removal Method, raw materials are diluted by 5~10 times, but with the High Load Nitrogen Removal Method, dilution is not performed. In this method, activated sludge is forced to be concentrated mechanically while it has usually been concentrated by natural sedimentation. Using this method, the sludge concentration rate at the first stage can be 15,000~20,000 ppm and the machinery equipment can be smaller. (The sludge concentration rate at the first stage has usually been several thousand ppm.)
Related links:
Screw Decanter Centrifuge, PD Dehydrator, Belt Press Dehydrator
High Load Nitrogen Removal Method by Membrane Separation
The most popular recently-developed version of the High Load Nitrogen Removal Method. By using ultrafiltration (UF) membranes, there is no need for a coagulating sedimentation tank and other equipment accompanying it. Compared to the High Load Nitrogen Removal Method, the machinery equipment can be smaller. The decanter is used to remove impurities at the first stage for reducing the load and for protection of the membranes at the back.
Related links:
Screw Decanter Centrifuge
Sedimentation Separation Device (Thickener, Clarifier)
There are two type of Sedimentation Separation Devices: Thickener and Clarifier. The former is used for obtaining a thick slurry, and the latter for obtaining supernatant fluid. There are no essential differences between them as devices.
Related links:
Screw Decanter Centrifuge, PD Dehydrator
Filter Aid
Filter Aid is used for improving filtration performance or preventing clogging of filter materials. There are several Filter Aids such as diatomaceous earth (material: fossil of diatom), perlite (material: stone) and cellulose (material: pulp). Diatomaceous earth is the most popular.
Classification: Diatomaceous earth, perlite, activated carbon and cellulose
Popular brands: Radiolite, Topco, Shirasagi, KC Flock, Celite, Roka-help, Taiko, Abosel and etc.
Related links:
Leaf Filter, Fundabac Filter
Direct Filtration
A method for filtrating raw materials directly without using filter aids. Filtration is generally divided into two categories. One is to filtrate by forming filtration layers with solids of different particles. The other is to filtrate using the filter materials themselves. The former is called "Cake filtration" and the latter "Filter material filtration". Membrane filtration is the representative method of the latter.
Related links:
Leaf Filter, Fundabac Filter
Precoating
Forming layers of filter aids on filter materials before filtration. By Precoating, catching solids with a smaller particle diameter is possible, compared to catching using filter materials only. As well, because solids do not touch the filter materials directly, cakes come off more easily and the clogging progress can be delayed. The amount of filter aids used for Precoating is generally 1kg/m2.
Related links:
Leaf Filter, Fundabac Filter
Body Feeding
Feeding a certain amount of filter aids to raw materials. The purpose is to improve filtration performance of raw materials. It is effective when treating raw materials that have particles of minute diameter therefore the cake resistance is easily maximized (that means filtration is impossible). By Body Feeding, the resistance of particles becomes smaller, and the amount of filtration can increase and the filtration time can be longer. Body Feeding is sometimes used together with Precoating.
Related links:
Leaf Filter, Fundabac Filter
Decolorization
Removing colors from raw materials. When treating water-like materials, activated carbon is added, and after mixing them, colors are absorbed to the activated carbon. When treating oil-like materials, activated clay is used instead of activated carbon. The activated carbon and activated clay are filtrated by a filtrator.
Related links:
Leaf Filter, Fundabac Filter
Cake Washing
Washing the separated/filtrated solids with water or solvents so that no mother liquid is left. Cake Washing is done when you want to collect as much mother liquid as possible because it is used as a product, or when you do not want to discharge mother liquid outside the system because it is poisonous.
Related links:
Leaf Filter, Guinard Centrifuge