Engine System Technology
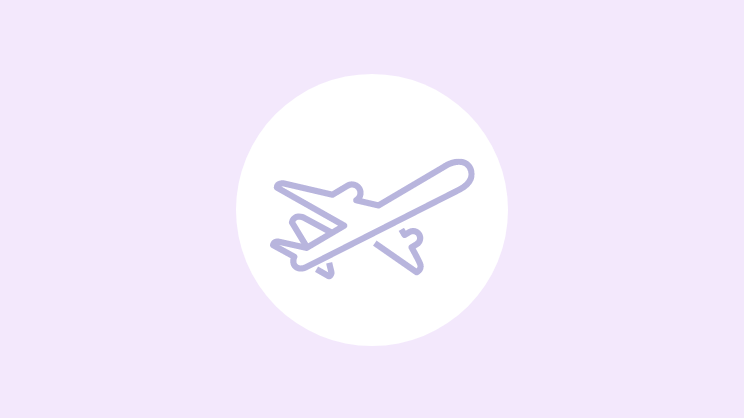
Engine System Technology
- FUJIMURA Tetsuji, OBA Yoshinori,IKEDA Shuji
The research and development of environmentally compatible engine for small aircraft (ECO engine project) was started in 2003. The objective of this project is to improve engine system integration capability and to establish the advanced technologies required for next generation small aircraft engines, which are environmentally friendly and economically viable. To satisfy these requirements, a large number of advanced component technologies has been developed and incorporated in the engine system design. The total number of stages has been reduced by half from current same class engines. This paper describes the outline of the engine system design, which satisfies the ECO engine project goal.