Ammonia Energy Value Chain for Carbon Neutrality from Production to Utilization
FUJIMORI Toshiro, SUDA Toshiyuki
FUJIMORI Toshiro : Doctor of Engineering, Technical advisor, Technology & Intelligence Integration
SUDA Toshiyuki : Doctor of Engineering, Manager, Strategic Project Department, Corporate Strategy Headquarters
Ammonia is attracting attention as a hydrogen energy carrier for reducing greenhouse gas emissions. Conversion of hydrogen into ammonia and liquefaction of ammonia allow hydrogen to be stored in a large quantity and to be transported to consumption areas from production areas with rich renewable energy resources. Furthermore, using ammonia as fuel for boiler turbine power generation and gas turbine power generation can promote the energy transition to carbon neutrality while utilizing existing infrastructure. The IHI Group has been providing important infrastructure technologies for energy value chains and proceeding with development of technologies and business opportunities to build an ammonia energy value chain.
1. Introduction
Ammonia is attracting attention because it is an efficient carrier for hydrogen energy and contributes to the reduction of carbon dioxide (CO2) emissions from thermal power generation(1). To achieve carbon neutrality, Japan needs to transport energy by ship from overseas because domestic renewable energy is insufficient to meet the demand for electricity and it is geographically isolated. Japan has positioned the fuel ammonia industry as an important business area where growth is expected due to carbon neutralization and plans to introduce 3 million tons ammonia as thermal power generation fuel in 2030 as an intermediate target and 30 million tons in 2050, which is equivalent to 10% of the amount of power generation(2).
Japan’s thermal power generation is one of the most efficient in the world, supplying 70% of domestic electricity. Even if renewable energy accounts for 50 to 60% of the total power generation in the future, thermal power generation is necessary for supply and demand adjustment and stabilization of the electricity grid system. By supplying carbon-neutral ammonia fuel and utilizing it in thermal power generation, the effect of reducing CO2 emissions can be obtained promptly. The energy value chain using ammonia is an effective measure for reducing CO2 emissions in areas where renewable energy resources are insufficient to meet their demand, such as Southeast Asia and in Japan.
The IHI Group has a track record of globally providing technologies for energy infrastructure including power generation plants, hydrogen and ammonia production and handling plants. Focusing on the potential of ammonia as an energy carrier, the IHI Group has been developing power generation technology using ammonia for boilers and gas turbines since 2013 and leading the world. Deploying the technology for the new energy value chain using ammonia will contribute to the global issue of greenhouse gas reduction. This paper introduces the value chain of fuel ammonia that the IHI Group is aiming for and the efforts to realize it.
2. Characteristics of ammonia as an energy carrier
Ammonia is used in various applications such as fertilizer, chemical raw material and refrigerant, but its characteristics as a fuel are not well known. Table 1 shows physical and combustion characteristics of ammonia, comparing with hydrogen and methane as typical fuels.
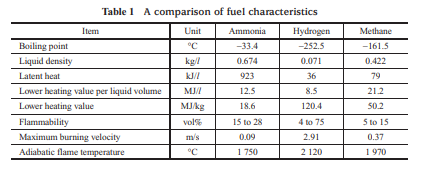
Since hydrogen has a low density and a small heating value per liquid volume, its transport efficiency is low, and conversion to substances with high transport efficiency has been investigated(3). Liquid ammonia contains 1.7 times as much hydrogen atoms per volume as liquid hydrogen and 1.5 times as much heating value. The boiling point of hydrogen is as low as -253°C, and a lot of energy is required for liquefaction, but the boiling point of ammonia is -33.4°C, which can be easily liquefied by a general-purpose refrigerator and easily handled.
The overall reaction formula of ammonia combustion is 4NH3 + 3O2 → 2N2+ 6H2O. As shown in the combustion flame of swirl burner in Fig. 1, ammonia forms self-sustaining combustion flame, but its flame length is longer than that of methane, which means the longer residence time is necessary to complete the combustion. Comparing ammonia combustion characteristics with those of methane, ammonia has 40% of methane’s lower heating value per weight, 200°C lower adiabatic flame temperature and one-fourth burning velocity. Therefore, the longer reaction time is required to stabilize flame and achieve complete combustion. Another challenge is to control the combustion emission. Since ammonia contains nitrogen atoms, NOx is easily generated in the combustion of the lean fuel mixture, while nitrous oxide (N2O) and unburned ammonia are generated in the rich fuel mixture. On the other hand, radicals (NHi) due to the decomposition of ammonia reduce NOx to nitrogen in a high temperature reducing atmosphere. The IHI Group has developed ammonia combustion technologies based on understanding of the above combustion characteristics peculiar to ammonia, and has achieved both flame stability and emission reduction, which will be introduced in Section 3.2. Along with the technology development, the IHI Group is promoting development of infrastructure for expanding the ammonia value chain (Fig. 2).
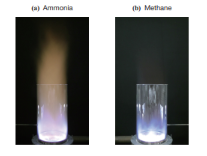
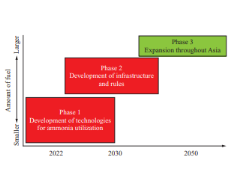
3. Ammonia energy value chain
Figure 3 shows the ammonia global value chain from the production to utilization. Ammonia is expected to be produced in areas rich in resources and renewable energy, mass-transported by ship, stored at receiving terminals, and used as fuel in thermal power generation, industrial heating furnaces, etc.
The world annual production of ammonia is approximately 200 million tons, and approximately 10% is distributed internationally. The main uses are fertilizers, chemical raw materials, and reducing agents of selective catalytic reduction for combustion exhaust gas treatment. When ammonia is also used as fuel, the distribution volume will be more than 10 times, and development of more efficient technologies and large investment are necessary to establish the value chain. In the short term, it is important to establish it promptly and realistic to utilize the existing infrastructure from production to power generation. In the medium to long term, it should be shifted to focus on its sustainability. The following is an introduction of our efforts toward the goal.
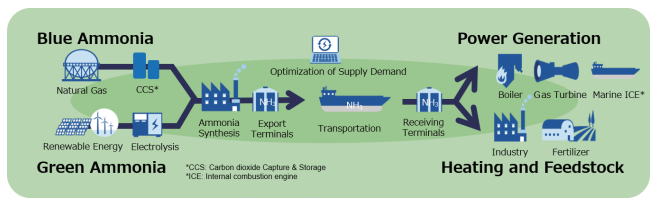
3.1 Ammonia production
The mass production technology for ammonia was established in the early 20th century, which is called the Haber-Bosch (HB) method. With this method, ammonia is synthesized from nitrogen and hydrogen. Production of 2 000 to 3 000 t/day per plant unit is a general scale. Toward the common use of ammonia as fuel, the plant scale-up (6 000 t/day or more) is under consideration to increase production efficiency and reduce the plant cost.
Carbon-neutral ammonia is classified into two types according to the method of production. One is blue ammonia, which uses fossil resources such as natural gas as raw materials and captures and sequesters CO2emitted from production processes. During the processes, CO2 is mainly emitted from the raw material synthetic process line and the combustion exhaust gas of the steam methane reformer (SMR). The IHI Group has developed technology for capturing CO2 in boiler exhaust gas(4) and using the captured CO2. The other is green ammonia, in whose production process used are renewable energy and hydrogen obtained by some methods of electrolysis of water, such as alkaline electrolysis, polymer electrolyte membrane fuel cell (PEMFC), and solid oxide fuel cell (SOFC). The IHI Group has developed an energy management system that optimizes electrolyzers’ operation with the use of renewable energy and is continuing study to increase the scale. A problem with the synthesis process is that the HB reaction pressure (10 to 30 MPa) is much higher than the pressure of hydrogen produced in electrolyzers at normal pressure or low pressure, and a lot of power is required for compression. Therefore, researches of catalysts with sufficient reaction efficiency at low pressure are ongoing.
The IHI Group has experiences of participation and achievements in the engineering, procurement, and construction business and providing technologies of hydrogen and ammonia production plants. Currently, a feasibility study(5) is being conducted in Australia for a green ammonia production plant that utilizes renewable energy (Fig. 4). This uses 250 MW hydropower to produce 200 000 tons of ammonia annually. The IHI Group aims to provide the optimized process design and technology according to the feedstocks and energy resources.
In the short term, developments of the blue ammonia production are proceeded to establish the energy value chain promptly and will be shifted to green ammonia. The cost of green ammonia production mainly depends on that of the electricity and electrolyzer. It is estimated that the cost of electricity needs to be $30/MWh or less for the green ammonia to be as priced as the blue one(6). Australia, Middle East and South and North America have good prospects of smooth transition from blue to green because of their abundant natural gas resources and renewable energy resources shown in Fig. 5.
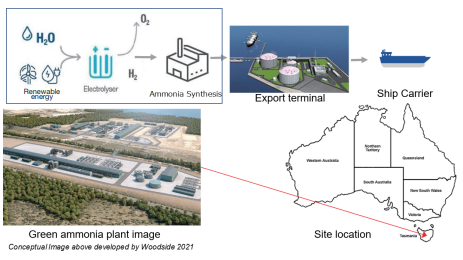
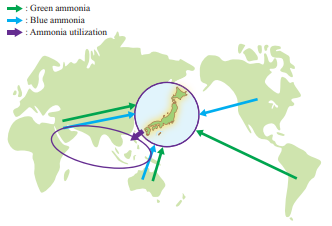
3.2 Power generation using ammonia fuel
Focusing on the potential of ammonia as a hydrogen energy carrier, the IHI Group has been developing ammonia combustion technology for large-scale boilers and gas turbines for power generation since 2013, and participated in the Energy Carrier project(3) of the Strategic Innovation Promotion Program (SIP) in 2014–2018.
The gas turbine has excellent load following performance, and when combined with an exhaust heat recovery steam generator, it enables cogeneration with a total heat utilization of over 85% and high-efficiency power generation with thermal efficiency of over 60%. The method of supplying ammonia to gas combustor is classified into gas supply method, liquid supply method, and reformed gas supply method, in which the gas is supplied after being partially decomposed into hydrogen and nitrogen by a catalyst. The IHI Group has advanced the development of ammonia gas and natural gas co-firing technology and achieved 20% co firing by the gas supply method with a 2 MW gas turbine (Fig. 6)(7). To achieve the higher co-firing ratio, a spray combustion technology has been developed. Liquid ammonia is easily handled in the pressurized conditions such as gas turbine. Stable combustion has been achieved up to 70% co firing ratio with natural gas while meeting Japanese environmental regulation with SCR (Selective Catalytic Reduction) exhaust gas treatment, and further development is underway for ammonia single firing.
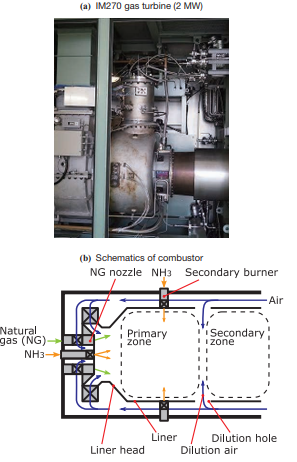
For coal-fired large-scale boilers for power generation, we have been developing ammonia co-firing technology for pulverized coal and ammonia. The IHI Group has succeeded in developing a 20% ammonia co-firing combustion technology. The technology achieved NOx emissions equal to or less than single coal firing as shown in Fig. 7(8). In addition, the IHI Group, in collaboration with JERA Co., Inc., a power generation company in Japan, is going to demonstrate the ammonia co-firing technology in a 1 000 MW coal-fired power plant for commercial operation in 2024 as a project of NEDO (JPNP16002) (Fig. 8). The only part of the plant to be modified for co-firing is the combustion burner, and the fuel supply equipment, exhaust gas treatment equipment and pressure parts of the boiler do not require to be modified. When 20% ammonia is co-fired in a 1 000 MW boiler power generation facility, the annual ammonia consumption is estimated to be 500 000 tons, which is almost half of the current demand for ammonia in Japan. In addition, the amount of CO2 emission reduction will be 1 million tons. The IHI Group is developing a high co-firing ratio and ammonia single combustion technology for boilers.
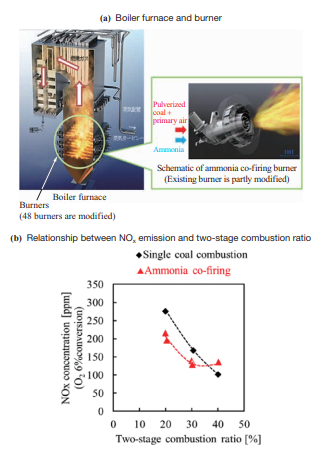
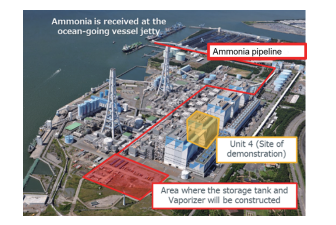
3.3 Storage and transportation of ammonia
An ammonia receiving terminal is required to be near the demand area. The IHI Group has provided technologies related to the main equipment for liquid gas (LAG) storage and its supply. Ammonia storage tanks are divided into double-walled metal tank type single containment and pre-stressed concrete (PC) full containment tank to prevent leakage to the outside and improve heat insulation. Both have excellent leak prevention functions, but the PC tanks are used for large storage equipment because of their ease of strength design.
Ammonia is transported as LAG with atmospheric pressure and boiling temperature (-33.4°C) for mass transportation by large carrier vessels and as pressurized LAG for small size transportation by coastal vessels. Since the boiling point of ammonia is close to that of liquefied petroleum gas, they can be transported at the same time. In addition, in order to reduce CO2 emissions in ship transportation, the IHI Group has been developing ammonia combustion technology for marine engines on tugboats toward service launch in 2024 (Fig. 9
(9)) and plans to expand its application to other engines.
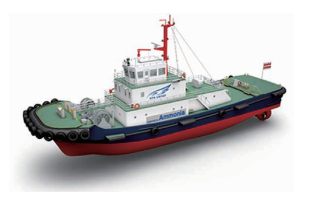
4. Summary
In order to establish an ammonia energy value chain, it is necessary to develop standards related to technology and operation. The Clean Fuel Ammonia Association in Japan that consists of companies interested in the ammonia value chain, is proceeding with the study.
What ammonia carries is not only energy but also cold heat. The latent heat of liquid ammonia is larger than that of liquefied natural gas and liquid hydrogen, and it is possible to supply heat to cold storage warehouses, data centers and buildings. After establishing the value chain in Japan, it will expand into regions with similar issues as Japan, such as Asian region. The IHI Group can provide many technologies in the ammonia value chain, from production to energy conversion in thermal power generation, and is making efforts toward the realization through new technology development and joint business development with partners.
REFERENCES
(1) International Energy Agency : The Role of Low Carbon Fuels in the Clean Energy Transitions of the Power Sector, 2021
(3) Strategic Innovation Promotion Program (SIP) Energy Carrier : , 2015, accessed 2022-02-18
(4) S. Okuno, S. Nakamura, Y. Yamanaka, T. Matsuyama, H. Sato and R. Ikeda : Demonstration results on advanced amine solvents, packings and process at IHI’s Aioi pilot plant, Energy Procedia 114, 2017, pp. 1 282- 1 287
(6) J. Armijo and C. Philibert : Flexible production of green hydrogen and ammonia from variable solar and wind energy: Case study of Chile and Argentina, Inter. J. Hydrogen Energy, 45, 2020, pp. 1 541-1 558
(8) H. Ishii, E. Ohno, T. Kozaki, T. Ito and T. Fujimori : Development of co-firing technology of pulverized coal and ammonia for suppressing the NOx generation, Trans. the JSME (in Japanese) 86 (883) 2020, DOI: 10.1299/transjsme.19-00363