Carbon-Neutral Thermal Power Generation Using Ammonia Combustion technology development and boiler design to expand use of ammonia
IHI Corporation
Although use of variable renewable energy power sources has been expanding, thermal power generation is still recognized to be a power source that is necessary for balancing of power supply and demand and power grid stabilization. Therefore, reducing carbon dioxide (CO2) emissions is an urgent issue for thermal power generation. This article introduces the development and future prospects of technologies to use ammonia, which is attracting attention as a solution to this issue, in coal-fired power plants.
HANAOKA Ryo
R&D Department, Engineering Center, Carbon Solution Business Unit,
Resources, Energy & Environment Business Area, IHI Corporation
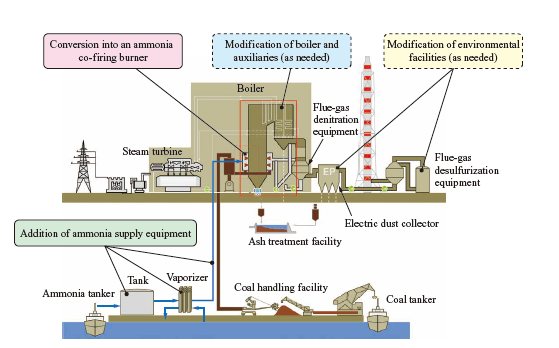
Introduction
To curb global warming, there is great need to reduce CO2 emissions around the world. In Japan, the government has declared the aim to achieve carbon neutrality by 2050. In thermal power generation, high-temperature, high-pressure steam is generated by burning fuel, and the generated force of the steam is used to turn generators. Inmost cases, coal, petroleum, natural gas, and other fossil fuels are used as fuel, and among these fuels, use of coal has expanded because it is inexpensive and can be supplied stably. The IHI Group has top-level coal utilization technologies and has been delivering thermal power generation facilities with the world’s highest efficiency, thereby contributing to CO2 emissions reduction.
However, there is a need to shift to carbon-free fuels, which emit no CO2. Ammonia is a promising carbon-free fuel. The combustion reaction formula of ammonia is 4NH3 + 3O2 → 2N2+ 6H2O, and ammonia emits no greenhouse gases when burned. Although hydrogen also emits no greenhouse gases when burned (2H2 + O2 → 2H2O), hydrogen has low transport efficiency because of its low combustion calorific value per unit volume with a low density, and much energy is required for hydrogen liquefaction. Therefore, efficient mass transport is an issue.
By contrast, ammonia, as an energy carrier, is more advantageous in terms of volumetric efficiency and liquefaction temperature (-33.4°C) than hydrogen. The figure above shows ammonia’s characteristics as an energy carrier. Ammonia is already commercially available in the chemical industry for uses such as fertilizer production; therefore, infrastructure is in place for producing, storing, and transporting large volumes of ammonia, and technologies for handling ammonia have been established.
For this reason, the IHI Group has been focusing on ammonia for carbon-neutral thermal power generation. We began to introduce ammonia co-firing with coal (for boilers) or natural gas (for gas turbines), which are currently mainstream fuels for thermal power generation, and we are continuing development with a view to single firing.
This article introduces the development of ammonia co-firing technologies for thermal power generation boiler facilities as well as relevant boiler designs.
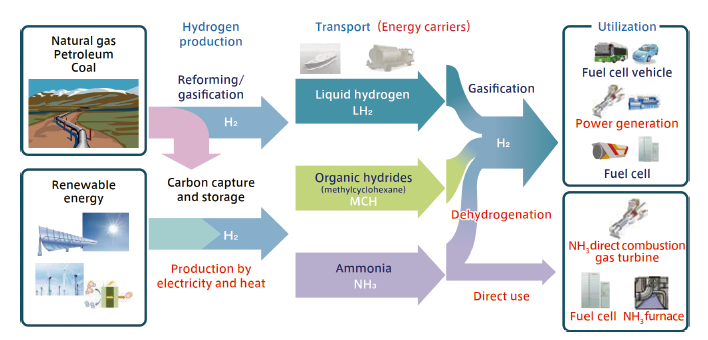
Characteristics of ammonia as an energy carrier
(Source: SIP (Cross-ministerial Strategic Innovation Promotion Program)
“Energy Carrier,” (https://www.jst.go.jp/sip/pdf/SIP_energycarriers2016_en.pdf )
Challenges for and realization of ammonia co-firing
Ammonia is widely used as a chemical feedstock or fertilizer, but it is rarely used as a fuel. Therefore, to use ammonia as a fuel, we first developed numerical analysis models while conducting testing and verification with our own combustion test furnace in order to confirm the basic combustion characteristics of ammonia.
Ammonia has a lower burning rate and flame temperature than other conventional fuels, such as methane. Also, there is a need to reduce the amount of nitrogen oxide (NOx) generated by the nitrogen components in the fuel. Reliable ignition and stable combustion are important, but the combustion conditions for achieving them have a trade-off relationship with low NOx emissions. In combustion technology development, it is important to strike a good balance between the two.
We studied optimal ammonia injection and mixing methods for pulverized coal burner flame through numerical analysis of ammonia co-firing with pulverized coal. For the mixing methods in this study, we used pulverized coal flow mixing, combustion air mixing, and direct furnace injection. The study found that NOx can be reduced effectively by feeding ammonia into a highly reducing atmosphere with a high gas temperature (direct furnace injection). The schematic below shows an ammonia co-firing burner for achieving this.
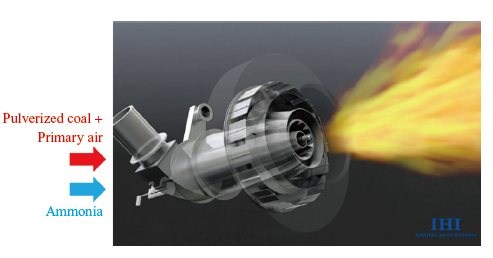
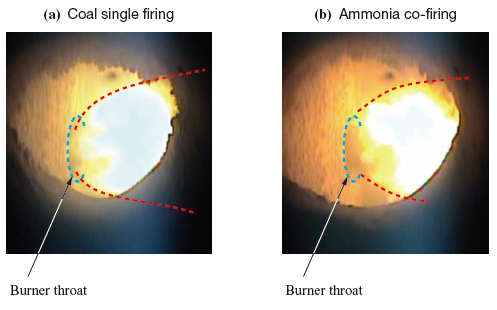
co-firing in a large combustion test furnace test
Based on this study result, we prototyped burners for combustion testing and conducted basic tests with a small combustion test furnace (1 MWth) and then with a large combustion test furnace (10 MWth). With respect to the latter, the photos shown at the end of the previous page show a comparison of the flame between coal single firing and ammonia co-firing. The results of these tests show that stable combustion was achieved when the ammonia mixing ratio was 20% in terms of the combustion calorific value. In addition, the NOx emissions and unburned content were at the same levels as those in pulverized coal single firing. The graph on the next page shows a comparison of the effects of the two-stage combustion ratio on NOx emission behavior between coal single firing and ammonia co-firing. In addition, we confirmed that favorable results can be obtained even under conditions that simulate partial load operation, and the developed ammonia co-firing burner can be used in actual facilities.
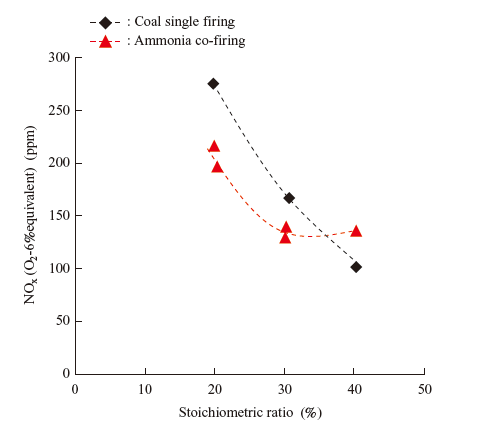
In parallel with burner development, we evaluated the effects on the boiler and auxiliaries with numerical analysis for the boiler and other methods. The lower left figure shows a comparison of the furnace analysis results between coal single firing and ammonia co-firing. We conducted studies with a model plant and confirmed that in 20% ammonia co-firing, there is basically no need to modify the heat transfer section, including the pressure-containing parts of the boiler, ventilation system, or environmental facilities. However, modification may be required depending on the facility design conditions, facility conditions, and coal properties.
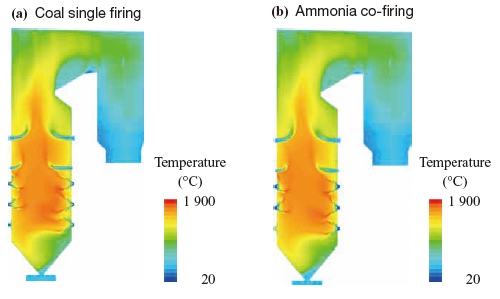
These efforts were made, based on our past research results, as part of a SIP (Cross-ministerial Strategic Innovation Promotion Program) project between 2017 and 2018 and a project by the New Energy and Industrial Technology Development Organization (NEDO) between 2019 and 2020.
A demonstration project started in August 2021. The figure on the first page shows a schematic of the ammonia co-firing plant. The demonstration experiment is planned to be conducted with a mixing ratio of 20% in terms of the calorific value, and the developed combustion technologies and modified designs will be verified to enhance technical reliability and to obtain data for achieving a higher mixing ratio in the future.
Development of technologies for co-firing with a higher ammonia mixing ratio
To achieve co-firing with a higher ammonia mixing ratio, there is a need to overcome the following challenges related to combustion, the boiler and auxiliaries as well as control and operation.
- < Combustion >
- - The increased amount of ammonia, which has a lower burning rate, results in an unstable combustion flame.
- The decreased amount of coal burned results in a decreased operational margin in operation around the lower limit for the coal pulverizer. - < Boiler and auxiliaries >
- - Because the amount of heat stored in the furnace and the amount of combustion air change, the boiler and auxiliaries need to be modified.
- < Control and operation >
- - Because the control and operation conditions of ammonia co-firing facilities differ from those of existing facilities, modifications are required with regard to control and operation.
To overcome the combustion-related challenges, we are conducting numerical analysis and verification with small combustion furnace tests and will continue burner development with large combustion test furnaces. As for the boiler-/auxiliary-related challenges, we will use an actual facility as a model and conduct numerical analysis and study the facility specifications to assess the effects. With regard to the control-/operation-related challenges, we will conduct an evaluation by operational simulation using the actual facility selected as a model.
Considerations in boiler design
In thermal power generation boilers, ammonia has been used as a denitration reducing agent, but to use ammonia as a fuel, the following considerations are required.
- Achieving the required performance of each piece of equipment and simulating their operation methods, operational restrictions, and constraint conditions
- Stably supplying ammonia
- Ensuring safety in ammonia handling
With regard to equipment specifications and performance, we will evaluate the effects of ammonia co-firing based on operational data and operational restrictions of existing facilities in order to set the target performance and operational constraints. As for the operation methods of each piece of equipment, we will study them in consideration of the changes made to well-proven operation methods for gas fuels in order to realize ammonia co-firing.
To ensure stable ammonia supply, adequate ammonia supply facilities are required; in general, these must include an ammonia receiving facility, storage facility, vaporizer, and pretreatment facility. The specifications of each facility are determined mainly based on the amount of ammonia used, which is in turn determined based on the boiler’s specifications, the required storage period, and ammonia receiving conditions. For the vaporizer, there is a need to select a heat source, and based on the selected heat source, to determine the equipment specifications and to study the operation method.
With regard to safety, ammonia must be handled carefully because it is a deleterious substance. In thermal power plants, however, ammonia is commonly used for denitration equipment to remove NOx from flue gases, and it is handled safely by qualified personnel according to a standardized handling procedure. When ammonia is used as a fuel, a larger amount of ammonia is used, and the handling procedure will be developed by government experts. However, it is thought that ammonia can be used safely by updating existing procedures and know-how.
Future challenges to overcome for widespread use of ammonia co-firing
To apply ammonia co-firing to thermal power generation facilities, a demonstration test has been conducted with a mixing ratio of 20% in terms of the calorific value. It is important for us to plan, implement, and evaluate this demonstration test without fail. Through this demonstration test, we will extract the challenges to overcome for commercialization and solve them in order to establish ammonia co-firing technology. Expectations for ammonia fuel, which will contribute to carbon neutrality, are rising rapidly. Demonstrating an integrated value chain from production to utilization will lead to the full-scale introduction of ammonia fuel.
It is important to increase the ammonia mixing ratio and also to develop power generation technologies for single firing. At the same time, there is a need to develop burners for a higher mixing ratio and to study boilers for a higher mixing ratio.
To achieve zero-emission thermal power generation, it is necessary to use ammonia, the production of which does not emit any CO2. It is essential to introduce blue ammonia, which is produced by capturing, utilizing, and storing CO2 emitted from conventional production using natural gas or petroleum as a raw material (CCUS : Carbon dioxide Capture, Utilization, and Storage), and green ammonia, which is produced using hydrogen derived from renewable energy. What is paramount is to develop an environment where blue ammonia and green ammonia can be supplied stably at reasonable prices.
Needless to say, solving these challenges requires not only technological development but the development of strategies and laws, which require governmental commitments.
Conclusion
With the aim of achieving carbon neutrality by using ammonia in thermal power generation facilities, this article has introduced our efforts to develop ammonia co-firing technologies and the considerations required to further increase the ammonia mixing ratio in combustion technology development and boiler design, with a focus on ammonia utilization technologies.
The following summarizes the characteristics of ammonia and current co-firing technologies for thermal power generation facilities.
- Ammonia’s strengths include long-distance transport and long-term storage of hydrogen energy.
- The greatest advantage of ammonia, which is a flammable gas, is that it can be used directly as a fuel for thermal power generation boilers. There is a need to improve combustibility and to reduce Fuel-NOx (NOx derived from nitrogen contained in fuel) and unburned components, but there are prospects that the necessary technologies will be established, and we have almost reached the point where a demonstration test with actual facilities is conducted.
- Ammonia is still expensive compared to conventional fossil fuels. Widespread use of ammonia requires a larger supply chain and support from the government, and social implementation, or equivalently commercialization, requires cost reduction, incentives, and other measures.
To realize carbon-neutral thermal power generation facilities, the IHI Group has started to develop ammonia-pulverized coal co-firing technologies ahead of other companies, and will further sophisticate utilization technologies and offer solutions to challenges identified in practical operation, thereby contributing to the achievement of carbon neutrality in the world. The IHI Group will continue to lead the development for the widespread utilization of ammonia in Japan.