Realizing Large-Volume Ammonia Tanks and Establishing New Test Method
Technology for realizing large-volume ammonia tanks, considered difficult to construct
IHI Plant Services Corporation / IHI Corporation
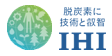
Ammonia is seen as a next-generation fuel. Ammonia is generally seemed easier to transport and store than hydrogen, and technologies for handling ammonia have already been established. However, there are many challenges that should be solved in constructing large-volume tanks necessary for producing and using great volumes of ammonia as a fuel. This article introduces the IHI Group’s efforts to realize large-volume ammonia tanks.
Necessity and challenges for constructing large-volume ammonia tanks
Storage tanks are necessary in order to produce and use ammonia as a fuel. When considering the size of a fuel tank, it may be helpful to compare the fuel’s calorific value per unit volume in liquefied form, in which it is stored, against those of other fuels. Ammonia’s calorific value per unit volume is approximately 60% of that of methane, which is the main component of liquefied natural gas (LNG). Therefore, to use ammonia as an alternative fuel to LNG, approximately 1.7 times as much methane storage would be required.
Currently, ammonia tanks used in the chemical industry in Japan can store around 10 000 to 20 000 t (in weight) of ammonia, and it is said that the limit with existing technology is around 40 000 t, which is equivalent to a volume of approximately 60 000 m3. Considering that common LNG tanks have a capacity of 200 000 m3 or more, the storage capacity of just 60 000 m3 is too small. Consequently, producing and using ammonia as a fuel in a commercially viable way requires much bigger tanks.
However, there are challenges for increasing the size of ammonia tanks. Considering that a tank must be able to store more than 10 000 t of ammonia in liquid form, a flat-bottomed cylindrical tank would be appropriate. A typical flat-bottomed cylindrical prestressed concrete (PC) tank has an inner tank made of steel whose outside is covered with thermal insulation, which is further covered with a concrete dike. The steel inner tank of a flat-bottomed cylindrical PC tank holds the internal pressure, and the welding seams in the inner tank must undergo post-weld heat treatment (PWHT) as required by the applicable standard. However, it is not realistic to apply PWHT to the entire large-volume tank, so we need to design a tank with a plate that is thin enough to be exempted from the PWHT requirement. Existing steel plates currently used for ammonia tanks, whose thickness is 38 mm or less, are exempt from PWHT. However, a tank manufactured with this plate thickness is not strong enough to hold more than 40 000 t in terms of strength. This is why it is said that the maximum capacity of ammonia tanks is 40 000 t with existing technology. In order to increase the size of the tank within the plate thickness limit, it is necessary to increase the strength of the steel material for the inner tank.
On the other hand, there is a concern that the inner tank, which directly contacts with ammonia, is likely to develop ammonia stress corrosion cracking (SCC). It is known that higher-strength steel is more likely to develop ammonia SCC, and various guidelines around the world have set upper limits on tensile strength, yield strength, and hardness of welding seams for steel materials accordingly. It is contrary to the intention of the guidelines to increase the strength of the steel material for the inner tank with the plate thickness limit that exempts PWHT. To solve this problem, we first need to select a high-strength steel that is stronger than specified in the guidelines and is less susceptible to ammonia SCC.
Tank open inspections conducted to check tanks for damage due to ammonia SCC pose another challenge. Tank open inspections are conducted periodically on ammonia tanks that are likely to develop such corrosion, but they are very expensive in terms of time, money, and the need to prepare spare tanks, so place a big burden on users.
Developing a new test method for ammonia SCC
The ammonia SCC test method is effective for selecting a steel type that is less susceptible to ammonia SCC. Ammonia SCC tests had been conducted by many researchers until around the 1980s, and it is known from the findings of those tests that higher-strength steel types are more susceptible to ammonia SCC. In the 1980s, there was no demand for large-volume ammonia tanks, and low-strength aluminum-killed steel with a thickness of up to 38 mm was used for ammonia tanks to reduce the risk of their developing ammonia SCC. Today, there is a larger number of steel types available than back then, so it is worth establishing a new ammonia SCC test method. Consequently, based on information in existing literature, we developed a method for testing the susceptibility of steel materials to ammonia SCC under low temperature and low pressure.
Ammonia is easily liquefied when cooled to a low temperature. Testing under low temperature and low pressure enables to operate test equipment under a pressure that does not conflict with the High Pressure Gas Safety Act of Japan, and such equipment is relatively easy to introduce. Generally, SCC has a latency period and it will occur after a certain period of time, and this holds true for SCC in liquid ammonia. It is reported that even HT60, which is a high-strength steel type susceptible to ammonia SCC, takes two years or longer to develop SCC in a normal liquid ammonia environment. Consequently, to evaluate the susceptibility of steel types to ammonia SCC in a limited period of time, it is necessary to accelerate the development of SCC. As existing literature suggested that SCC could be promoted by electrochemically controlling a parameter of SCC test specimens called the electric potential, we adopted this method. The ammonia SCC test equipment built by the IHI Group has a container, into which is placed a test specimen subjected to stress by a jig in advance. The test specimen in the container is connected to external electrochemical test equipment so that its electric potential can be controlled. Note that platinum (Pt) is used for the reference electrode and the counter electrode in liquid ammonia. The entire container is installed in a low-temperature tank and equipped with piping and valves to let ammonia gas in and out.
We adjusted stress factors that affect ammonia SCC (the test specimen shape and the applied stress) and environmental factors that also influence ammonia SCC (the oxygen concentration, the water concentration, and the amounts of supporting electrolyte salt and the chemical added to enable electric potential control), and then examined whether SCC could occur with some steel types (such as HT60 and HT80) that are thought to be more likely to develop ammonia SCC by controlling their electric potential. As a result, we were able to develop cracks with HT60 and HT80 in the one-week ammonia SCC test. When the test specimens were observed with an optical microscope, HT60, which develops no cracks when exposed to an inert, low-temperature environment, was found to have developed SCC from the edge (bottom of the notch) of the test specimen.
Adoption of SUS821L1
We have never seen any reports on the development of ammonia SCC in SUS304 and other austenitic stainless steels, but because stainless steel of this type is not as strong as carbon steel, the plate thickness must be increased. In addition, it is very expensive. As such, adopting this steel type for large-volume tanks that use several thousand tons of steel is unrealistic.
Therefore, as the steel material candidate for the inner tank, we focused on duplex stainless steel. Duplex refers to a steel comprising an austenite phase and a ferrite phase in a 50:50 ratio. Of the different types of duplex stainless steel, SUS821L1, which is called lean duplex stainless steel due to its low nickel content, is high-strength and stable in price. In addition, SUS821L1 is highly resistant to corrosion and is reported to be equivalent to SUS304 in susceptibility to SCC in a normal neutral aqueous solution environment.
The IHI Group has studied properties of SUS821L1 and worked on the development of technologies for welding and processing it, and in around 2015, it started adopting SUS821L1 as a material for watergates and other products. To adopt SUS821L1 as the steel material for the inner tank of ammonia tanks, we must further study its performance — including its reliability and soundness against ammonia SCC. Having developed the new ammonia SCC test method, we designed a prototype tank using our technologies for welding and processing SUS821L1 and conducted a performance test on welding seams. The test results indicated that a tank capacity of up to 110 000 t is viable with a prototype tank design that includes the PC frame and other structures. When SUS821L1 was tested using the ammonia SCC test method developed by IHI, cracks did not develop during a one-week test, in which high-strength steel develops SCC. This result indicates that SUS821L1 is less susceptible to ammonia SCC. Future work will involve conducting long-term ammonia SCC tests on SUS821L1 using the test specimens collected from the welded joints to confirm whether this steel material is indeed less susceptible to ammonia SCC. If the test results demonstrate that the material will not develop or is very unlikely to develop ammonia SCC, tanks made of SUS821L1 will contribute to reducing the burden on users by eliminating the need for them to conduct tank open inspections or enabling them to reduce the inspection frequency.
Adoption of PC membrane
The IHI Group believes that the PC membrane tank will be the most promising candidate type in the future, so has been working on the development of this technology. A membrane is a 2-mm-thick thin plate made of SUS304, and has corrugations for absorbing thermal shrinkage. The membrane does not hold pressure by itself but transmits pressure to the thermal insulation and the PC frame to hold the contents. This extremely rational design using membranes is applied to all underground LNG tanks in Japan.
When the membranes are used in the PC frames of aboveground LNG tanks, this kind of tanks is called PC membranes. Whereas a standard on PC membranes has not yet been set in Japan, European Norm (EN) and American Petroleum Institute (API) standards specify requirements for PC membranes and in these regions, they have been put into practical use in LNG tanks. The IHI Group has worked on the development of PC membranes for LNG since the 1990s, and our product type was prequalified (homologated) by Shell International Oil Products B.V. in 1999.
Membranes remain 2 mm thick regardless of the tank capacity and are free of the challenging PWHT requirement, enabling us to solve the challenge of plate thickness when constructing large-volume tanks. In addition, since there have been no reports of ammonia SCC development in SUS304, which is used as the steel material for membranes, tanks made of it are epoch-making in that they eliminate the need to conduct tank open inspections. Moreover, since tank size does not depend on the thickness of the steel material, it may be possible to construct a supersized ammonia tank.
It is qualitatively known that large-capacity tanks have a cost advantage over smaller ones, and as a result of designing a prototype PC membrane tank with a capacity of 40 000 t, we found that it could be constructed at a lower cost than standard PC tanks of the same size. Another advantage of a PC membrane tank is that it takes less time to construct. At present, the IHI Group has also completed designing a prototype PC membrane tank with a capacity of 110 000 t, and is in the process of determining the upper capacity limit for large-capacity tanks.
Conclusion and challenges for the future
The IHI Group has developed our own ammonia SCC test method and test equipment, and has been conducting ammonia SCC tests on various steel materials. We have completed designing a prototype flat-bottomed cylindrical PC tank with a capacity of 110 000 t using SUS821L1, and are in the implementation stage, but will continue exploring steel materials that are even more cost-effective and even less susceptible to ammonia SCC. When it comes to PC membranes, we have completed the development of the technologies for the main elements. However, there are no tanks of the same type in Japan, we would like to start taking action to obtain permits and licenses together with users. In addition, toward realizing supersized tanks, which is the most attractive feature of PC membranes, we have started to examine the maximum allowable capacity for tanks of this type.
In our new efforts to use ammonia as a fuel, we cannot make the tank size issue a bottleneck. The IHI Group will therefore strive to continue development to provide large-volume ammonia tanks that are inexpensive and, above all, safe.