Technologies for Reducing Greenhouse Gas and Air Pollutants in New Medium-Speed Diesel Engine "25AHX"
MIMURA Takahisa, KATO Shoji
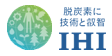
MIMURA Takahisa : RE Design & Development Department, Engineering & Technology Center, IHI Power Systems Co., Ltd.
KATO Shoji : Manager, RE Design & Development Department, Engineering & Technology Center, IHI Power Systems Co., Ltd.
As efforts for environmental conservation including global warming prevention, it is essential to reduce emissions of carbon dioxide (CO2) and other greenhouse gases and take measures toward carbon neutrality. In response to these requirements, IHI Power Systems Co., Ltd. has developed and delivered alternative-fueled engines and hybrid and electric propulsion systems. In addition to reducing greenhouse gas emissions, it is still indispensable to reduce air pollutants. To satisfy both of reducing greenhouse gas emissions and air pollutants, IPS developed new diesel engine “25AHX,” which has reduced fuel consumption and nitrogen oxide (NOx) emissions 30% lower than the International Maritime Organization (IMO) Tier II regulation and complies with Chinese maritime exhaust gas regulations. This engine is planned to be available with ammonia, carbon-free fuel. This paper reports on technologies for reducing fuel consumption and NOx in this new engine and their effects.
1. Introduction
Internal combustion engines have been improved and evolved ever since they were first invented, and their convenience has seen their uses diversify and expand worldwide. As such, internal combustion engines have contributed immeasurably to the development of civilized society and the higher living standards. However, their exhaust gases contain both greenhouse gases (GHG) and air pollutants that affect the global environment. The major components of GHGs and air pollutants are carbon dioxide (CO₂) and nitrogen oxide (NOx), respectively.
To deal with the rise of pollution to the level of being a social problem in Japan, laws and treaties were enacted to regulate exhaust emissions. Regarding the emissions from diesel engines, since February 1987, NOx, sulfur oxide (SOx) and soot dust have been subjected to legal controls (the Air Pollution Control Act).
Similarly, for marine diesel engines, the International Maritime Organization (IMO) put MARPOL Annex VI into effect on May 19, 2005, to regulate NOx and SOx emissions. Regarding NOx regulation, as of 2023, Tier II has been applicable to general maritime areas and Tier III has been applicable to emission control areas (ECAs) such as the Baltic Sea and North American coastal areas. Figure 1 shows the NOx emission limits specified by the IMO.
In China, CHINA II(1), which is a regulation for marine engine emissions (GB15097-2016) stricter than the IMO’s Tier II, has been applicable to the China domestic vessels built after July 2022. The NOx emission limit for engines with an output of 1 000 kW or more and less than 2 000 kW is approximately 30% lower than that of IMO Tier II. For conventional engines to comply with the regulation, they need to undergo significant changes in specifications and equipment composition.
As for GHGs, international efforts to fight climate change started with the adoption and effectuation of the Kyoto Protocol in 1997 and February 2005 respectively.
Following the Kyoto Protocol, the IMO also adopted GHG Reduction Strategy in 2018, when the following three numerical goals compared to 2008 were set for the international maritime shipping industry. Since then, the regulations are being tightened at an accelerated rate in order to improve the global environment.
- CO₂ emission reduction by 40% or more by 2030,
- GHG emission reduction by 50% or more by 2050, and
- Zero GHG emissions as soon as possible in this century.
IHI Power Systems Co., Ltd. (IPS) developed Japan’s first marine diesel engine in 1919, and has been quick to deal with the environment-related regulations as mentioned above as they have taken effect. In 2010, IPS released the 28AHX (2 000 to 6 500 kW), an environmentally friendly diesel engine that achieves low NOx and low fuel consumption, and so has helped to improve the global environment. IPS has developed the 25AHX, a new diesel engine that achieves both improved fuel efficiency for the prevention of global warming and compliance with stringent environmental regulations.
This paper describes technical findings while developing the 25AHX engine, with respect to CO₂ and NOx reduction through lowering fuel consumption.
2. Outline of the 25AHX engine
IPS developed the 25AHX engine, as part of the AHX series capable of coping with environmental problems, to meet the needs of new era. This series has been developed to replace the HX series, which comprises engines with an output of 1 000 to 2 000 kW that are widely used as conventional marine engines. The 25AHX was developed by applying the low-NOx technology acquired through the development of the 28AHX(2), which is also one of AHX series, so as to be lower in fuel consumption than conventional engines and to realize NOx reduction by 30% from the emission limit specified in the IMO Tier II. Table 1 shows the main engine specifications of the 25AHX and Fig. 2 shows an exterior view of it with its six cylinders (6L25AHX). The 25AHX was designed with due consideration to engine size, assuming that it would replace the HX series and improve maintenance performance of components, so as to accommodate customers who have used the HX series.
3. Performance improvement and environmental measures of the 25AHX engine
3.1 CO₂ and NOx generation from diesel engines and methods for reducing them
CO₂ is the GHG generated when carbon (C) in fossil fuel combusts with oxygen (O₂) in the air. The most effective way of reducing CO₂ discharged from diesel engines is to replace fossil fuel with biofuel or to use carbon-free fuel such as ammonia (NH₃), hydrogen (H₂). In the case of using conventional heavy oil as fuel, the most effective way of reducing CO₂ is to reduce the fuel consumption rate (fuel efficiency). Effective ways to cut fuel consumption are to increase combustion temperature or extend the period when combustion gas are exposed to high temperature during combustion.
As for NOx varieties, which are air pollutants, there are thermal NOx generated when nitrogen (N₂) and O₂ in the air react with each other through combustion, and fuel NOx generated when nitrogen (N) in fuel oil chemically reacts with O₂ in the air. The majority of NOx discharged from diesel engines is thermal NOx. An effective way of reducing the thermal NOx through the improvement of combustion of diesel engines is to lower combustion temperature. Figure 3 shows the mechanism of NOx generation.
As described above, the fact that the effective ways of reducing fuel consumption and NOx through improving combustion temperatures are directly contrary to each other clearly shows that there is a trade-off relationship between reducing fuel consumption and cutting NOx generation. Thus, it is technically difficult for diesel engines to simultaneously achieve reductions in both fuel consumption and NOx generation, so it is important to figure out an optimal condition effective for reducing both fuel consumption and NOx generation.
3.2 NOx reduction technology in the 25AHX engine
Because the 25AHX needs to realize low NOx emission and fuel consumption, as is the case with the 28AHX, the 25AHX adopts, in addition to the same Miller cycle as the 28AHX, a high-pressure ratio turbocharger and a variable intake valve timing (VIVT) mechanism as shown in Fig. 4. Outlines of these technologies are described in what follows.
- Miller cycle (early closure of the intake valve)
The Miller cycle is a combustion technology to suppress NOx generation through reducing combustion temperature. This technology advances intake valve close timing (IVC) so that an intake valve closes before the bottom dead center in an intake stroke. With this control, an engine undergoes adiabatic expansion with an intake valve closed and the temperature at the bottom dead center decreases, resulting in the decrease of the compression end temperature when the compression pressure ratio is constant. Reduction in combustion temperature along with the decrease of the compression end temperature leads to suppressing NOx generation.
- High-pressure ratio turbocharger
Adopting the Miller cycle enables the intake valve open period to be shorter than an engine without the Miller cycle. Therefore, it is necessary to select a high-pressure ratio turbocharger so that enough air can be supplied to a cylinder in a short time.
- VIVT mechanism
There are concerns about aggravated combustion due to air shortage in a cylinder when the rotation speed of the turbocharger is insufficient at low load. Thus, the VIVT mechanism has been adopted to optimize intake valve open and close timings (particularly IVC) when the engine is operating under a low load. This mechanism enables valve open and close timings to be switched while the intake valve open period stays constant.
3.3 IMO-compliant specifications and performance of the 25AHX engine
Because the 25AHX engine’s performance needs to meet the requirements in the IMO Tier II with fuel consumption minimized, 1D cycle simulation was conducted to preliminarily verify the performance. However, the errors between simulated and actually measured NOx emissions were too large to correctly evaluate the engine’s performance with the simulation results. Thus we studied how to reduce NOx emissions with reference to the evaluation(3), which focuses on the correlation between the ratio (Pmax/Pcomp) of maximum cylinder pressure (Pmax) to compressive pressure (Pcomp) and NOx.
Also, as mentioned above, in order to address the concern that a Miller cycle engine undergoes a shortage in the amount of air injected into a cylinder when the engine is operating under a low load, the VIVT mechanism was adopted to improve combustion through optimizing intake valve timing. This would maximize the amount of air injected into a cylinder during low-load operation (at a load factor of 25%). The 1D simulation was then conducted to identify the condition (i.e., the intake valve timing that maximizes the excess air ratio) that optimizes the engine’s low-load operation. Figure 5 shows the changes in excess air ratios when IVC is delayed at a load factor of 25%. According to Fig. 5, it was found that there is an IVC timing at which the excess air ratio is highest, and the maximum amount of air can be supplied into the cylinder by setting the IVC to the maximum excess air ratio at a load factor of 25%.
During development of the 25AHX engine, 1D cycle simulation was conducted to determine parameters required to achieve target performance such as engine specifications, fuel injection characteristics, fuel injection start timing, intake valve open and close timings, and compression ratio. Also the specifications of engine components and equipment were determined, and a test machine was built. At the same time, test parts such as the camshaft and fuel injection system needed for adjusting the performance of the test machine were prepared and performance tests were conducted. We optimized the final engine specifications to meet the requirements in the IMO Tier II by adjusting the compression ratio, IVC, fuel injection start timing, and turbocharger matching using the test machine.
Figure 6 shows the relationship between fuel consumption by two engines (the 25AHX with IMO Tier II specifications and a conventional engine) and CO₂ emissions generated through combustion. Figure 7 shows the comparison of engine performance in a test cycle E3 mode (marine characteristics) between the 25AHX with IMO Tier II specifications and a conventional engine. The comparison shown in Fig. 7 is a relative comparison based on the performance value of a conventional engine at rated output.
According to Fig. 6, fuel consumption and CO₂ emissions are in a proportional relationship, and the proportional inclinations are almost identical regardless of engine type. This suggests that CO₂ emissions per kilogram of fuel are constant regardless of engine type, and that amounts of CO₂ reduction can be known once fuel reduction amounts are obtained. Also, according to Fig. 7, the 25AHX features improvements in fuel consumption with respect to all load factors compared to a conventional engine. In terms of fuel consumption and CO₂ emissions, the 25AHX shows improvements of approximately 7% at the rated output (1 500 kW) and 15% at a load factor of 25%, compared to a conventional engine. When compared with engines that have identical net mean effective pressure (Pme) as of 2020, this fuel consumption performance is one of the best in the world.
In addition, the 25AHX shows significant improvement in the emissions of air pollutants such as total hydrocarbon (THC). This is because, firstly, the 25AHX has a higher compression ratio than conventional engines and secondly, the VIVT mechanism can avoid the situation where the engine undergoes a shortage in air when the load is too low to operate a turbocharger and can maximize volumetric efficiency when an intake valve is opened or closed. This enables the 25AHX to be supplied with sufficient air even when the engine load is low.
When the engine load is high, a turbocharger supplies the 25AHX with sufficient air.
Thus, the 25AHX can increase combustion efficiency at all load ranges and achieve a favorable combustion state with low fuel consumption, similar to the 28AHX.
3.4 Measures to meet the regulations for marine engine emissions applicable to Chinese domestic vessels
As a mentioned above, CHINA II(1), the Chinese regulation for marine engine emissions (GB15097-2016), is stricter than the IMO Tier II. It is a different system from the IMO emission limits. That is, it stipulates the emission limits based on engine output and cylinder displacement, covers not only NOx, but also other exhaust gas compositions like carbon monoxide (CO), THC, and particulate matter (PM).
The 25AHX engine has a rated output of 1 500 kW and a volumetric displacement per cylinder of 18.2 L, so the CHINA II emission limit of 7 kg/kWh for NOx and THC combined is applied for it. To meet this emission limit, it is necessary to reduce the NOx emission rate by nearly 30% compared to the IMO Tier II specification. Figure 8 shows a comparison of ship exhaust regulations (NOx and THC) in domestic Chinese shipping and IMO NOx regulations.
It is possible to reduce NOx emission rate by 30% to meet the CHINA II regulation with a post-processing device such as a selective catalytic reduction (SCR). However, considering the adverse impact on cargo holds (reduction in transport volumes and need to enlarge vessels’ hulls) and the use of reducing agents, adoption of a post-processing device may carry the risk of increasing the burden on customers and environmental loads. Thus, while developing the 25AHX to meet the CHINA II regulation, we achieved an additional 30% reduction in the NOx emission rate without using a post-processing device. This was done through improving combustion in the engine body by minimizing the increase in fuel consumption arising from NOx emission reduction.
3.5 NOx reduction methods
Compliance of the 25AHX for the NOx emission limit in the CHINA II regulation was evaluated with the NOx emission rate (g/kWh) through the test cycle, as was the case with the evaluation for the IMO NOx emission limit. Table 2 shows the weighting factors used for evaluating the NOx emission rate of propulsion engines (E3 mode) according to the propeller law. In both IMO Tier II and CHINA II, weighting factors have been set for each of four load factors to evaluate NOx emission rates. The weighting factors for load factors of 75% and 100% are 0.50 and 0.20, respectively, which are larger than the other weighting factors. Thus, it is effective to meet the emission limits by reducing NOx emissions in the high-load range.
What follows describes the details of delaying the fuel injection start timing and advancing IVC as effective ways to cut NOx emissions.
3.5.1 Delaying fuel injection start timing
To investigate the changes in fuel consumption and NOx emissions along with the changes in fuel injection start timing, a test was conducted to measure NOx emissions with fuel injection start timing delayed by 3.5° and 7.1° from that in the specifications to comply with IMO Tier II. This test was done under four load factors, from 25% to 100%. Figure 9 shows the comparison of mean in-cylinder gas temperature curves with different fuel injection start timings at respective load factors. Also, Fig. 10 shows a comparison of in-cylinder pressure curves with different fuel injection start timings under the respective load factors. The fuel injection start timings in these figures are based on the specifications to comply with IMO Tier II.
Figure 9 confirms that at all load factors, the more the fuel injection start timing is delayed, the lower the mean cylinder gas temperature (combustion temperature) in the range from top dead center, where NOx is generated, to 30° after top dead center. This is considered to have caused a significant change in the combustion state in a cylinder. Actually, as Fig. 11 indicates, delaying the fuel injection start timing caused a reduction in NOx emissions but an increase in fuel consumption. In particular, we confirmed that delaying the fuel injection start timing by 7.1° from the reference point caused the reduction in NOx emissions by 30% and thereby meeting the emission limit of CHINA II regulation. However, it caused an increase in fuel consumption by approximately 7% at a load factor of 100%. As Fig. 10 shows, the combustion state when the fuel injection start timing is the most delayed is that there is no abrupt pressure increase from the top dead center (crank angle of 0°), and the combustion state is similar to isobaric combustion. Pmax has also reduced, and the combustion period has been extended, resulting in an increase in fuel consumption. Such a combustion state is not considered ideal for an engine.
From these results, delaying the fuel injection start timing can reduce NOx emissions. However, considering the increase in fuel consumption, it is not a satisfactory NOx emission reduction method by simply delaying the injection start timing.
3.5.2 Advancing IVC (Miller cycle)
As described in Subsection 3.5.1, delaying the fuel injection start timing also can reduce NOx emissions but this alone cannot help to achieve optimal engine performance from the viewpoint of fuel consumption. To slightly enhance the effect of the Miller cycle through advancing IVC, a test was conducted to measure NOx emissions when IVC on the high load side was advanced by 3° from that in the specifications of IMO Tier II at load factors of 75% and 100%.
Figure 12 shows the mean in-cylinder gas temperature curves obtained through this test. According to Fig. 12, when IVC is advanced for both load factors, enhancement of the Miller cycle effect can be confirmed through the fact: decrease in compression temperatures at the compression finish time close to the top dead center; and also decrease in combustion temperatures. As Fig. 13 shows, advancing IVC reduced NOx emissions but increased fuel consumption. Figures 11 and 13 show there is a trade-off relationship between reducing fuel consumption and cutting NOx generation, in that both delaying the fuel injection start timing and advancing IVC have the effect of reducing NOx emissions but result in higher fuel consumption. Figure 14 shows the effects of delaying the fuel injection start timing and advancing IVC at a load factor of 100% on NOx emissions and fuel consumption. According to Fig. 14, when reducing an identical amount of NOx, it is clear that advancing IVC results in a lower increase in fuel consumption than does delaying the fuel injection start timing. Based on these results, the fuel injection start timing was set so as to meet the NOx emission limit through preferential advancement of IVC within a range where IVC operates.
Furthermore, the VIVT mechanism was used for shifting the intake valve timing when the load was low, at a load factor of 25%, to reduce fuel consumption and CO₂ as well as THC emissions. As a result, combined emissions of NOx and THC were 6.6 g/kWh, and CO and PM emissions also met the CHINA II regulation values. Figure 15 shows performance curves of the 25AHX with the specifications complying with CHINA II and a comparison with conventional engine. As shown in Fig. 15, the 25AHX with CHINA II specifications has improved performance in all load ranges compared to conventional engine. For example, there are approximately 3% and 15% reductions in fuel consumption at the rated output and under a load factor of 25%, respectively, as well as lower PM emissions in all load ranges. As for boost pressure, because we have adopted the Miller cycle and a high-pressure turbocharger for the 25AHX, this engine has higher boost pressure than conventional engine for which the Miller cycle is not adopted.
4. Evaluation of the 25AHX’s effects on fuel consumption and CO₂ reduction
Expected applications of the 25AHX are as a marine engine for tugboats in particular. Therefore, we analyzed the navigation data of tugboats operating in Tokyo Bay for three months from July to September 2021, and based on the results of investigating the navigation time by load factor, we estimated the 25AHX’s fuel consumption and CO₂ reduction effect during actual operation. According to Fig. 16, which shows the percentage of navigation time of the surveyed tugboats by load factor, navigation at load factors of 25% or less accounts for approximately 80% of the total navigation time. Using this result and the fuel consumption of the 25AHX at the load factors shown in Figs. 7 and 15, we calculated the fuel consumption to be used iN₂ 000 hours navigation per year for three cases: the 25AHX with IMO Tier II specifications, the 25AHX with CHINA II specifications, and a conventional engine with IMO Tier II specifications. The calculated results and comparisons for the three cases are shown in Fig. 17. As a result, when the 25AHX engine is installed on a tugboat, the 25AHX with the IMO Tier II specifications reduces fuel consumption and CO₂ by 12% per year compared to conventional engine, and the 25AHX with the CHINA II specifications reduces NOx emission levels by approximately 30% compared to conventional engine. Accordingly, it is expected that the 25AHX can reduce fuel consumption and CO₂ emissions by approximately 10% annually and help customers to reduce running costs, as well as aid them in taking measures against global warming through cutting CO₂ emissions.
5. Evaluation of the 25AHX for commercialization (reliability enhancement)
As shown in Fig. 15, the 25AHX with CHINA II specifications tends to have a higher exhaust temperature than conventional engines. Thus, there was concern that that 25AHX might undergo thermal deformation of the cylinder head or exhaust manifold due to the high temperature. To cope with this concern, we have taken measures to improve the soundness of these components by preliminarily studying and adopting optimal shapes based on checking the temperatures to which these components would be exposed through computational fluid dynamics (CFD) and the finite element method (FEM). In particular, a water-cooled exhaust manifold is adopted for the 25AHX because the cylinder head’s exhaust port is subject to high temperature. The effect of installing this water-cooled exhaust manifold on the 25AHX is confirmed to be able to cool the cylinder head down tO₂20°C, a temperature level equivalent to that in a conventional engine with proven performance. This fact was demonstrated through the measurement of temperatures on the cylinder head as shown in Fig. 18.
We have advanced the 25AHX’s degree of completion through several product development verification tests, including durability testing. Figure 19 shows an example of monitoring the 25AHX’s performance during a durability test. The test was conducted efficiently using automatic measurement and state monitoring.
6. Conclusion
The 25AHX engine utilizes the technologies that reduce fuel consumption and NOx emissions acquired through the developing the AHX series of engines, achieving world-class fuel consumption performance and successfully satisfying the CHINA II regulations, which are stricter than the IMO Tier II regulations. This paper introduced the technical findings with respect to CO₂ and NOx reduction through lowering fuel consumption in the course of developing the 25AHX. With its established performance using these technical findings, the 25AHX can be considered as an engine with significantly improved fuel consumption not only at rated output but also at low loads in particular, and as an engine expected to reduce CO₂ emissions in actual commercial operations.
The 25AHX engine has been on sale from April 2022 and the 25AHX with CHINA II specifications (introduced in this paper) acquired CHINA II certification from the China Classification Society (CCS) in July 2022. Since then, there have been many inquiries from prospective customers.
Currently, in order to cut CO₂ emissions, organizations in various industrial fields have promoted research and development of alternative fuels, including carbon-neutral fuel like biofuel and carbon-free fuels like ammonia (NH₃) and hydrogen (H₂). IPS has also promoted research and development of an ammonia-fueled engine. Because the 25AHX is an engine with great potential for enhancing environmental performance, including prevention of global warming, IPS will continue improving the 25AHX to make it compatible with such alternative fuels. IPS will work to reduce global environmental loads through providing AHX-series engines, including the 25AHX, to as many customers as possible for various applications, and to improve the performance of the AHX series. This will contribute to activities that sustainably improve the global environment.
REFERENCES
(1) GB15097-2016:Limits and measurement methods for exhaust pollutants from marine engines (CHINA I,II)
(2) H. Nagasawa, K. Imai, H. Yamamoto, S. Kato and K. Sonobe : 28AHX: Next-Generation Medium Speed Diesel Engine Designed to Comply with Environmental Regulations, Journal of IHI Technologies, Vol. 50, No. 3, 2010, pp. 84-87 (in Japanese)
(3) M. Kawakami et al.:Investigation on reducing NOx emission of medium-speed diesel engine,18th CIMAC World Congress,(1989),Paper No. D27