Hydrogen Production by Thermal Decomposition of Natural Gas
ITO Takamasa, MIYAURA Takuto
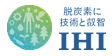
ITO Takamasa : Doctor of Engineering, Manager, Energy Conversion Group, Technology Platform Center, Technology & Intelligence Integration
MIYAURA Takuto : Energy Conversion Group, Technology Platform Center, Technology & Intelligence Integration
This paper introduces new technology related to hydrogen production by thermal decomposition of natural gas. This technology needs less energy to produce hydrogen than the other conventional technologies. And the carbon derived from natural gas is collected in solid phase after decomposition. This technology is expected to produce hydrogen in low cost with low carbon dioxide (CO₂) emissions. There are a variety of systems proposed, depending on the heating system, sort of catalyst and handling of the collected carbon. IHI has developed the original system which consists of the fluidized bed with iron ore as catalyst. This paper introduces the development of this technology and plan for its commercialization.
1. Introduction
The more widespread use of hydrogen is expected to establish a decarbonized society. Currently, steam reforming of natural gas is recognized as the main technology for hydrogen production, but because this technology generates carbon dioxide (CO₂) through the process as a by-product, the CO₂ collection, storage, and utilization are needed not to release CO₂ into the atmosphere. In contrast, water electrolysis is an ideal technology to produce hydrogen in terms of no CO₂ emissions. However, water electrolysis consumes a lot of energy to produce hydrogen, and it will take time to cover the energy source for this technology by renewable energy. For these reasons, IHI has developed new technology for hydrogen production based on thermal decomposition of natural gas. This technology uses a small amount of renewable energy and catalysts to ensure cost-effectiveness and minimize CO₂ emissions. This paper firstly introduces general technologies concerning hydrogen production, then precisely explains the characteristics of the thermal decomposition of natural gas developed by IHI, and finally mentions the prospect for commercialization of this technology.
2. Technologies for hydrogen production
2.1 General technologies of hydrogen production
Table 1 shows the general technologies of hydrogen production. Steam reforming of natural gas produces hydrogen by mixing natural gas with steam at high temperature. Currently, this technology is common in society, and the produced hydrogen is used in a variety of fields, including industries, medical care, etc. However, it has the disadvantage of CO₂ emissions during the process and faces the necessity to reduce such emissions. The method to reduce CO₂ generated through the process is mainly collection, storage, or utilization of CO₂. In recent years, CertifHy™(1), a project proposing hydrogen standards in Europe, defines hydrogen produced with CO₂ emissions of 36.4 g-CO₂/MJH2 (equivalent to 4.4 kg-CO₂/kg-H₂) or less as the low-carbon hydrogen. Several systems related for subsidies such as tax deductions based on this value are under establishment.
Water electrolysis is a technology to produce hydrogen by electrochemically decomposing water into hydrogen and oxygen with a certain voltage applied to water. There are no CO₂ emissions according to the thermochemical equation, which means that the technology is ideal in terms of zero CO₂ emissions if the electricity is from renewable sources. However, since this technology requires more energy to produce a certain amount of hydrogen than other technologies, a stable supply of renewable energy is essential.
The thermal decomposition of natural gas is a technology that thermally decomposes natural gas into hydrogen and solid carbon. Because this technology requires quite a low energy input of 38 kJ/mol-H₂ to produce 1 mol of hydrogen, it can theoretically generate about six times more energy in the form of hydrogen than input energy. Also, whereas steam reforming unavoidably introduces CO₂ at a molar ratio of 1/5 in produced gas, the thermal decomposition of natural gas enables carbon to be collected in a solid form. Consequently, the thermal decomposition of natural gas is anticipated to yield highly concentrated hydrogen.
2.2 Thermal decomposition of natural gas
Several systems have been proposed for the thermal decomposition of natural gas, differing with respect to heating methods, types of catalysts, and the utilization of co-produced carbon. This section introduces the systems proposed by some companies as shown in Table 2.
Company A’s system generates a high-temperature field at least 1 500°C using plasma produced with electricity derived from renewable sources to decompose natural gas without the use of catalysts. After the decomposition, carbon nanometer-scale particulates are suspended in the air as agglomerates. These particulates are collected and commercialized as carbon black. Company A has reduced CO₂ emissions by changing heat sources from conventional fossil fuel to renewable energy. The important point of this system is that the amount of hydrogen production is restricted by the market size for carbon black. The global market for carbon black is in the tens of millions of metric tons per year, but the production of hydrogen calculated based on the market size of carbon black is at most several million t/y. This amount of hydrogen is quite tiny as the energy source in the future. In addition, this type of business requires experience in distributing carbon black.
Company B’s system uses molten metal (tin) as a catalyst to accelerate the thermal decomposition of natural gas. The thermal decomposition occurs when the gas passes through the molten tin that is heated with an electric heater. Solid carbon is generated during the thermal decomposition and suspended on the surface of the molten metal as slag because the specific gravity of carbon is lower than that of the molten metal. Highly concentrated hydrogen can be continuously generated with discharging the slag of carbon.
In Company C’s system, a part of the heat required for thermal decomposition is supplied by the produced hydrogen. By combusting the produced hydrogen to supply heat, the system can reduce CO₂ emissions by approximately 90% compared to those from steam reforming.
Company D’s system utilizes iron ore as a catalyst and collects carbon deposited on the surface of the iron ore. This carbon has a potential to be material for batteries. However, carbon for batteries must be at a high level of purity, so the residual catalyst in the carbon particulates needs to be eliminated by acid dissolution, etc.
IHI’s thermal decomposition system utilizes granular iron ore as a catalyst and incorporates fluidized-bed technology, of which IHI has accumulated abundant knowledge, for handling particles of iron ore. The goal of the system is to continuously produce hydrogen whose concentration is maintained to be more than 90% by the appropriate handling of the catalyst and gas. The carbon discharged from this system has already been confirmed as environmentally harmless. And this carbon is investigated to be utilized for improving the quality of water and reforming soil.
As explained above, there are several systems proposed, which differ according to heating methods, catalysts, and utilization of collected carbon. The common issue to these systems is the utilization of the carbon that is co-produced in amounts three times greater than the produced hydrogen. In order to commercialize these systems, it is important to find the right balance in market size between the target hydrogen and carbon.
3. Hydrogen production by IHI’s thermal decomposition system
IHI has been developing a thermal decomposition system for natural gas. The target production volume for a single unit is up to 100 t/d of hydrogen. This production volume is similar with that of the steam reforming system that is recognized as the major technology for hydrogen mass production today.
Figure 1 shows an outline of the system. To achieve a daily hydrogen production of 100 t, the system requires 400 t/d of natural gas and 140 t/d of iron ore as a catalyst. Iron exists in iron ore mainly as an iron oxide called hematite (Fe₂O₃). Therefore, the iron ore input into the system is initially reduced to iron (Fe) upon contact with natural gas and subsequently functions as a catalyst. A small amount of CO₂ is generated during the reduction process, but this quantity can be suppressed to approximately 1/10 of that produced through steam reforming. After the thermal decomposition, hydrogen is collected and post-processed as needed and carbon is deposited on the surface of the catalyst and discharged as a mixture with iron. The energy required for these reactions is approximately 480 MWh/d, which is roughly 1/7 of the electric power required for water electrolysis. These values are references only and vary according to the composition of the iron ore. Detailed descriptions of the iron ore, hydrogen, and carbon are as below.
3.1 Iron ore
As a catalyst for thermal decomposition, this system uses iron ore which is generally distributed throughout the iron and steel industry. The main component of the iron ore is hematite. Table 3 shows the composition of the iron ore used in the fundamental experiment conducted by IHI. The iron ore has an iron content of slightly less than 70 wt% and is granular in shape. According to a report(2) published by the Australian government, iron ore distributed throughout the global market ranges widely in size, ranging from powders with diameters in the order of a few hundred microns to lumps with diameters in the order of a few centimeters, with an iron content of approximately 60 wt% from an economic perspective.
The advantages of using iron ore are mainly the following two. Firstly, a substantial quantity of 2.5 billion t(2) is distributed annually to the market by many suppliers. This increases the freedom of choice in selecting procurement sources. Secondly, the procurement cost (free on board) is quite low as a catalyst, at around 100 US$/t(3). It supports to keep the unit cost of hydrogen production moderate.
3.2 Hydrogen concentration
Figure 2 shows the chronological changes in the composition of the gas produced by the thermal decomposition of methane at high temperature. This figure represents the results of the whole processes in the fundamental experiment, including the activation and deactivation of the catalyst. In the figure, the hydrogen (H₂) concentration gradually increases and peaks at around 90 vol%. After certain period, the concentration of hydrogen decreases gradually again. During the initial stage of the experiment, the produced gas contains carbon monoxide (CO) and CO₂ because hematite, the main component of iron ore, is reduced with methane. After the reduction of iron ore, the produced gas mainly consists of hydrogen and unreacted methane. Comparing the areas of H₂, CO, and CO₂ on the graph, it is clear that the produced amounts of CO and CO₂ are much smaller than that of H₂.
As Table 1 indicates, the hydrogen concentration derived from steam reforming is at most around 80 vol% due to the cogeneration of CO₂ with H₂ in the produced gas. But because of the capability to collect carbon as a solid, IHI’s thermal decomposition system of natural gas can achieve a higher hydrogen concentration. Currently, IHI is working
on further improving the hydrogen concentration by appropriately controlling the residence time of gas and particles in the furnace. Increasing the hydrogen concentration in the produced gas is expected to reduce hydrogen production costs by decreasing the load of the gas separation process.
3.3 Solid carbon
Figure 3 shows appearance of the iron ore and carbon collected after the experiment. The volume of the collected carbon is approximately seven times greater than that of iron ore before the reaction. This means that the diameter of iron ore has been increased due to the carbon deposited on them. The surfaces of the grains are dry and they are easy to handle during transportation.
Figure 4 is an electron micrograph showing an enlarged view of carbon particles. The white dots are iron components, and the other gray particles are carbon. This image clearly shows that spherical carbon particles deposit on the core of iron in conjunction with one another. To check the environmental safety of blending these particles into soil, an analysis was conducted in accordance with JIS K 0102 “Testing methods for industrial water and industrial wastewater” with reference to the “Environmental Quality Standards for Soil Pollution” (the Public Notice of the Ministry of the Environment No. 46). The results of analysis are presented in Table 4. The values of the respective items in the results were lower than the thresholds of the Environmental Quality Standards for Soil Pollution, confirming that these particles are environmentally safe. Currently, we are working on applying particles to soil reforming, water improvement, etc.
4. Commercialization of hydrogen production technology by thermal decomposition of natural gas
Figure 5 shows the schedule for commercialization of this technology. We aim to commercialize this technology in the latter half of the 2020s. Currently, to maximize the hydrogen concentration in the produced gas, a prototype model has been in operation since December 2023. The production capacity of this prototype model is around 10 kg-H₂/d. Figure 6 gives an illustration of the prototype model. This prototype model comprises a feeder for the gas, a furnace for the thermal decomposition, and a furnace for the combustion of the produced gas. In addition to maximization of the hydrogen concentration in the produced gas in the future, we will evaluate the durability of the furnace through long-term operation, as well as the purification of the produced hydrogen to suit the specification of the certain usage.
This technology relies on using natural gas and iron ore. Therefore, we plan to commercialize this technology in the countries where these resources are available. One of the candidate countries is the United States, where a tax credit system for clean hydrogen production has been introduced based on the Inflation Reduction Act enacted in August 2022. This tax credit system allows for tax deductions of up to 3 US$/kg-H₂ of hydrogen produced depending on the amount of CO₂ emissions. Figure 7 shows the tax credit based on CO₂ emissions. To qualify for this tax credit system, CO₂ emissions must not be greater than 4.0 kg-CO₂/kg-H₂. This threshold has been considered to be difficult for the conventional steam reforming with natural gas. In contrast, IHI’s thermal decomposition system introduced in this paper can significantly reduce CO₂ emissions to approximately 1/10 of that with conventional steam reforming, so it is expected to qualify the criteria of this tax credit system.
5. Conclusion
This paper introduces the technology for producing hydrogen by the thermal decomposition of natural gas. This technology utilizes granular iron ore as a catalyst and incorporates fluidized-bed technology, of which IHI has accumulated abundant knowledge, to handle solid particles. Although this method produces hydrogen using natural gas as a raw material, it requires less energy to decompose the natural gas than conventional technologies. This is expected to reduce the unit cost and carbon intensity of hydrogen production. Recognizing that this technology represents a significant step in contributing to the spread of hydrogen into society amid the transition from fossil fuel to renewable energy, we will continue going forward to commercialize it.
REFERENCES
(1) CertifHy™:https://www.certifhy.eu, accessed 2023-10-24
(2) D. Summerfield : Australian Resource Reviews Iron Ore 2019, Geoscience Australia, 2020
(3)Nihon Keizai Shimbun (nikkei.com) : Iron ore price fell 4 points due to sluggish global steel demand. Procurement trends for blast furnace steel manufacturers in the quarter of July to September, June 8, 2023, https://www.nikkei.com/article/DGXZQOUB080 TG0Y3A600C2000000/,accessed 2023-06-09 (in Japanese)