Development and Commercialization of Twin Roll Strip Caster
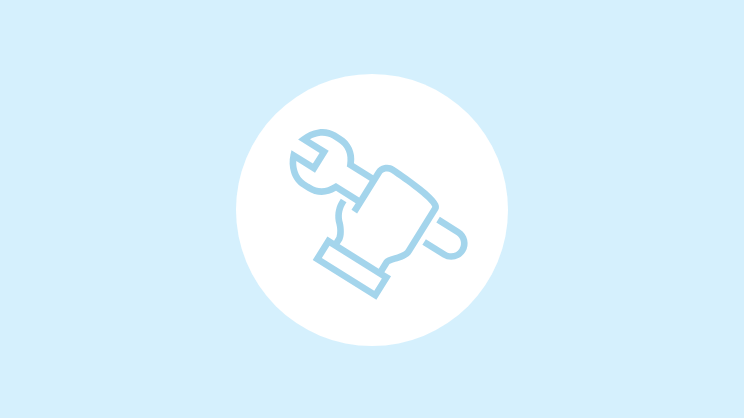
Development and Commercialization of Twin Roll Strip Caster
- MATSUSHITA Toshirou, NAKAYAMA Katsumi, FUKASE Hisahiko, OSADA Shirou
IHI started development of the strip caster in 1982, and successfully achieved continuous casting by a laboratory caster, which was then expanded to collaboration with BHP (currently BSL) of Australia in 1989. The pilot plant for 5-ton melt was constructed and succeeded in casting. Next, a commercial scale demonstration plant for 60-ton melt was built in 1994, which progressed well. For further development, Nucor of the USA joined with IHI and BSL in 2000 and established a joint corporation, Castrip LLC. The first commercial facility was constructed at the Crawfordsville Steel Works of Nucor and has produced 650 000 tons of low carbon steel strips as of 2007 since the start-up in 2002. Ultra thin Cast steel Strips (UCS, 0.85 to 1.5 mm thick) produced by the caster are now selling well in the market of those from the conventional hot/cold strip rolling mills. IHI has received an order for a second commercial facility to be operated in early 2009. Furthermore, the strip caster has the potential to achieve the dream of competitiveness in producing value-added products that cannot be achieved by the conventional slab casting & rolling processes.