Intangible Asset1
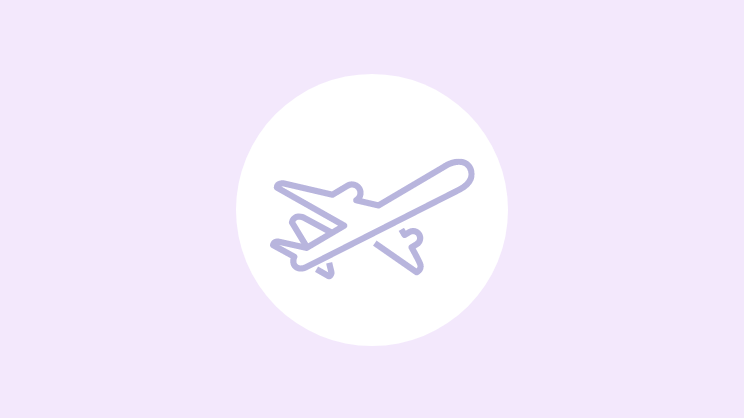
People Who Lead Our Jet Engine Factories to Realize Your Dreams
- IHI Corporation
Change
Location
Currently Using The English Site.
Regional HQ’s Websites
Other
1. Intangible Asset
Intangible Asset1:
People Who Lead Our Jet Engine Factories to Realize Your Dreams
Intangible Asset2:
Designing a Variety of Jet Engine Shafts with Deep Expertise in the Manufacturing Line - A Key Person in Engine Shaft Manufacturing -
Intangible Asset3:
Building the Technology and Production Lines to Precisely Mass-Produce Blades with Complex Shapes - A Key Person in Electrical Machining -
Intangible Asset4:
Family Doctor Who Performs His Check Ups on Jet Engines - A Key Person in Maintenance Engineering -
2. Technologies
Technologies1:
Making Lighter Aircraft Engines with Titanium Aluminide Blades The current state of net shape casting
Technologies2:
IHI's Unique Technology Behind Jet Engines Automated shaft coating
3. Business
4. Essay
Essay1:
Where Does the Sound TOKU-TOKU Come from?
5. Technical Papers
Technical Papers1:
Development of PW1100G-JM Turbofan Engine
Technical Papers2:
Development of CMC Turbine Parts for Aero Engines
Technical Papers3:
Moving to an All-Electric Aircraft System
Technical Papers4:
Application of Linear Friction Welding Technique to Aircraft Engine Parts
Technical Papers5:
Development of Metal Injection Molding Process for Aircraft Engine Part Production
Technical Papers6:
Research and Development of a High Performance Axial Compressor
Technical Papers7:
Development of Composite Fan System
People Who Lead Our Jet Engine Factories to Realize Your Dreams
Designing a Variety of Jet Engine Shafts with Deep Expertise in the Manufacturing Line - A Key Person in Engine Shaft Manufacturing -
The Kure Aero-Engine & Turbo Machinery Works manufactures 70-80% of the world's long shafts used in jet engines. The key person who manages the design and execution of the manufacturing line has to create a manufacturing setup that can cater to the advanced demands of global customers, while also remaining sensitive to local needs. His role is like that of an orchestra conductor.
Building the Technology and Production Lines to Precisely Mass-Produce Blades with Complex Shapes - A Key Person in Electrical Machining -
In order to improve jet engine efficiency, a large number of complexly shaped blades are indispensable. This article spotlights a key person who is very familiar with a broad range of electrical machining technologies used to efficiently and precisely machine these blades, and who oversees the building of production lines and the development of processing technologies.
Family Doctor Who Performs His Check Ups on Jet Engines - A Key Person in Maintenance Engineering -
All new jet engines and those after maintenance are required to be tested before delivery to verify their performance. Mizuho Aero-Engine Works, which handles the maintenance of jet engines, has twelve testing facilities (test cells). The key person who took part in the start-up of the latest test cell and manages all of its operations is just like a family doctor for jet engines.
Making Lighter Aircraft Engines with Titanium Aluminide Blades The current state of net shape casting
Titanium aluminide is a new material that will lead to much lighter aircraft engines, and thus lighter aircraft. Net shape precision casting is the latest development in the ancient technique of casting, and is used to mass-produce hundreds of turbine blades accurately and at low cost. By also applying a revolutionary melting technology, the mass production of titanium aluminide blades becomes possible.
IHI's Unique Technology Behind Jet Engines Automated shaft coating
In the past, jet engine shafts have been manually coated by skilled workers. In the midst of the current situation in which it is difficult to secure skilled workers, we have put an automated coating system for engine shafts into practical use for the first time in the world. The result has been improved coating quality as well as the establishment of a system to cope with a future increase in demand.
Learning from Disaster: The First Step Toward a World-Class Soma Works Utilizing renewable energy to turn Soma into a world-class facility
The Soma Works recovered from the Tohoku Earthquake and tsunami and resumed production with extraordinary speed. Now, the facility is transitioning from a disaster recovery phase to an expansion phase, and a variety of lessons learned from the disaster are being implemented. The first major actions are Business Continuity Planning (BCP) and the photovoltaic (PV) solar power generation system introduced as a power-saving measure. This involves a new model of renewable energy utilization.
Where Does the Sound TOKU-TOKU Come from?
Development of PW1100G-JM Turbofan Engine
The PW1100G-JM is one of the next-generation turbofan engines selected to power the Airbus A320neo (New Engine Option). IHI participated in the PW1100G-JM program as a member company of the Japanese Aero Engines Corporation (JAEC). The PW1100G-JM adopts the Geared Turbo Fan (GTF) system and delivers improvements in fuel efficiency, emissions, and noise by applying state-of-the-art composite materials and component technologies. This paper presents an overview of the PW1100G-JM.
Development of CMC Turbine Parts for Aero Engines
Recently, oil prices have risen creating a need for fuel-efficient aero-engines. New materials that have low density and the ability to withstand high temperatures will contribute to improving fuel-efficiency. Ceramics have such properties but their brittleness limits their fields of application. Ceramic Matrix Composites (CMC) - ceramics reinforced with fibers - can solve this issue, and are being developed as next-generation materials for aero-engines. CMCs have been under development for more than 20 years, and will be applied to commercial fields in the near future. IHI has been working on the development of CMCs, mainly for use in turbine nozzles and blades. Through these studies, good results were obtained from spin tests and fatigue tests carried out for prototype components.
Moving to an All-Electric Aircraft System
The More Electric Architecture for Aircraft and Propulsion (MEAAP) project aims to improve safety, environmental friendliness, and economic benefits with innovations that integrate electrical power management and thermal management for aircraft. IHI is trying to develop an all-electric system for the engine and aircraft of the future within the next decade or two. This paper introduces an overview of the MEAAP concept and IHI all-electrical system innovations.
Application of Linear Friction Welding Technique to Aircraft Engine Parts
In recent aircraft engines, the application of blisks in fan and compressor rotors is increasing to achieve weight reduction and performance improvement. The conventional manufacturing method of blisks is to machine them from a forged material. But with this method, the loss of material is relatively large. Therefore a manufacturing method in which blades are joined to disks with Linear Friction Welding (LFW) is being developed. LFW is a kind of solid state welding technique in which the weld surfaces are rubbed together to cause them to heat up. In the current study, the changes in the micro structure, the structural integrity of the LFW joint, and the results of the manufacturing trial of the compressor blisk are reported.
Development of Metal Injection Molding Process for Aircraft Engine Part Production
Metal Injection Molding (MIM) is a net-shape process for producing metal parts that combines the design freedom of plastic injection molding with material strength near that of wrought metal. IHI has been developing the MIM process for low-cost manufacture of high pressure compressor vanes which are used in aircraft gas-turbine engines. Material tests have been carried out on the vanes and the test results show good performance. Measurement of the dimensional precision of the prototype compressor vane has shown promising results. This paper describes the status of MIM process development at IHI.
Research and Development of a High Performance Axial Compressor
Higher efficiency and higher pressure ratios are required for compressors of aircraft turbo-fan engines in order to achieve a fuel burn reduction. In addition, technical issues related to a smaller core size must be overcome to realize a higher overall pressure ratio and higher bypass ratio of an engine. This paper summarizes the development of axial compressor aerodynamic design technologies that address these subjects, including validation through rig testing. The development of some key structural design technologies to realize the original intent of an aerodynamic design is also described, including higher accuracy variable stator vane actuation, tip clearance reduction, and blade forced response prediction.
Development of Composite Fan System
The Composite Fan System R&D Project was created to develop composite structural parts for the fans used in next-generation commercial aero-engines. The technology developed for the composite fan case and composite structural guide vane has been completed and demonstrated. These two parts will be applied to the PW1100G-JM, which powers the Airbus A320neo. This paper gives an outline of the development of the composite fan case and composite SGV.