First Environmentally Friendly Next-Generation Electric Propulsion Ship System in Japan
System integration enabling to reduce CO2 emissions by 30%
IHI Power Systems Co., Ltd.
IHI Power Systems Co., Ltd. has succeeded in significantly reducing carbon dioxide (CO₂) emissions compared with conventional ships by adopting the DC (direct current) voltage grid system for the series hybrid. The series hybrid uses electric motors for propulsion and a combination of batteries and generators for electricity.

Realization of carbon neutrality by 2050 and a growth strategy for the ship industry
In October 2020, the Japanese government declared that Japan would achieve carbon neutrality by 2050 and announced that we have entered an era in which responding to global warming is viewed as an opportunity for global growth, rather than as a constraint or cost on economic growth.
Furthermore, following this declaration, the Ministry of Economy, Trade and Industry announced the Green Growth Strategy in June 2021. This Green Growth Strategy set ambitious goals to achieve net zero GHG (greenhouse gas) emissions in promising industries (14 fields) as an industrial policy to create a virtuous circle of economy and environment.
In this strategy, fuel cell ships, electric propulsion ships, and gas fuel ships are said to be effective in reducing carbon dioxide (CO₂) emissions in the ship industry. IHI Power Systems Co., Ltd. (IPS) especially strives to spread electric propulsion ships with the electrified power system and gas fuel ships as part of its sustainable growth strategy.
IPS focuses on electric propulsion ships because domestic vessels, where IPS holds an advantage, are well-suited for electric propulsion using batteries due to their short navigation distances. In addition, there have been advancements in efficiency improvement and price reduction of electric motors, along with the recent availability of high-function and high-efficiency inverters and electric equipment that drive these electric motors. This has resulted in easier system building and allowed for adoption in a wide range of ships. This is another reason why IPS focuses on electric propulsion ships.
Past electric propulsion ships IPS has been involved in
IPS is currently developing next-generation electric propulsion systems. This article first discusses electric propulsion ships using examples in which IPS was actually involved.
IPS has a strong track record and much experience delivering marine engines and propulsion systems. We also offer total packages that include remote control devices in addition to engines and propulsion systems. Among these propulsion systems, especially our azimuth thruster (Z-PELLER®) accounts for 90% of the Japanese market and 30% of the world market excluding Japan. We have delivered over 5 000 sets.
Among the electric propulsion ships in which IPS was involved in the past, this section introduces tugboats equipped with the Z-PELLER described above. The types of electric propulsion ships are listed in the table.
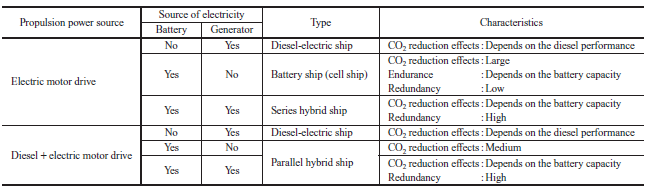
In March 2013, Tsubasa, the first parallel hybrid tugboat in Japan, went into service at Yokohama Port. Tsubasa is a parallel hybrid tugboat with a plug-in function that allows power to be supplied from land. This tugboat is equipped with lithium-ion cells as batteries for the first time as a domestic vessel.
In October 2013, Ginga, another tugboat of the same type was commissioned at Yokohama Port. However, Ginga is not equipped with batteries. This was the first diesel-electric tugboat in Japan that did not use batteries, which were expensive at the time.
Both of the ships have many transformer components due to the adoption of an AC voltage grid system. Although this made it challenging to install them into the limited ship space, IPS successfully achieved the expected operational and environmental performance.
IPS gained insights into integrating the power management system using diesel engines and electric motors for drive power through these two projects.
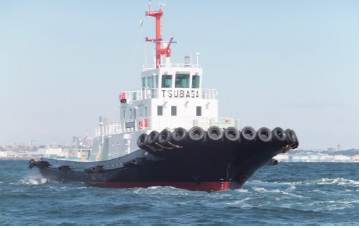
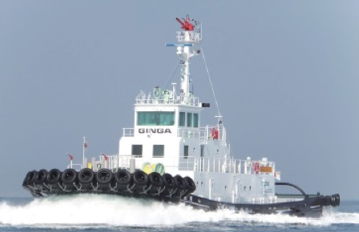
Next-generation electric propulsion ship, Taiga
A new type of electric propulsion tugboat named Taiga went into service in January 2023. IPS was involved in this tugboat as a system integrator and supplier of generator and propulsion system. This is an electric propulsion tugboat of the series hybrid type, which combines high-capacity lithium-ion cells and diesel generators. IPS reduced the emissions of CO₂, nitrogen oxides (NOx), and sulfur oxides (SOx) by about 30% compared to conventional diesel-driven ships by integrating the systems to manage power and power source. This tugboat not only reduces environmental load in this way but also mitigates noise and vibration, which is good for the crew’s work environment and the environment around ports.
Taiga adopted an L-Drive Z-PELLER equipped with electric motors, which IPS supplied for the first time, as its propulsion systems. The L-Drive Z-PELLER eliminates the need for the power transmission device from electric motors to propulsion systems. This results in certain advantages, specifically, a reduction in size and mechanical loss.
In addition, the electric propulsion systems have achieved higher efficiency than conventional ones by adopting the DC grid for the electric control system for the first time in Japan and combining it with high-capacity lithium-ion cells.
Next-generation electric propulsion ship, Asuka
A project started in order to adopt a 499 GT model coastal service electric propulsion ship for fuel transportation to Unit 2 of Aioi Power Plant (Aioi biomass power plant) of Aioi Bioenergy Corporation.
As a system integrator, IPS received an order for a set comprising the main power generation engine and electric system. The system is compact and highly efficient as ABB’s Onboard Microgrid, a DC grid system, and permanent magnet (PM) propulsion electric motors, etc. are used for system control.
Asuka is a series hybrid electric propulsion ship equipped with high-capacity batteries in addition to the compact main generators provided by IPS. Therefore, Asuka ensures the range and speed equal or superior to diesel-driven ships and provides zero emission operation in ports including arrival/departure and cargo handling with electricity supply from high-capacity batteries.
With these superior characteristics, it is planned to reduce CO₂ emissions during operation by up to 50% compared with conventional diesel-driven ships. The same type as Asuka is expected to be popular in the future as a next-generation coastal service electric propulsion ship.
Innovative technology — DC grid system
Taiga and Asuka are series hybrid electric propulsion ships that do not use diesel engines for drive power. In addition, they adopted a full-scale DC grid system, which is different from the AC grid or AC synchronous generator system for conventional electric propulsion ships. This DC grid system can be easily installed in small ships like domestic vessels whereas the conventional grid panel for electricity control was too large to be installed in the limited space on such ships.
The DC grid (colored part) shown in the DC grid reference diagram distributes electricity with DC voltage instead of AC voltage and therefore is a core system required in more efficient next-generation ships. The DC grid panel houses power converters such as an inverter/converter, breakers and other components. In addition, it is not necessary to synchronize each generator because induction generators are connected to the DC grid via a converter. Moreover, load sharing between these generators and batteries can be easily controlled by changing the voltage in the DC grid.
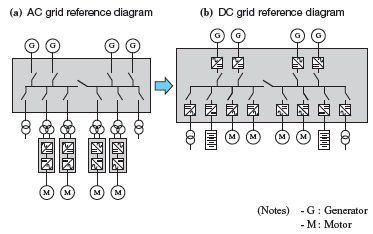
Furthermore, the battery system can be made more compact, as they can be linked with the DC grid via a DC/DC converter or through direct connection. The inverters, which convert DC voltage to AC voltage in the DC grid, can perform conversion into the variable frequency used in the AC electric motor for propulsion and the fixed frequency for inboard power, etc.
These functions and several hundred parameters are controlled and monitored on the upper level by a control system known as PEMS (power and energy management system). The knowledge of IPS on ship maneuvering control is incorporated into this system in the form of parameters.
Battery system
There are two methods to connect batteries: to the DC or AC grid. Since batteries use the direct-current based energy storage method, connection to the DC grid is simpler than connection to the AC grid.
The DC grid system generally requires fewer devices and can be more compact than the AC grid system. In comparison between these grid systems using a general-purpose converter that does not consider the short-circuit protection function and power supply/reception control, the total length of the grid panel for the AC converter system is twice that for the DC converter system. When the short-circuit protection function and power supply/reception control are considered, the total length of the grid panel for the AC converter system is nearly four times that for the DC converter system as shown in the diagram of battery connection methods.
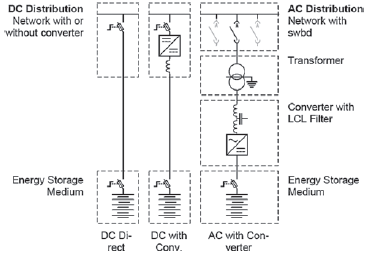
In the DC grid system, there are two methods to connect batteries to the DC grid: direct connection or via a DC/DC converter. Taiga uses the direct connection method. The direct connection method is advantageous for a ship with large output and battery capacity like Taiga as any battery can be shared. Asuka uses the converter method. The converter method is advantageous for a ship with small output and battery capacity like Asuka as the right and left batteries can be used independently.
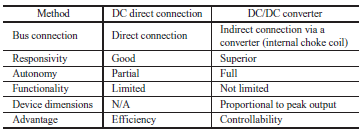
Future vision
IPS has received many inquiries about the next-generation electric propulsion system as it is suitable for the use of high-capacity batteries and is easier to install than conventional ones. Through the activities with the first ship, IPS acquired insights into size reduction using a cooling water system for the DC grid system, individual control through asynchronous electricity generation using the induction generator, and technologies introduced in this article. Among them, the logic for managing the power and power source using the PEMS and electromagnetic noise measures implemented on-site are particularly high-value technologies. We will contribute to the realization of a decarbonated society and carbon neutrality with these technologies related to next-generation electric propulsion ship systems.