火力発電ボイラにおけるメンテナンスや運転支援の取り組み 遠隔監視技術を活用した運転・保守支援システム “MEDICUS NAVI®” と新しい検査・評価技術
遠隔監視技術を活用した運転・保守支援システム“MEDICUS NAVI”は,ボイラの運転状態を評価し,火力発電プラントの運転効率向上や運用性向上につながっている.また,新しい検査・評価技術により,火力発電プラントの健全性を確認し,稼働率向上に寄与している.
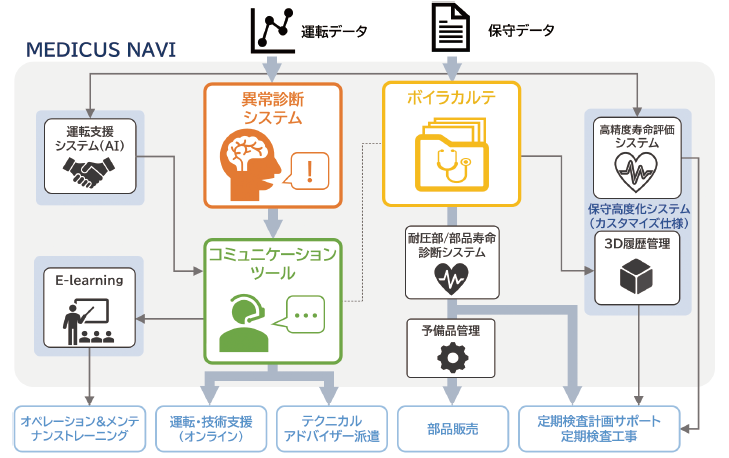
はじめに
火力発電プラントは電力の安定供給の一翼を担っており,脱炭素社会へ移行するなかでも,当面安定的な運用が求められる.また,火力発電プラントの稼働率向上のため,定期検査インターバルの長期化や定期検査期間の短縮が求められている.このような環境のなかで,IHIではデジタル技術や新しい検査・評価技術の活用によるメンテナンスの効率化に取り組んでいる.ここでは,遠隔監視技術を活用し,火力発電プラントの運転効率向上や運用性向上に寄与する運転・保守支援システムと,火力発電プラントの稼働率向上につながる新しい検査・評価技術について紹介する.
運転・保守支援システム“MEDICUS NAVI”
火力発電プラントには石炭,石油,天然ガスなどの化石燃料を燃焼させることで発電に用いる水蒸気を供給するボイラと呼ばれる設備が欠かせない.IHIはボイラメーカーとして長い歴史を有しており,世界中にボイラを納入している.近年,各国で脱炭素化の流れが加速し,火力発電プラントを新設することは減少し,メーカーはいかに既設プラントの保守・改造工事に対する競争力を維持するかが焦点となっている.さらに日本では,発電に伴うCO2排出量の削減と,電力需要の変化に伴う発電量調整への即時対応を同時に求められるなど,これまで以上に火力発電プラントを安定的に運用する必要性が生じている.そこで各社は,遠隔監視技術に基づく火力発電プラントの運転支援を目指して,火力発電プラントの稼働率および発電効率の向上,CO2排出量低減,発電要求量に対する追従性向上に向けたシステム開発を進めている.
IHIではこれまでに蓄積したエンジニアリング知識を活用し,ボイラに特化したサービスを提供するというコンセプトを掲げ,膨大な運転データや設備メンテナンスデータを共有し,最適なソリューションを一緒に考えていけるよう,お客さまとIHIをつなぐ “MEDICUS NAVI”を開発している.MEDICUSとはラテン語で「医者」という意味があり,MEDICUS NAVIは「ボイラの医者」としてお客さまに寄り添い,お客さまの症状を改善するまでの道のりを案内するという目的で開発されたシステムである.2022年現在,異常診断システム,コミュニケーションツール,ボイラカルテの機能を有し,海外の火力発電プラントにおいて実証試験を行い,運用状況評価を進めている.
(1) 異常診断システム
MEDICUS NAVIにおいて,異常診断システムは運転状況に基づいて火力発電プラントの異常状態を検出し,その情報を警報発令前にお客さまに通報し,対応のアドバイスをすることで火力発電プラントの緊急停止の頻度を低減させ,ボイラの稼働率向上に寄与している.
本システムは火力発電プラントの運転中における異常診断のため,火力発電プラントの運転データや現場計測データを分析し異常度指数を設定し,正常から逸脱した異常状態を通知する.それにより突然の異常停止が発生する前に猶予時間を確保でき,火力発電プラントの運用切り替えなど停止に向けた準備作業が可能となる.異常状態の検出項目は,火力発電プラント設備の構成により,さまざまな項目の設定を要請されるため,MEDICUS NAVIを用いて火力発電プラントを運用されるお客さまとともに各種検出項目を作りあげていくことも可能となっている.
(2) コミュニケーションツール
MEDICUS NAVIには,お客さまから寄せられる問い合わせへの対応・サポートを行うためのコミュニケーションツールが用意されている.本ツールには,火力発電プラントの状況を確認しながら迅速に対応するためのお客さまとの対話機能があり,これらの履歴を管理・活用することで,類似トラブルの再発を抑制することが可能となる.お客さまとのコミュニケーションには,これまでも電話,電子メールが活用されているが,コミュニケーションツールではチャット形式での応答が可能となっている.また,画像や動画などのデータをお客さまと簡単に共有することができる.
そのほかにも,蓄積した過去の問い合わせを収集し,体系的に保管することで情報のナレッジ化を図っている.発生した異常の類似現象をお客さま自身が検索することで,お客さま自身が主体的に対処できるように分析できる状態を目指す.
(3) ボイラカルテ
ボイラカルテ機能の活用により,これまでのメンテナンス情報を一元管理し,メンテナンス記録を整理できることで,情報検索作業を容易にして,ボイラの劣化状態に基づいたメンテナンス計画を立案できるようになる.
以前はメンテナンス記録が紙媒体であり,メンテナンス計画時の部位ごとの履歴抽出,実施時期の時系列整理において,計画ごとに煩雑な情報整理作業が発生していた.ボイラカルテ機能によるメンテナンス情報の一元化は,機器ごとで記録システムが異なる場合にはシステム間のデータ連携が困難であったことの解消にもつながり,長期運転時のプラントに関するメンテナンス情報を整理し直すことなく次の担当者に引き継ぐことが可能となる.
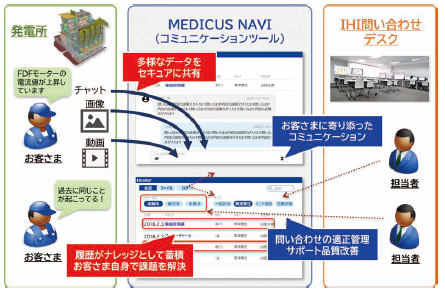
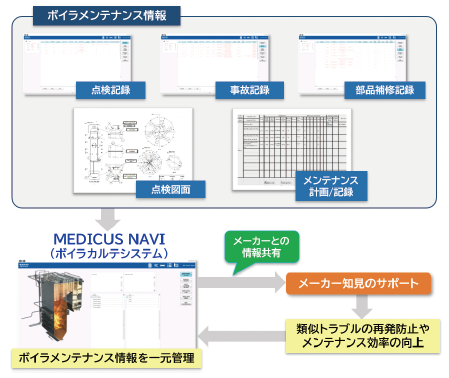
火力発電プラントの稼働率向上につながる新しい検査・評価技術
(1) ステンレス鋼の寿命評価手法
ステンレス鋼は,高温強度および耐高温酸化特性に優れるため,超々臨界圧ボイラ (USCボイラ) の伝熱管として使用されている.USCボイラの運用開始から20年以上経過しており,近年ではステンレス鋼のクリープ損傷事例が報告されている.そのため,ボイラを安定して運転するためには,ステンレス鋼のクリープ寿命評価手法を確立することが非常に重要である.一般にクリープ寿命は応力と温度に左右されるが,特に温度の影響を強く受ける.そのため,材料の使用温度を推定できれば,既存のクリープ破断試験データから高精度な寿命評価が可能である.そこで,高温での使用中に生じるステンレス鋼のミクロ組織変化に着目し,使用温度を予測できるか検討した.
ステンレス鋼の一つである火SUS304J1HTB (18Cr-9Ni-3Cu-Nb-N) を用いてクリープ試験を行い,断面組織観察を行った.その結果,結晶粒界にFe,Crの金属間化合物であるσ相が観察され,σ相の粒子径は試験時間に伴い大きくなった.そこで,結晶粒界に存在するσ相の粒子径を定量化した結果,σ相の粒子径は応力の有無や応力状態に関わらず,温度,時間の関数であるLarson-Millerパラメーター (LMP) で整理できることが分かった.よって,σ相の粒子径および伝熱管の使用時間 (t) から伝熱管の使用温度 (T) を推定できる.そして,推定した温度,管に作用する応力およびクリープ破断試験データから,伝熱管の寿命評価が可能である.本評価手法は,レプリカ検査により,実機を破壊することなく適用できる.レプリカ検査とは,実サンプル表面の金属組織を現出させ,その組織をレプリカ膜に転写する非破壊検査手法である.レプリカ膜を用いた組織観察においても,σ相はそのサイズ,形状,析出位置から,ほかの析出物と識別できる.
以上により,本評価手法はステンレス鋼の高精度な寿命評価を実機を破壊することなく実施できる手法だといえる.
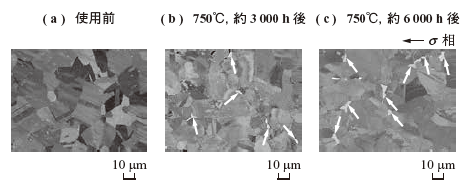
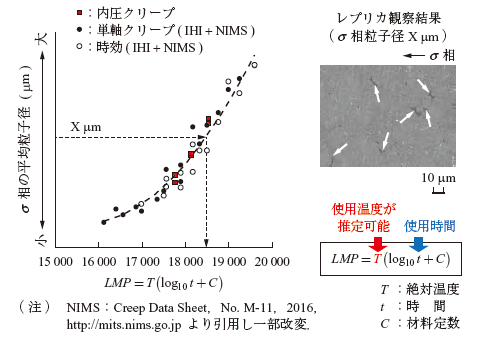
(2) 渦電流探傷試験を用いたファイアクラック検査
火力発電ボイラの火炉壁管は,高温かつ腐食性の環境にて使用されるため,高温硫化腐食やファイアクラックなどの損傷が生じる.なかでもファイアクラックは腐食疲労の一種であり,火炉の腐食環境,火炎からの加熱状況の変動などに起因して発生する.ファイアクラックの点検は,灰・スケールをブラストなどで除去した後に目視にて実施することが多いものの,目視点検でクラック深さを評価することは困難であり,事前のブラスト処理にも時間を要するという課題があった.この課題は,火炉壁管に渦電流探傷試験 (Eddy current Testing:ET) を適用すると解決できることが分かったため,その検証結果について説明する.なお,ETとは電磁誘導により生じた渦電流の変化によって対象物の表層を検査する手法である.表層にクラックがある場合は渦電流が乱れるため,その乱れをコイルで検出することで,クラックの有無が分かる.
まず初めに,灰・スケールなどが付着した状況下でクラックの検出およびその深さ評価を検証した.そのために,クラックを模擬したスリットを付与した被膜厚さの異なる試験体を3種類作製した.溶射前の信号強度を計測した後,付着を模擬した溶射試験体を準備し,溶射後の信号強度を計測した.プローブを走査したところ,各スリットで信号が出現し,その信号強度はスリット深さに対応して増加した.また,溶射を施した試験体の信号強度は,溶射を施していない試験体の半分程度であったが,被膜厚さの違いによる信号強度の差はわずかであった.
次に,ファイアクラックが生じた実機抜管材にETを適用した検証を行った.磁気探傷試験 (Magnetic particle Testing:MT) にて指示の観察された箇所ではETの信号強度が大きくなった.信号強度の大きい箇所で断面観察を実施した結果,外表面にクラックが確認され,その深さは最大0.2 mmであった.この値は,先に実施した溶射試験体での試験から予想されるクラック深さとおおむね一致した.このことから,ETによってファイアクラックの検出およびその深さ評価が可能だと分かった.
火炉壁管のファイアクラック検査にETを適用することで,これまで目視点検前に行っていたブラストや清掃などの時間を省略できる.それにより,検査に掛かる時間を大幅に短縮したメンテナンスを実現できる.
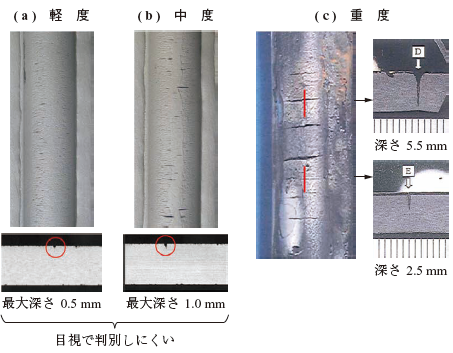
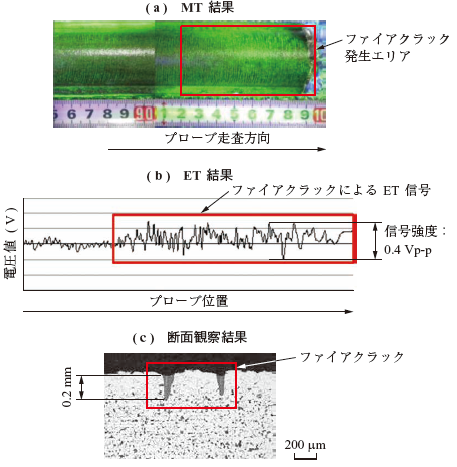
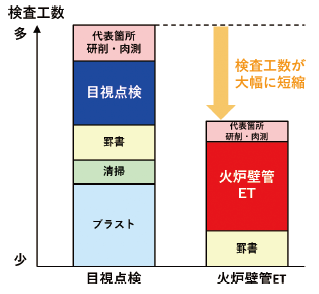
おわりに
脱炭素社会へ急速に移行するなかで,エネルギー供給源としての火力発電プラントは難しい対応を迫られている.今後,運用の変化に伴い定期検査の周期が延伸され,火力発電プラントの劣化状態の予測が難しくなるなかで,IHIではデジタル技術を活用した運用状態の把握や新しい手法としての検査や評価,そして補修技術を活用していく.また,この火力発電ボイラで確立したMEDICUS NAVI最適化や遠隔監視の考え方,ノウハウ,アルゴリズムなどを,将来的にはカーボンソリューション事業へ展開,活用を図っていく.