セラミックス基複合材料中の繊維-マトリックス近傍における界面強度特性評価
金澤真吾,岸 朋紀,久布白圭司
金澤 真吾 技術開発本部技術基盤センター材料・構造グループ 博士(工学)
岸 朋紀 技術開発本部技術企画部
久布白 圭司 IHI Asia Pacific ( Thailand ) Co., Ltd. Asia Solution Center 主幹 博士(工学)
ジェットエンジン高温部材への適用が本格化してきているセラミックス基複合材料 ( CMC ) の強度特性は,繊維-マトリックス近傍の界面強度特性に大きな影響を受ける.CMCに使用される繊維の直径は10 μm程度であり,金属基複合材料など,そのほかの複合材料に使用される繊維と比較すると小径である.そのため,CMCの界面強度を精度良く評価する手法は技術的に難易度が高く,確立された報告例はほとんどない.本稿では,界面強度試験の一つであるPush-out試験に着目し,適切な試験装置,圧子形状,試験片厚さを検討することで,繊維-マトリックス近傍の界面強度を精度良く取得することを目的とした.種々試験片を用いたPush-out試験の結果,位置決め精度の高いナノインデンターおよび先端が球形のRound end cone圧子を用いることで,116 μmまでの厚さのCMCについては,界面せん断剥離応力を取得可能であることを見いだした.ただし,試験片厚み方向に対する繊維の垂直度を考慮できていないなど,定量評価手法とするには課題も残る.
The strength properties of ceramic matrix composites ( CMCs ), which have been expected to be applied to high-temperature section parts of aircraft engines, are greatly affected by the fiber-matrix interface strength properties. However, there are few reports on the interface strength properties of small diameter fibers used in CMCs. In this paper, we investigated the appropriate device, indenter shape and thickness of the test specimen for the push-out test, one of interface strength property tests, to establish an interface strength property evaluation method applicable to CMCs consisting of small diameter fibers approximately 10 μm. As a result of the test, it was found that the interface strength properties of CMCs with a thickness of 116 μm or less can be evaluated by using a nano-indenter with a round end cone shape indenter. However, the push-out test is not enough to be a quantitative test method so far in that the plumbness of fibers to specimen thickness cannot be considered.
1. 緒言
複合材料は金属材料よりも比強度,比剛性に優れるため,航空機部材を金属材料から複合材料に代替することで航空機の軽量化へ貢献できる.この軽量化により,燃費の改善および環境負荷低減が期待される.そのため1980 年代前半より,民間機の機体およびジェットエンジン低温部材には炭素繊維強化プラスチック ( Carbon Fiber Reinforced Plastic:CFRP ) が積極的に適用され始めた ( 1 ),( 2 ).さらにジェットエンジン高温部材には,現行のニッケル ( Ni ) 基合金と比べ軽量かつ高い耐熱性を有するセラミックス基複合材料 ( ceramic matrix composites:CMC ) が,2016 年に初めて民間機に適用された ( 3 ),( 4 ).今後はさらにCMC部材の適用箇所を拡大し,航空機のさらなる燃費改善につなげる動きが活発化している.
CMCは繊維,界面コーティング層,マトリックスの三つの構成要素から成る.CMC組織の模式図を第1図に示す.三つの構成要素のいずれもぜい性材料であるセラミックスでありながら,CMCとしては高いじん性を有する.これは第1図に示すように,繊維表面に設けたもろい界面コーティング層により,マトリックスから進展してきたき裂が,繊維の表面に沿って偏向し,連続的なき裂の進展を阻害することに起因する ( 5 ) ~ ( 8 ).このように,界面コーティング層は繊維-マトリックス近傍でのき裂進展挙動に大きな影響を及ぼし,CMCの強度特性を支配する重要な因子である.そのため,繊維-マトリックス近傍の界面強度特性を正確に把握することは,CMCの破壊や強度特性を理解するうえで非常に重要である.
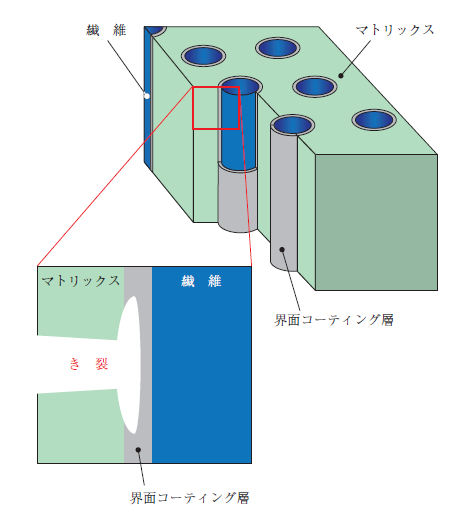
第2図に代表的な界面強度評価試験の模式図を示す ( 9 ) .複合材料の界面強度特性の評価手法には,さまざまな手法が存在する ( 9 ) ~ ( 14 ).Multiple fracture試験およびPush-in試験では,各相の体積率やヤング率といった値を使用して間接的に界面強度特性を評価する.しかしながら,CMCの繊維やマトリックスの物性値は大きなばらつきをもつため,得られる界面強度についての定量的な議論は難しい.Pull-out試験は,評価対象部材とは別に界面強度特性評価専用の試験片を作製する必要があるなど,課題も多い.Protrusion試験は,高温まで界面強度特性を評価できるほぼ唯一の手法であるが,箇所によらず界面強度は一定であるとの仮定を導入する必要があり,定量性に欠ける.一方Push-out試験は,製品など界面強度特性の評価対象部材を試験に供試でき,試験で得られる実測値のみを用い,繊維半径方向の界面せん断剥離応力を検討することができることから,CMCの界面強度評価手法として有望であると考えられる.これまでに100 ~200 μm程度の大径繊維から構成されたCMCに対し,ビッカース試験機を用いたPush-out試験が報告されている ( 15 ),( 16 ).近年ではジェットエンジンへの使用が期待される10 μm程度の小径繊維に対しても適用が検討されているが ( 10 ),( 17 ) ~ ( 19 ),報告例は少なく試験としての信頼性は乏しい.また,繊維の直径10 μm程度では界面せん断剥離応力の算出に与える界面コーティング層の厚さを無視できないため,剥離位置の確認が必要になる.
本研究では,10 μm程度の小径繊維から成るCMCに対し,Push-out試験を用いた界面強度評価手法を確立するため,界面せん断剥離応力に及ぼす試験装置,圧子形状,試験片厚さの影響を調査することで,適切な試験条件を見いだすことを目的とした.また,剥離位置を特定することで,より正確な界面せん断剥離応力の算出を試みた.
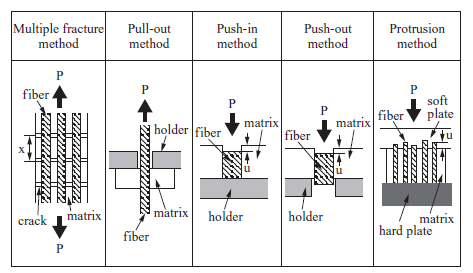
2. 試験方法
2.1 試験片作製
界面コーティング層として窒化ほう素 ( Boron Nitride:BN ) を成膜した炭化けい素 ( Silicon carbide:SiC ) 繊維束を用い,直交三次元織りの強化体とした.その後,化学気相含浸法 ( Chemical Vapor Infiltration:CVI ) ならびに低温溶湯含浸法 ( Low Temperature Melt Infiltration:LMI ) ( 20 ) によって,強化体内部の空隙にマトリックスを形成し,CMCとした.Push-out試験用の2 種類の供試体として,このCMCを樹脂包埋・研磨により87 μm,116 μmまで薄肉化し作製した.
2.2 寸法計測
試験片の厚さhはレーザ顕微鏡を用い計測した.走査型電子顕微鏡 ( SEM ) を用い,一つの繊維および界面コーティング層の全体が収まるようSEM像を撮影した.取得したSEM像を用い,必要に応じて繊維半径Rfまたは界面コーティング層を含む繊維半径Rf +BNを測定した.
2.3 Push-out試験
Push-out試験の概略図を第3図に示す.試験では供試体をSUS製のジグに設置した.供試体を置いたジグには,試験中に繊維とジグが接触しないよう幅30 μmのスリットが入っている.その後,スリット上の繊維に荷重を加え,荷重-変位曲線を取得した.圧子には,第4図に示す三角すい形状のBerkovich圧子および先端が球形のRound end cone圧子の2 種類の圧子を用いた.そのほかの試験条件を第1表に示す.
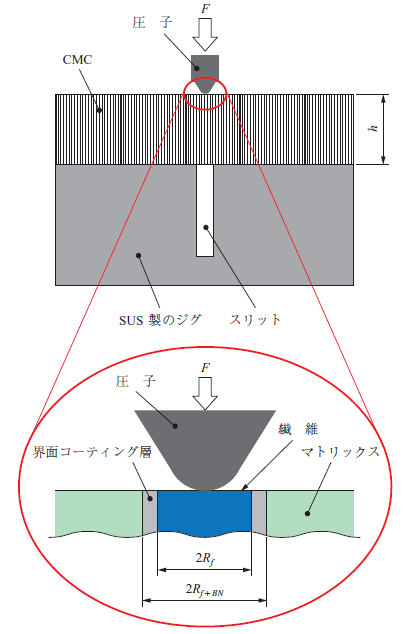
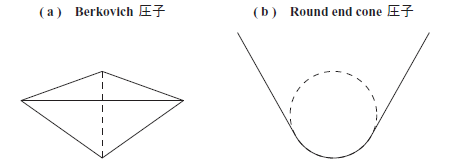
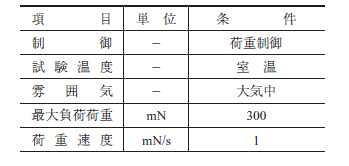
3. 結果
3.1 試験装置の選定
Push-out試験に適した試験装置として,過去の報告 ( 10 ),( 15 ) ~ ( 19 ) でも用いられているビッカース試験機と位置決め精度に優れ,圧子形状の変更が可能なナノインデンターを候補とした.10 μm程度の小径繊維から成るCMCの繊維中央部に荷重を付与する場合,中央から数 μm程度のずれによって圧子が界面コーティング層やマトリックスに接触し,Push-out試験が成立しない可能性がある.そのため,試験機の位置決め精度は1 μm以下が望ましいと考えられる.ビッカース試験機の位置決め精度は2 μm程度であり,ナノインデンターの位置決め精度は数 nmオーダーであることから,Push-out試験ではナノインデンターが適当であると判断し,採用した.
3.2 Push-out試験に及ぼす圧子形状の影響
形状が異なるBerkovich圧子とRound end cone圧子の2 種類を用いて,Push-out試験を実施した.Push-out試験後のSEM像を第5図に示す.それぞれの圧子ではいずれも,繊維の一様な圧縮応力による半径方向への膨らみに加え,繊維の局所的な変形による効果などが重畳し,界面に生ずる応力が増加することにより,せん断破壊したと考えられる.Berkovich圧子を用いた場合,Push-out試験後の繊維には明瞭な圧痕が認められた.繊維はぜい性材料のため,局所的な破壊により永久変形が残ったと考えられる.繊維の局所的な永久変形により,繊維と界面コーティング層の間での摩擦力が増大し,荷重-変位曲線取得時の荷重値に影響を与えることが懸念される.一方,Round end cone圧子を用いた場合では,繊維に圧痕は認められず,局所的な永久変形に伴う摩擦力の増大は軽微であると考えられる.よって,Push-out試験に適した圧子は,繊維の局所的な永久変形が認められなかったRound end cone圧子であると判断した.
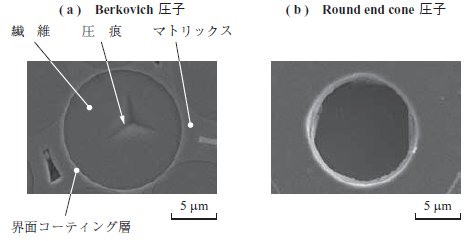
3.3 厚さが異なる試験片を用いた界面せん断剥離応力の算出
厚さ87 μmおよび116 μmの試験片を用い,Push-out試験を実施した.Push-out試験前後における,各試験片のSEM像を第6図に示す.Push-out試験後では,厚さ87 μmの試験片,厚さ116 μmの試験片ともに,繊維はマトリックスから剥離している様子が観察された.また,Push-out試験後における典型的な繊維の剥離の様子を第7図に示す.この図からPush-out試験による繊維の剥離は,繊維と界面コーティング層の間で生じたことが明らかとなった.
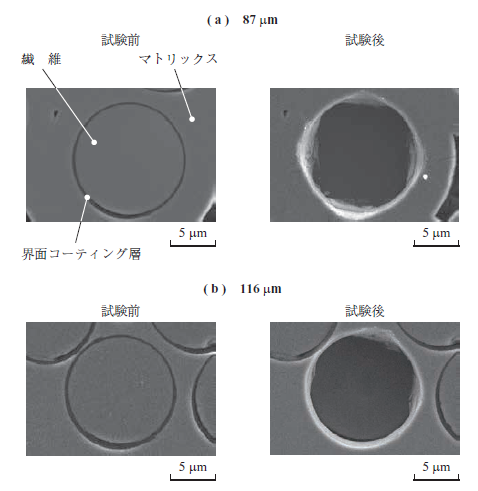
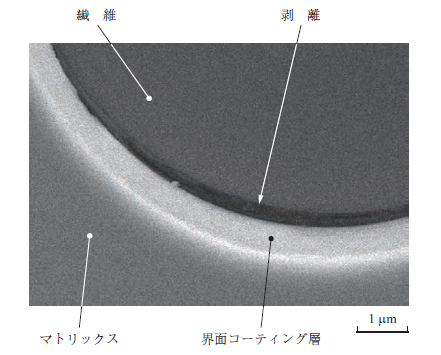
Push-out試験により得られた荷重-変位曲線を第8図に示す.厚さ87 μmの試験片では試験荷重が79.2 mN,厚さ116 μmの試験片では試験荷重が118.1 mNまで増加した際に,変位が瞬間的に増加した.これは,界面コーティング層から繊維が全面剥離し,圧子が荷重負荷方向に急激に移動したためであると考えられ,既存文献の報告とも整合する ( 10 ),( 15 ) ~ ( 19 ).全面剥離に至るまで荷重-変位曲線に変曲点は認められていないことから,初期剥離と全面剥離はほぼ同時に生じたものとみなし,本材料系においては特に区別していない.そこで急激に変位が増加するときに界面剥離が発生したと判断し,このときの荷重Fdを用いて ( 1 ) 式により界面せん断剥離応力τdを求めた.
なお,繊維の剥離後も圧子が荷重方向に移動しマトリックスと接触することで,荷重の再上昇が認められた.前述のように,Push-out試験による繊維の剥離位置は繊維と界面コーティング層の間であることから,( 1 ) 式中のRには繊維半径Rfを用いた.
τd = Fd /2πRh ………………(1)
厚さ87 μmの試験片ではτdが23.7 MPa,厚さ116 μmの試験片ではτdが27.4 MPaであった.これらの値は,本田らが報告したビッカース試験機により繊維の直径144 μmを対象に実施したPush-out試験で得られた値と比較的よく一致した ( 15 ).以上のことから,Push-out試験により,厚さ116 μmまでの10 μm程度の小径繊維から成るCMCの界面せん断剥離応力を測定するためには,数nmオーダーの位置決め精度を有するナノインデンターおよび繊維の破壊に伴う局所的な永久変形を与えないRound end cone圧子を用いることが有用であることを明らかとした.
4. 結言
10 μm程度の小径繊維を用いたCMCの界面特性評価手法としてPush-out試験を選定し,試験装置,圧子形状,試験片厚さの影響について検討を行い,以下の結論を得た.
- Push-out試験では繊維中央部分に正確に荷重を付与する必要があるため,試験装置としては数 nmオーダーの位置決め精度をもつナノインデンターが適切であると判明した.
- Push-out試験に用いる圧子には,繊維の破壊を伴う局所的な永久変形を与えない先端が球形のRound end cone圧子が有用である.
- Push-out試験後に試験片のSEM観察を実施することで,剥離位置を把握した.これにより,( 1 ) 式で示す界面せん断剥離応力の計算に用いるRとして繊維半径Rfを選択し,計算精度を向上させた.
- 厚さ87 μm,116 μmの試験片において,界面せん断剥離応力に明確な差異は認められなかった.しかし,試験片厚み方向に対する繊維の垂直度を考慮できていないなど,定量評価手法とするには課題も残る.
本稿で検討・実施したPush-out試験は,10 μm程度の小径繊維から成るCMCに対する界面特性評価手法として有用である.本技術の高度化によりCMCの破壊メカニズム理解を深め,それにより優れた強度特性を有するCMC開発につなげ,航空機への適用範囲を拡大,ジェットエンジンの燃費向上,ひいてはカーボンニュートラルの実現に貢献していく.
参考文献
(1) 盛田英夫:航空エンジン用FRP部品の開発,日本航空宇宙学会誌,Vol. 48,No. 558,2000年7月,pp. 416-421
(2) 大隅 真:航空機工業における材料の現状と動向,溶接学会誌,Vol. 52,No. 5,1983年4月,pp. 418-431
(3) G. Corman and K. Luthra:Development history of GE’s prepreg melt infiltrated ceramic matrix composite material and applications,Comprehensive Composite Material II,Vol. 5,(2018),pp. 325-338
(4) G. Gardiner:Aeroengine Composites, Part 1: The CMC invasion,Composites World,https://www.compositesworld.com/articles/aeroengine-composites-part-1-the-cmc-invasion,(参照2022. 9. 20)
(5) F. Zok:Ceramic-matrix composites enable revolutionary gains in turbine engine efficiency,American Ceramic Society Bulletin,Vol. 95,No. 5,(2016. 7),pp. 22-28
(6) J. DiCarlo and Hee-Mann Yun:Non-oxide (Silicon Carbide) fibers,Handbook of ceramic composites,N. P. Bansal,(2005),pp. 33-52
(7) T. Ishikawa, K. Bansaku, N. Watanabe, Y. Nomura, M. Shibuya and T. Hirokawa:Experimental stress/strain behavior of SiC-matrix composites reinforced with Si-Ti-C-O fibers and estimation of matrix elastic modulus,Composites Science and Technology,Vol. 58,Iss. 1,(1998),pp. 51-63
(8) R. Naslain:Fiber-reinforced ceramic matrix composites: State of the art,challenge and perspective,KOMPOZYTY (COMPOSITES) ,Vol. 5,No. 1,(2005),pp. 3-19
(9) 香川 豊:複合材料の界面力学と界面特性評価・解析―I. 繊維強化セラミックスの界面力学と力学特性の測定,日本複合材料学会誌,Vol. 21,No. 1,1995年,pp. 2-7
(10) K. Goto, I. Kawahara, H. Hatta, Y. Kogo and I. Shiota:Measurement of fiber/matrix interface properties of C/C composites by single fiber and fiber bundle push-out methods,Composite Interfaces,Vol. 12,Iss. 7,(2005. 1),pp. 603-616
(11) 本田紘一,香川 豊:突き出し法による繊維強化セラミックスの界面せん断応力の測定,日本金属学会誌,Vol. 56,No. 11,1992年5月,pp. 1 360-1 369
(12) 三輪 實:複合材料の界面力学と界面特性評価・解析―III. PMCの繊維/樹脂界面特性,日本複合材料学会誌,Vol. 21,No. 3,1995年,pp. 83-88
(13) 池上皓三:繊維強化複合材料の界面強度,繊維と工業,Vol. 41,No. 8,1985年,pp. 275-281
(14) T. Yano and K. Yoshida:Mechanical and interfacial properties of SiC fiber-reinforced SiC composites,Strength, Fracture and Complexity,Vol. 1,No. 3,(2003),pp. 157-165
(15) 本田紘一,香川 豊:SiC繊維強化Ti複合材料の界面応力伝達機構,日本金属学会誌,Vol. 58,No. 1,1994年8月,pp. 91-97
(16) 香川 豊,大蔵明光:プッシュアウト法によるSiC (CVD) 繊維強化Ti-15Mo-5Zr-3Al複合材料の界面せん断強度の測定,日本金属学会誌,Vol. 56,No. 3,1992年9月,pp. 278-284
(17) D. Marshall:An indentation method for measuring matrix-fiber frictional stresses in ceramic composites,Journal of the American Ceramic Society,Vol. 67,No. 12,(1984),pp. 259-260
(18) K. Yoshida:Development of silicon carbide fiber-reinforced silicon carbide matrix composites with high performance based on interfacial and microstructure control,Journal of the Ceramic Society of Japan,Vol. 118,No. 1 374,(2010),pp. 82-90
(19) R. Kerans, R. Hay, N. Pagano and T. Parthasarathy:The role of the fiber-matrix interface in ceramic composites,American Ceramic Society Bulletin,Vol. 68,No. 2,(1989),pp. 429-442
(20) 金澤真吾,山崎直樹,朝倉勇貴,久布白圭司,石川毅彦,小笠原俊夫:直交3次元非晶質SiC繊維/SiC/YSi2-Si基複合材料の開発,材料,Vol. 70,No. 2,2021年2月,pp. 86-92