CMC冷却孔部寿命評価手法の開発
佐藤速夫,春山大地,北村祥之,中村 寛,本田達人
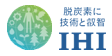
佐藤 速夫 航空・宇宙・防衛事業領域技術開発センターエンジン技術部
春山 大地 技術開発本部技術基盤センター数理工学グループ
北村 祥之 航空・宇宙・防衛事業領域技術開発センターエンジン技術部 グループ長
中村 寛 航空・宇宙・防衛事業領域技術開発センター技術管理部 グループ長 博士(工学)
本田 達人 航空・宇宙・防衛事業領域技術開発センターエンジン技術部 部長
セラミックス基複合材料 ( Ceramic Matrix Composites:CMC ) は,Ni基合金に比べて耐熱性や比弾性率が高く,航空機タービンエンジン部品などへの適用拡大が望まれている.材料の耐熱温度を超える高温のガスにさらされる部品では,冷却のために部品表面に微小孔を空けるのが一般的であるが,微小孔を空けたことによるCMCの疲労寿命への影響を調査した先行研究例は僅かである.本研究では,この影響を調査するため,多種の冷却孔平板試験片を用いて冷却孔の形状と疲労強度の関係を調査した.その結果,単孔と複数孔では異なる破壊モードとき裂の進展様式が観察された.これらの異なる破壊モードを有する試験片の疲労強度を説明するために寿命評価モデルを検討し,強度パラメータの考えを導入した.強度パラメータは,有限要素解析 ( Finite Element Analysis:FEA ) より予測された応力分布をCMCの単位領域(ユニットセルサイズ)で平均化することで算出し,疲労寿命を評価した.本評価手法により疲労寿命を評価した結果,孔のない平滑試験片について得られたS-N線図から多種の冷却孔形状を有する試験片の疲労寿命予測が可能であることを確認した.
Ceramic matrix composites ( CMC ) have higher heat resistance and specific modulus than Ni-based alloys, thus they are desired to be more applied to aircraft engine parts such as turbine parts. When engine parts are exposed in the condition over the heat proof temperature, multiple holes are generally pierced on them in order to cool their surface. However, there are few research results on small hole effect for CMC fatigue life. This study focused on this phenomenon. Fatigue tests were conducted using flat plates manufactured with a single hole and multiple holes. As a result of tests, different fracture and crack propagation modes were observed between single-holed and multiple-holed types. A life prediction model was considered to explain the life degradation. The strength parameters were calculated by averaging stress fields, which were predicted by finite element analysis ( FEA ) , in area of CMC unit cell. By using the life prediction model developed in this study, fatigue lives of all types of specimens with hole can be predicted based on the S-N curve obtained from a smooth-shaped specimen without hole.
1. 緒言
国際航空運送協会 ( The International Air Transport Association:IATA ) は,2050 年までに民間航空機の炭素排出量を正味ゼロにするという目標を掲げている ( 1 ).この達成に向けて,タービン入口温度 ( Turbine Inlet Temperature:TIT ) を上昇させて,エンジン性能を向上させる取組みがなされているが,そのためには,より耐熱性の高い材料が求められている.第1図に耐熱温度と比強度に関する材料性能を示す.CMCは,Ni基合金よりも耐熱性に優れており,タービン部品などの航空機エンジンへ適用することで性能向上や軽量化が期待されている.
国立研究開発法人宇宙航空研究開発機構 ( Japan Aerospace Exploration Agency:JAXA ) は,NOxとCO₂を削減する競争力のある技術を獲得することを目的としたコアエンジン技術実証プロジェクト ( Environmentally compatible Core engine technology research project:En-Core ) を2018 年に開始した ( 2 ).このプロジェクトで,JAXAとIHIは,次世代エンジンタービンのコンセプトを提案し,設計技術の開発と設計検証を実施している.提案された次世代タービン翼のコンセプトを第2図に示す.これまでの先行研究では,CMCを高温部品に適用した場合を想定した冷却システムの検討が積極的に行われてきた ( 3 ).一方,冷却のために複合材料に空けた微小孔と機械的特性の関係に関する研究例は僅かであった.本研究では,冷却孔の仕様(大きさ,形状,ピッチ)と疲労寿命の関係に焦点を当て,単純平板に微小孔を空けた冷却孔平板試験片を作製し,疲労試験を実施した.
2. 試験
2.1 材 料
試験片を切出したCMC板は,SiC(炭化けい素)の連続繊維織物で構成されており,三次元織と呼ばれる構造を有している.繊維は化学気相浸透法 ( Chemical Vapor Infiltration:CVI ) によりサブミリオーダーの繊維束に束ねられ,繊維束は溶融浸透法 ( Melt Infiltration:MI ) で希土類材料により固化して形成される.試験片は,成形されたCMC板を機械加工することにより作製した.
2.2 試験片形状
代表的な試験片の寸法を第3図に示す.有孔試験片の孔は,レーザ加工によって形成した.孔の形状および孔と繊維束の位置関係の模式図を第4図に示す.孔の傾斜角度は,試験片荷重方向に垂直な断面内における試験片幅方向に対する孔の角度を表す.平板の孔とCMCを構成する繊維束の位置関係は,機械的特性において重要と考えられるため,本研究では,孔を繊維束の中央に配置した.また,孔部の応力集中による強度低下を確認するために,比較として無孔試験片を用意した.無孔試験片の形状は,ASTM1275 ( 5 ) に従う平滑形状とした.
2.3 試験条件
本研究では,試験片の変形量を調査するため,室温におけるストレスサーベイ試験と疲労特性を確認する高温疲労試験を実施した.試験条件を第1表に,測定装置を第5図に示す.
ストレスサーベイ試験は,試験片の荷重値と変形量およびひずみ量との関係を調査することを目的とした.そのため,室温下試験片に微小な荷重を与え,伸び計とひずみゲージを用いて試験片の標点間の変形量とひずみを計測した.
疲労試験は,高温下における有孔試験片の疲労寿命を取得することが目的である.試験は,1 200℃雰囲気中で行った.応力比の目標値を0.1として,荷重制御により試験荷重を制御した.
3. 寿命予測手法
3.1 応力予測モデル
孔部周囲の応力分布は,FEA ( Finite Element Analysis ) を用いて予測した.CMCをマクロな直交異方性材料と仮定して,材料モデルの入力値は,別途行った材料基礎試験から得られた値を適用した.
解析モデルの形状は,ディフューザ孔試験片を除き,図面記載のノミナル寸法に従った.ディフューザ孔の形状は,実際に製造された孔の寸法の計測値にばらつきがみられたため,実寸法を有限要素モデルに再現した.
3.2 寿命予測モデル
有孔試験片の寿命予測の精度を確認するために,無孔試験片との強度比較を行った.無孔試験片のlog (σ) −log ( Nf ) 回帰直線と有孔試験の試験荷重における評価応力-破断サイクル関係をプロットすることで,両者の関係を比較した.
有孔試験片の寿命評価に用いた評価応力は,有限要素モデル上の特定断面の特定範囲内で解析により得られた応力値を平均化することで算出した.第6図に垂直孔試験片を例に評価断面と平均化領域の関係について示す.断面の向きは荷重方向に対して垂直である.平均化領域の大きさはCMCのユニットセルサイズに相当する.
4. 試験結果
4.1 ストレスサーベイ試験
ひずみゲージにより取得したひずみ履歴とFEAによる予測値を第7図に示す.孔部から離れたひずみゲージの計測値は予測値と良い一致を示した.伸び計により測定したひずみ履歴とFEAによる予測値を第8図に示す.孔に近づいた伸び計によるひずみ計測値は,単数孔タイプは,予測値と良い一致を示した.一方,複数孔タイプでは,1 000 N以下では予測値と一致するものの,それ以上の荷重では,予測に対して高めに計測された.この原因として,連続した孔では損傷が発生している可能性が考えられる.
4.2 疲労試験
第9図に疲労試験前後の孔部周囲の画像を示す.いずれの試験片も,孔の中心位置で破断していることを確認した.
伸び計により計測したひずみのサイクル履歴を第10図に示す.第10図では,サイクリック荷重における最大/最小ひずみをプロットした.単孔試験片のひずみは,時間の経過とともに単調かつ連続的に増加し,破断時に不連続にひずみが急増することを確認した.一方,複数孔試験片のひずみは時間経過に伴い階段状に増加する様子が確認された.また,ひずみおよび荷重のサイクル履歴を比較すると,ひずみが上昇した後に荷重の低下が生じることが確認された.これらの情報から,複数孔試験片では,ひずみが階段状に上昇したタイミングで試験片内部に損傷が進展したことが想定される.よって,ここでは,孔部の初期損傷の定義をひずみの最初の不連続上昇タイミングとし,最終破断を荷重低下のタイミングとした.本稿では,初期損傷時のサイクル数を用いて疲労寿命を評価した.
5. 考察
第11図に疲労試験で得られた有孔試験片の評価応力-初期損傷時のサイクル数の関係を,1 200℃環境下における無孔試験片のS-N線図上に併記した結果を示す.第11図 - ( a ) の縦軸は,試験片の最小断面にかかる断面平均応力を用いた結果である.また,第11図 - ( b ) の縦軸は,3. 2 節で示した方法により算出した平均化応力を用いて表した結果である.
第11図 - ( a ) の方法を用いた場合,有孔試験片の強度は,無孔試験片の回帰直線に対して低い強度を示す.一方,第11図 - ( b ) の方法を用いた場合,有孔試験片の強度は無孔試験片の回帰直線の±10%以内に収まる結果を得た.本検討の範囲では,FEAからユニットセルサイズで平均化した応力を用いて有孔試験片の疲労寿命を評価することで,孔の形状や配置の変更があっても,無孔試験片の試験結果から疲労寿命が予測できることが確認された.
なお,ストレスサーベイ試験において,孔部周囲のひずみ分布の検証は今後の課題である.高解像度の画像を用いたひずみ解析を進めることが有効と考える.
6. 結言
本研究では,冷却孔を想定した有孔平板試験片を設計し,孔の仕様と疲労寿命の関係を調査した.疲労寿命は,ひずみ履歴におけるひずみ初期の不連続増加のタイミングに相当するサイクル数として定義した.そして,FEAからユニットセルサイズで平均化した応力を用いることによって,4 種類の有孔試験片に対して無孔材のS-N線図から疲労寿命を予測できることが確認できた.
一方,FEAからユニットセルサイズで平均化した応力を用いることで,複数の有孔試験片の疲労寿命を精度良く予測できる理由については明らかになっていない.今後,損傷メカニズムを理解する必要があり,予測破断サイクルにおける有孔試験片の孔部周辺の損傷を観察し,それぞれの試験片の損傷の様相を特定することが効果的である.孔部周辺の微小な損傷を捉えるためにも,これまで以上に高分解能の機材を用いた観察が有効と考える.
また,解析モデルのひずみ・応力の予測精度を向上する手段として,CMCの剛性低下を表現できる均質体として損傷モデルの導入が考えられる.一方で,繊維束とマトリックスが連なる微小構造を有するCMCに対して実際の孔の位置関係によっては,均質体モデルにより予測される応力を用いた強度評価結果は,実態よりも高く見誤るリスクも考えられる.現状危険側の予測がなされていないため,上記のようなリスクや評価の手間を踏まえる必要性について今後議論していきたい.
― 謝 辞 ―
本稿の成果は,コアエンジン技術実証( En-Core [ アン・コア ] )プロジェクトによって得られた成果である.国立研究開発法人宇宙航空研究開発機構 ( JAXA ) の関係者の皆さまに深く感謝します.
参考文献
(1) IATA:Our Commitment to Fly Net Zero by 2050,https://www.iata.org/en/programs/environment/flynetzero/,(参照2022. 12. 1)
(2) 山根 敬:En-Coreプロジェクト(コアエンジン技術実証) - 環境技術の実証に向けて,https://www.aero.jaxa.jp/news/event/pdf/sympo211105/sympo02.pdf,(参照2023. 11. 15)
(3) P. H. Wilkins et.al:Effect of a Ceramic Matrix Composite Surface on Film Cooling,Journal of Turbomachinery,( 2022. 3 )
(4) 中村武志:高温用非金属材料の技術動向,日本ガスタービン学会誌,Vol. 38,No. 3,( 2010 ),pp. 140-145
(5) ASTM C1275-18:Standard Test Method for Monotonic Tensile Behavior of Continuous Fiber-Reinforced Advanced Ceramics with Solid Rectangular Cross-Section Test Specimens at Ambient Temperature,( 2018. 1 )