微小サンプルによる材料評価技術
中原庸裕,木村尭弘
中原 庸裕 技術開発本部技術基盤センター材料・構造技術部
木村 尭弘 技術開発本部技術基盤センター材料・構造技術部
微小サンプルを用いた材料評価技術は,原子力・火力発電プラントの劣化評価から始まり,溶接継手や生体材料の評価など多様な産業分野へと応用されている.特に,スモールパンチ試験は,微小サンプルからの試験片の加工が比較的容易であり,さまざまな機械特性の評価に有効である.本稿では,スモールパンチ試験の手法,基本原理,および有用性を概説する.
Material evaluation method with miniature specimen, which originated in the assessment of degradation in nuclear and thermal power plants, are now applied in diverse industrial fields, including the evaluation of weld joints and biomaterials. In particular, the Small Punch test is relatively easy in terms of preparation from miniature specimens and is effective for evaluating various mechanical properties. This article outlines the methods, fundamental principles, and utility of the Small Punch test.
1. 緒言
微小サンプルを用いた材料評価技術は,主に原子力・火力発電プラントの構造部材の劣化や損傷の程度を評価する手法として開発され発展してきた ( 1 ) ~ ( 3 ).近年では,溶接継手の接合部やインプラント向けの生体材料,航空エンジン用材料の機械特性評価など,他の産業分野にも応用されている ( 4 ) ~ ( 7 ).構造物の安全性と信頼性を確保するには,実製品を用いた評価が有効であり,そのサイズに見合った評価手法が求められる.
微小サンプルを用いた試験手法としては,標準試験を小型化したサブサイズ標準試験 ( 8 ) ~ ( 11 ),押込み試験 ( 12 ),スモールパンチ ( Small Punch:SP ) 試験 ( 13 ),( 14 ) などがある.そのうちSP試験は,厚さ1 mm以下の薄型のサンプルで評価が可能であり,ドッグボーン形状や砂時計形状などに加工する必要があるサブサイズ標準試験に比べて試験片の加工が容易である.また,SP試験は,クリープ特性を評価するスモールパンチクリープ ( Small Punch Creep:SPC ) 試験 ( 15 ) や疲労特性を評価するスモールバルジ疲労 ( Small Bulge Fatigue:SBF ) 試験 ( 16 ) などの応用技術も開発されている.これらの試験技術に関する研究は,主に金属材料を対象に多くなされており,引張り,クリープ,疲労,破壊じん性などの機械特性との相関が確認されている ( 13 ) ~ ( 19 ).そのため,これらの技術はより幅広い産業分野での活用が期待される.本稿ではSP試験の手法,基本原理,その有用性について解説する.
2. スモールパンチ試験
第1図にSP試験の概略図を示す.SP試験は,薄い円盤状の試験片を上部ダイと下部ダイで挟んで固定し,円筒形のパンチャーで試験片を押込み破断させる試験方法である.SP試験で一般的に用いられる試験片は,直径3 ~10 mm,厚さ0.5 mmであり,単軸引張試験片と比較して材料の使用量が少なく,局所的な評価が可能である.
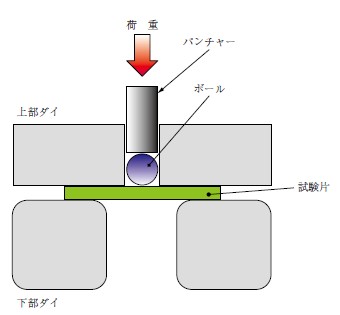
SP試験は押込みによる曲げと膜の伸長により変形が不均一となり応力とひずみが多軸状態となるため ( 3 ),( 17 ),( 18 ),得られる結果に対する解釈は複雑である.第2図は金属材料のSP試験で得られる典型的な荷重-変位曲線である.これは,過去の実験的,解析的研究により,次のように解釈される ( 20 ),( 21 ).
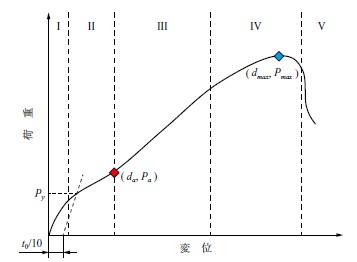
- 領域I :試験片全体が弾性変形する領域
- 領域II :弾性変形から塑性変形へ移行する領域
- 領域III :多軸応力により膜が伸長する領域
- 領域IV :試験片の厚みが減少し,ボイドが形成・成長する塑性不安定な領域
- 領域V :亀裂が成長し破断する領域
さまざまな研究者が,SP試験結果から機械特性を推定するための定式化を試みている ( 3 ),( 13 ),( 18 ).例えば,Garcíaら ( 18 ) は,ステンレス鋼やアルミ合金を対象に,厚さ0.5 mmに切り出した試験片を用いたSP試験とASTM E8に準じた引張試験を行い,SP試験から降伏応力と引張強度を推定する式を,それぞれ( 1 ) 式,( 2 ) 式として提案した.
(2).jpg)
ここで,t0は試験片初期厚みであり,Pyは荷重-変位曲線とこの曲線の原点における接線を横軸にt0 /10オフセットした直線との交点である.また,Pmaxとdmaxは,荷重変位曲線における最大荷重とそのときの変位である.( 1 ) 式の降伏応力の推定式では,Pyをt0
2で割ることで厚さの影響を排除しており,サンプル調製のばらつきの影響が軽減される.一方,( 2 ) 式の引張強度の推定式では,試験片が最大荷重に達する前に厚さが減少することを考慮し,t0だけでなく最大荷重時の変位dmaxも使用している.
大田ら ( 22 ) は,これまで金属材料を対象に検討されたSP試験の適用範囲拡大のため,複数の樹脂を対象としてSP試験と引張試験を行い,SP試験により樹脂材料の機械的特性評価の適用可能性を検証した.その結果,0.2%耐力は ( 1 ) 式で同様の換算ができることを確認した.一方,引張強度は ( 2 ) 式のPmaxとdmaxでは表現ができなかったことから,領域IIから領域IIIへの転換点の荷重Paと変位量daを定義し,( 3 ) 式による換算を試みた.
.jpg)
第3図に( 2 ) 式,( 3 ) 式によってさまざまな樹脂材料のSP試験結果を引張強度に換算した結果を示す.( 2 ) 式による換算結果は引張試験結果より低強度側の値となるのに対して,( 3 ) 式による換算結果は引張試験結果と比較的よく一致した.領域IIから領域IIIの転換点を用いる理由は,領域III以降の多軸応力下の変形や塑性不安定となる影響を避けるためと考えられている.
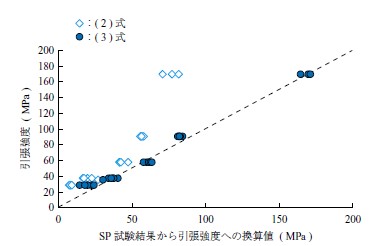
その他,SP試験を応用して,弾性率 ( 23 ) や破壊じん性 ( 24 ),( 25 ) を推定する方法も提案されている.
このように,SP試験は結果の解釈が複雑ではあるものの,材料の機械的特性との相関が高い手法であり,体積の限られた材料や製品の微小部位の評価に有効な手法である.
3. スモールパンチクリープ試験
SPC試験は,試験温度に加熱された電気炉内部において,上部ダイと下部ダイで挟んだ薄い円盤状の試験片に対し,ボールとパンチャーを介して試験片中央に一定荷重Fを負荷して実施する.試験時間に伴う試験片の変位と,試験片の破断時間を測定することが可能な試験法である.試験片・ジグの形状はSP試験(第1図)と基本的に同じであるが,電気炉にて加熱しながら試験することから,試験片酸化を抑制するために,アルゴン ( Ar ) ガスなどの不活性ガスを流して試験する.SPC試験片の一般的な寸法は,直径7 ~10 mmの円盤もしくは10 mm四方の板であり,厚さは0.5 mmである ( 26 ).
久布白ら ( 27 ) は,火力発電ボイラに使用される2.25Cr-1Mo鋼の溶接継手を用いて,単軸クリープ試験とSPC試験を行うことによって,溶接継手の余寿命評価手法を検証した.本手法では,クリープ損傷率をDc,SPC試験によるクリープ損傷率をDspとし,( 4 ) 式に示す損傷和Dについて,Dが0.8 ~1.2の範囲に収まることを明らかにした.第4図に線形損傷則によるクリープ損傷値とSPC損傷値の評価結果を示す.
.jpg)
ここで,
(6).jpg)
であり,tiは単軸クリープ試験を中断するまでの試験時間,trは単軸クリープ試験の破断時間,t′rはtiで中断した単軸クリープ試験片から採取した素材で実施したSPC試験の破断時間,t″rは単軸クリープ試験片の溶接継手と同じ材質の新材から採取・試験したSPC試験の破断時間である.
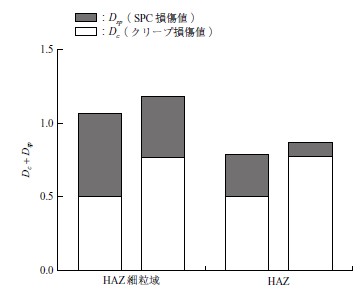
この関係より,クリープ損傷率DcをSPC試験によって評価することが可能である.また,SPC試験片中央に溶接熱影響部 ( Heat Affected Zone:HAZ ) が分布するように,母材および溶接金属を含めて採取した場合でも,損傷和は0.8 ~1.2の範囲にあった.そのため実機の溶接継手に対し,表面からのサンプリングによるクリープ余寿命評価が可能であることが示唆される.
SPC試験はクリープ特性を評価する試験手法であるが,前述のとおり,SPC試験では応力σではなく荷重Fを負荷する.したがって,通常の単軸クリープ試験結果と比較するためには,この荷重を応力に変換する必要がある.荷重/応力 ( 28 ) の換算式F/σについては,例えば,SP試験結果より得られるFm(最大荷重),um(最大荷重時の変位)および試験片の厚さを用いたものや,umc(SPC試験にて最小変位速度に達したときの変位)を用いたもの ( 29 ),( 30 ) など,多くの手法が提案されている.第5図にSPC試験によるクリープ余寿命評価フローの例を示すが,前述の手法を用いて適切な応力条件に換算することにより,通常の単軸クリープ試験と同様,実製品のクリープ余寿命評価への活用が可能となる.
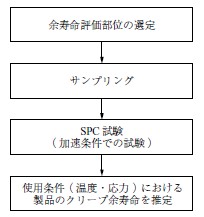
4. スモールバルジ疲労試験
SBF試験は,Komazakiら ( 16 ) によって開発された円盤状の試験片を用いた疲労特性を評価する試験方法である.第6図にSBF試験の模式図を示す.銅パッキンで固定された試験片の隣接したところには油圧室が備わっており,油圧で試験片を板厚方向に荷重を負荷する構造となっている.サーボバルブの切り替えによって一定圧力の油圧を試験片両面から交互に負荷することで,両振りの疲労試験を実現する.SBF試験片の断面形状および寸法を第7図に示す.試験片形状は片面が平面で,もう片面は凹面の形状を取っており,銅パッキンの固定部における応力集中による破壊を防いでいる.また,片面側を平面とすることで疲労寿命に影響を与えると考えられる材料表面を残すことができる.
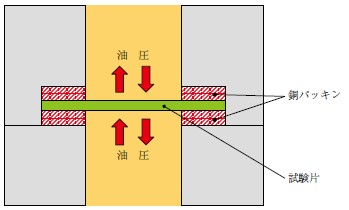
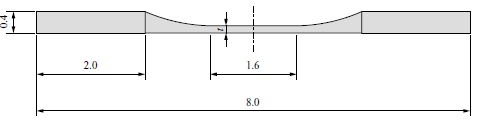
SBF試験はSP試験,SPC試験と同様に多軸応力となるため,単軸の疲労試験との比較には注意が必要である.ここでは,ニッケル ( Ni ) 基インコネル®718を対象とした事例を紹介する.SBF試験は,油圧室の圧力が一定の値に低下した段階で装置が自動停止するよう設定して行う.自動停止後の試験片には,中心から放射状の亀裂が生じ,一部の試験片で欠落が観察される.すなわち試験片の破断により試験が終了する.試験時のひずみは,試験片平面側の中心付近にひずみゲージを貼り付け取得する.なお,本試験のように対象とする試験材の強度レベルがひずみゲージの強度に比べ極端に高い場合は,ひずみゲージ貼り付けによる寿命への影響はないと考えられる.
第8図は,試験片の中心部の厚さtと圧力を変えて行ったSBF試験における,破断に至るまでのひずみとサイクル数(疲労寿命)の関係を示している.同図には,従来の疲労試験(単軸疲労,超音波疲労,回転曲げ疲労)の結果もプロットしている.両者の疲労寿命には一定の相関が認められたが,SBF試験の疲労寿命は,従来の疲労試験に比べ長寿命側へシフトする結果となった.
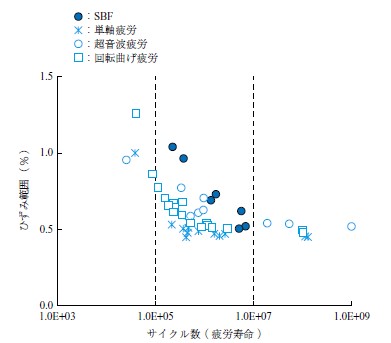
吉崎ら ( 31 ) は,SUS316を対象にSBF試験を行い,表面亀裂長さの比で疲労寿命を規格化することで単軸疲労試験の結果と一致することを報告している.同様にインコネル718のSBF試験結果について,規格化を試みた.SBF試験片の平行部に相当する1.6 mmに亀裂長さが達する繰り返し数N1.6を,それぞれSBF試験の疲労寿命Nf (SBF),単軸疲労試験の疲労寿命Nf (UA) として定義すると,次のような関係が得られた.
(8).jpg)
この関係から,以下の ( 9 ) 式の換算式が求められる.
.jpg)
( 9 ) 式を用いて規格化した結果を第9図に示す.同図より,SBF試験における疲労寿命が従来の疲労試験の結果と良好に一致することが分かる.このように,SBF試験は材料の疲労特性を評価する手法として有効であり,疲労寿命を予測できる可能性が示唆された.今後は,高温化に向けた試験手法の開発にも取り組む予定である.
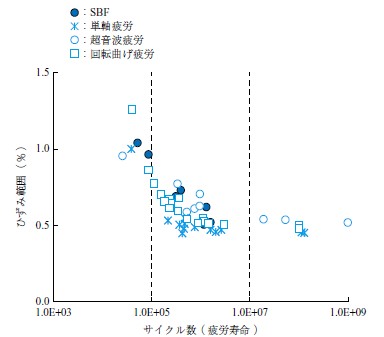
5. 結言
本稿では,SP試験を中心に微小サンプルを用いた材料評価技術を紹介した.SP試験においては,その試験片形状および負荷方式により破断部位が多軸状態になる.このことより,試験ごとに破断強度が異なるため,単軸試験結果と比較を行って相対的な寿命を算出する必要がある.しかしながら,構造物の余寿命評価においては,実機材料を用いる方が劣化精度を正確に知ることができる.そのために試験片加工が容易であり採取後の実機への影響も少ないSP試験をはじめとした微小サンプルを用いた材料評価技術は,構造部材の局所的な機械特性の評価として有効である.試験技術の適用性の検証,高度化,さらには試験法の標準化に向けて開発に取り組んでいく.
参考文献
(1) 三沢俊平:微小試験片材料評価技術の進歩,日本金属学会会報,Vol. 31,No. 11,1992 年11 月,pp. 1,008-1,009
(2) M. P. Manahan, A. S. Argon and O. K. Harling:The development of a miniaturized disk bend test for the determination of postirradiation mechanical properties,Journal of Nuclear Materials,Vol. 104,( 1981 ),pp. 1,545-1,550
(3) E. Fleury and J. S. Ha:Small punch tests to estimate the mechanical properties of steels for steam power plant: I. Mechanical strength,International Journal of Pressure Vessels and Piping,Vol. 75,Iss. 9,( 1998. 8 ),pp. 699-706
(4) C. Rodríguez, J. G. Cabezas, E. Cardenas, F. J. Belzunce and C. Betegón:Mechanical properties characterization of heat-affected zone using the small punch test,Welding Journal,Vol. 88,No. 9,( 2010. 1 ),pp. 188-192
(5) H. G. Svoboda, M. Duran, F. J. Belzunce and C. Rodríguez:Estimation of Local Mechanical Properties by Small Punch Test in Welded Joints of Maraging C250 Steel,Journal of Materials Engineering and Performance,( 2024. 7 )
(6) V. L. Giddings, S. M. Kurtz, C. W. Jewett, J. R. Foulds and A. A. Edidin:A small punch test technique for characterizing the elastic modulus and fracture behavior of PMMA bone cement used in total joint replacement,Biomaterials,Vol. 22,Iss. 13,( 2001. 7 ),pp. 1,875-1,881
(7) R. C. Hurst, R. J. Lancaster, S. P. Jeffs and M. R. Bache:The contribution of small punch testing towards the development of materials for aero-engine applications,Theoretical and Applied Fracture Mechanics,Vol. 86,Part A,( 2016. 12 ),pp. 69-77
(8) N. Kashaev, M. Horstmann, V. Ventzke, S. Riekehr and N. Huber:Comparative study of mechanical properties using standard and micro-specimens of base materials Inconel 625, Inconel 718 and Ti-6Al-4V,Journal of Materials Research and Technology,Vol. 2,Iss. 1,( 2013 ),pp. 43-47
(9) S. Nogami, W. Guan, M. Toyota, and A. Hasegawa:Fatigue life prediction of ferritic/martensitic steels based on universal slope equations and tensile properties obtained using small specimen,Fusion Engineering and Design,Vol. 125,( 2017. 12 ),pp. 330-336
(10) S. Nogami, A. Nishimura, E. Wakai, H. Tanigawa, T. Itoh and A. Hasegawa:Development of fatigue life evaluation method using small specimen,Journal of Nuclear Materials,Vol. 441,Iss. 1-3,( 2013. 10 ),pp. 125-132
(11) P. Zheng, R. Chen, H. Liu, J. Chen, Z. Zhang, X. Liu, and Y. Shen:On the standards and practices for miniaturized tensile test – A review,Fusion Engineering and Design,Vol. 161,( 2020. 12 )
(12) S. Arunkumar:A Review of Indentation Theory,Materials Today: Proceedings,Vol. 5,Iss. 11,Part 3,( 2018 ),pp. 23,664-23,673
(13) X. Mao and H. Takahashi:Development of a further-miniaturized specimen of 3 mm diameter for tem disk ( ø3 mm ) small punch tests,Journal of Nuclear Materials,Vol. 150,Iss. 1,( 1987. 9 ),pp. 42-52
(14) E. N. Campitelli, P. Spätig, R. Bonadé, W. Hoffelner and M. Victoria:Assessment of the constitutive properties from small ball punch test: experiment and modeling,Journal of Nuclear Materials,Vol. 335,Iss. 3,( 2004. 12 ),pp. 366-378
(15) B. Ule, T. Šuštar, F. Dobeš, K. Milička, V. Bicego, S. Tettamanti, K. Maile, C. Schwarzkopf, M. P. Whelan, R. H. Kozlowski and J. Klaput:Small punch test method assessment for the determination of the residual creep life of service exposed components: outcomes from an interlaboratory exercise,Nuclear Engineering and Design,Vol. 192,Iss. 1,( 1999. 8 ),pp. 1-11
(16) S. Komazaki, R. Jojima, N. Muraoka, S. Nogami, M. Kamaya, C. Hisaka, M. Fujiwara and A. Nitta:Development of small bulge fatigue testing technique using small disk-type specimen,Fatigue & Fracture of Engineering Materials & Structures,Vol. 43,Iss. 3,( 2020. 3 ),pp. 444-456
(17) E. Altstadt, H. E. Ge, V. Kuksenko, M. Serrano, M. Houska, M. Lasan, M. Bruchhausen, J. -M. Lapetite and Y. Dai:Critical evaluation of the small punch test as a screening procedure for mechanical properties,Journal of Nuclear Materials,Vol. 472,( 2016. 4 ),pp. 186-195
(18) T. E. García, C. Rodríguez, F. J. Belzunce and C. Suárez:Estimation of the mechanical properties of metallic materials by means of the small punch test,Journal of Alloys and Compounds,Vol. 582,( 2014. 1 ),pp. 708-717
(19) M. Abendroth and S. Soltysiak:Assessment of Material Properties by Means of the Small Punch Test,Recent Trends in Fracture and Damage Mechanics,Springer,( 2016 ),pp. 127-157
(20) S. Rasche and M. Kuna:Improved small punch testing and parameter identification of ductile to brittle materials,International Journal of Pressure Vessels and Piping,Vol. 125,( 2015. 1 ),pp. 23-34
(21) M. Abendroth and M. Kuna:Determination of deformation and failure properties of ductile materials by means of the small punch test and neural networks,Computational Materials Science,Vol. 28,Iss. 3-4,( 2003. 11 ),pp. 633-644
(22) 大田祐太朗,中原庸裕,榊原洋平:スモールパンチ試験を用いた微小サンプルによる熱可塑性樹脂と熱硬化性樹脂の引張特性評価,材料,Vol. 72,No. 8,2023 年8 月,pp. 599-605
(23) J. C. Chica, P. M. B. Díez and M. P. Calzada:Improved correlation for elastic modulus prediction of metallic materials in the Small Punch Test,International Journal of Mechanical Sciences,Vol. 134,( 2017. 12 ),pp. 112-122
(24) J. M. Alegre, R. Lacalle, I. I. Cuesta and J. A. Álvarez:Different methodologies to obtain the fracture properties of metallic materials using pre-notched small punch test specimens,Theoretical and Applied Fracture Mechanics,Vol. 86,Part A,( 2016. 12 ),pp. 11-18
(25) I. I. Cuesta, A. Willig, A. Díaz, E. Martínez-Pañeda and J. M. Alegre:Pre-notched dog bone small punch specimens for the estimation of fracture properties,Engineering Failure Analysis,Vol. 96,( 2019. 2 ),pp. 236-240
(26) 公益社団法人日本材料学会:― 高温機器の余寿命診断のための ― 微小サンプルクリープ試験法標準,2012 年
(27) 久布白圭司,吉澤廣喜:2.25Cr-1Mo鋼溶接継手のスモールパンチクリープ寿命評価,IHI技報,Vol. 47,No. 4,2007 年12 月,pp. 153-156
(28) 駒崎慎一,小畑啓介,屋口正次,金井雅之,友部真人,熊田明裕:スモールパンチ試験法による9Cr鋼ボイラ配管のクリープ特性評価,材料,Vol. 70,No. 2,2021 年2 月,pp. 125-132
(29) P. Dymáček, Y. Li, F. Dobeš, and P. Stevens:New approach to determine uniaxial creep properties from small punch creep curves,Materials at High Temperatures,Vol. 36,Iss. 2,( 2018. 7 ),pp. 157–164
(30) S. Holmström, Y. Li, P. Dymacek, E. Vacchieri, S. P. Jeffs, R. J. Lancaster, D. Omacht, Z. Kubon, E. Anelli, J. Rantala, A. Tonti, S. Komazaki, Naveena, M. Bruchhausen, R. C. Hurst, P. Hähner, M. Richardson and D. Andres:Creep strength and minimum strain rate estimation from Small Punch Creep tests,Materials Science and Engineering: A,Vol. 731,( 2018. 7 ),pp. 161-172
(31) 吉崎幸一朗,駒崎慎一,釜谷昌幸,野上修平,村岡南那,日坂知明,新田明人:スモールバルジ疲労試験技術の開発,日本機械学会M&M材料力学カンファレンス講演論文集,2018 年12 月