JAXA F7エンジンでの1400℃級CMCシュラウド実証試験
渡邉文章,山中彰平,中村武志
渡邉 文章 航空・宇宙・防衛事業領域技術開発センターエンジン技術部 主査
山中 彰平 航空・宇宙・防衛事業領域技術開発センターエンジン技術部 主査
中村 武志 航空・宇宙・防衛事業領域技術開発センター材料技術部 主幹
航空機に関して日本国内で研究・開発された独自技術の適用性についてエンジン実機を用いて実証するため,国立研究開発法人宇宙航空研究開発機構 (JAXA) に株式会社IHIが設計・製造を担当したF7-10エンジンが導入された.F7-10エンジンは防衛装備庁 (ATLA) によってP-1固定翼哨戒機用に開発された高バイパス比ターボファンエンジンである.IHIは,国立研究開発法人新エネルギー・産業技術総合開発機構 (NEDO) の委託を受け,1 400℃級の耐熱性を有するセラミック基複合材料 (CMC) シュラウドを研究・開発し,JAXAと共同でF7-10エンジン (以下,JAXA F7エンジン) に搭載し,実証試験を行って,エンジン実環境における健全性を確認した.
Japan Aerospace Exploration Agency (JAXA) introduced F7-10 turbo fan engine to demonstrate new aeroengine technologies developed in Japan by producing their usage environment with an actual engine. The engine is a high bypass ratio turbo fan engine developed by Acquisition, Technology & Logistics Agency (ATLA) for P-1 maritime patrol aircraft. In the course of its development, IHI designed and manufactured it. Commissioned by New Energy and Industrial Technology Development Organization (NEDO) , IHI developed a ceramic matrix composite (CMC) shroud which has 1 400°C class temperature capability and confirmed its soundness when mounted in the actual engine through a demonstration test conducted jointly with JAXA.
1. 緒言
近年,CO2削減の社会的要請はますます高まっており,航空機用エンジンの燃費改善への取組みは,より重要性を増している.燃費改善の実現に向けて世界各国のみならず日本でも独自に新技術の研究・開発が行われている.新機種の開発には非常に長い期間を要し,多額の費用も掛かる.特に航空機用エンジンには高い信頼性が求められるため,新技術の導入に際しては,事前にさまざまな試験などによって適用性を実証し,リスクを十分に低減しておく必要がある.エンジンを構成する各部品は,エンジン特有の温度・荷重・振動などの複合環境下において使用される.したがって,これらを総合的に実証できるエンジン実環境での試験が不可欠である.
日本国内で研究・開発された独自技術を実証するため,JAXAに技術実証試験用として第1図に示すJAXA F7エンジンが2019年に導入された(1).JAXA F7エンジンはATLAによってP-1固定翼哨戒機用に開発された高バイパス比ターボファンエンジンであり,IHIが設計・製造を担当した.ATLAとIHIの間でJAXAへの販売に向けた民間転用契約が締結されて,2019年にJAXAに導入された.JAXA F7エンジンの活用により,日本における新技術の研究・開発がよりいっそう進展していくことが期待されている.
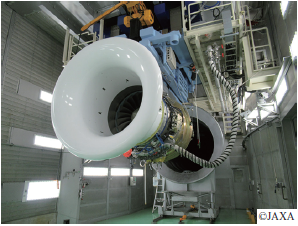
第1図 JAXA F7 エンジン
Fig. 1 JAXA F7 engine
エンジン燃費改善に有効な方法として,高圧タービン部品の耐熱温度を上昇させて冷却空気量を低減したり,タービン入口温度を上昇させたりすることがある.従来は高圧タービン用材料としてニッケル基などの超合金が用いられてきたが,近年さらなる耐熱性向上を目指し,セラミック基複合材料 (Ceramic Matrix Composite:CMC) が実用化され始めている.IHIでは数十年にわたってCMC材料および部品の研究・開発を行ってきた(2).2015年からはNEDOの委託を受け,世界最高レベルである1 400℃級の耐熱温度を有するCMC材料と,この材料を用いた高圧タービンシュラウドを研究・開発し,2021年にJAXA F7エンジンに搭載して実証試験を行った.本稿では,1 400℃級CMCシュラウドの研究・開発の概要とエンジン試験結果について述べる.
2. CMC材料システム
一般に,セラミック材料は金属材料に比べて軽量で耐熱性が高いという特徴があるが,ぜい性的な破壊挙動を示すため,高い信頼性が求められる航空機用エンジン部品への適用は困難であった.CMCはセラミック材料をセラミック繊維で強化した複合材である.CMCは材料内部の微小な亀裂の伝ぱが強化繊維によって妨げられるため,材料全体としては金属材料のような延性的な挙動を示し,航空機用エンジン部品への適用が可能となる.
IHIはNEDOの委託を受け,1 400℃級での使用に耐え得る材料を目指し,次のような構成の材料システムを研究・開発した.SiC (炭化けい素) 繊維はNGSアドバンストファイバー株式会社のHi-Nicalon Type-S,繊維界面コーティングはBN (窒化ほう素) ,繊維構造として直交三次元織物を採用した.SiCマトリックスは気相含浸 (Chemical Vapor Infiltration:CVI) 法を,希土類シリケートベースのマトリックスは液相含浸 (Melt Infiltration:MI) 法を用いたハイブリッド形式で作製した.部品形状に成形した後,主流ガスに曝される面には,希土類シリケートをベースとしたアンダーコートとハフニアをベースとしたトップコートで構成される耐環境コーティング (Environmental Barrier Coating:EBC) を施した.
高圧タービンシュラウドの設計に必要なCMC構成材料の各種データは,1 400℃までの材料試験を行い,取得した.
3. CMCシュラウド設計
IHIはNEDOの委託を受け,1 400℃級CMCを用いた実証試験用のシュラウドを研究・開発した.第2図にエンジン全体の断面図を示す.本稿で述べる実証試験では,高圧タービンの1段シュラウドを対象とした.タービンシュラウドはタービン動翼の外径側に位置し,主流ガスの流路面を形成するという機能をもつ.第3図に示すように,タービンシュラウドは高温高圧の燃焼ガスに曝され,繰返し作用する温度,温度差,圧力差,振動,タービン動翼との接触 (ラビング) による衝撃を受けるが,これらに対して要求寿命を満足するよう設計されなければならない.
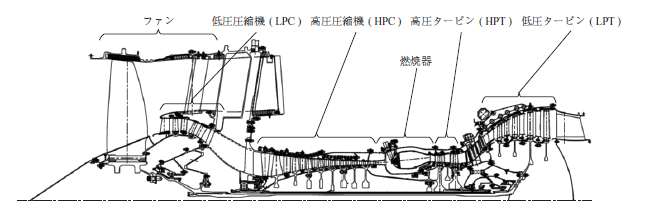
Fig. 2 Cross section of JAXA F7 engine (3)
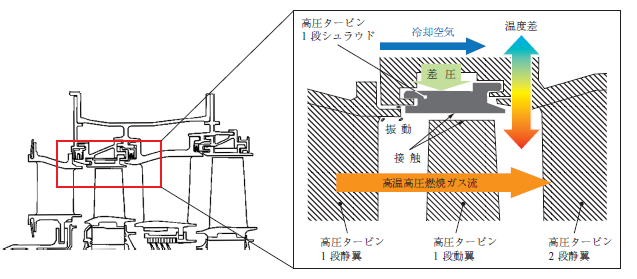
Fig. 3 Operating environment of high pressure turbine shroud
上記の要求を満たすように設計したCMCシュラウド形状を第4図に示す.伝熱解析結果および応力解析結果を第5図,第6図に示す.解析の結果,設計上は最大温度が1 355℃であり,強度的にエンジン試験条件に対して余裕があることを確認した.
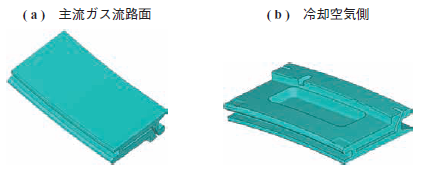
Fig. 4 CMC shroud geometry
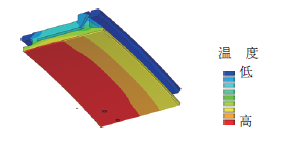
Fig. 5 Estimated temperature distribution of CMC shroud
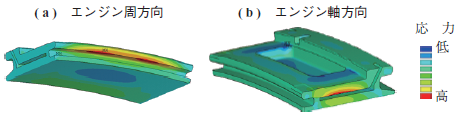
Fig. 6 Estimated stress distribution of CMC shroud
4. 要素試験・部品試験
IHIはNEDOの委託を受けた1 400℃級CMCシュラウドの研究・開発として,エンジン試験前に以下の①~④の要素試験および部品試験を実施した.
①平板試験片による高温ガス流曝露試験
②動翼との接触状況を模擬したラビング試験
③シュラウド支持部であるフック部の強度試験
④シュラウドの熱サイクル試験
このうち,③と④の試験概要について述べる.
4.1 フック部強度試験
シュラウド支持部であるフック部の強度健全性を確認するために,実際のシュラウドフック部の形状,エンジン温度,負荷応力状態を模擬した強度試験を実施した.試験温度は,伝熱解析によって予想したエンジン試験におけるフック部の温度である920℃とした.フック部強度試験の試験形態を第7図に示す.試験条件と結果の一覧を第1表に示す.静的破壊試験の結果,供試体2体の破壊荷重は約2 500 Nであった.疲労試験では,エンジン試験で発生する荷重に相当する試験荷重810 Nで2体の供試体が1 000サイクルで破壊せず,さらにその1.5倍以上の荷重1 270 Nを負荷した別の2体の試験についても1 000サイクルで破壊しなかった.各供試体には段階的に負荷をかけていき,最終的に破壊するまで疲労試験を実施した.代表として供試体4の破壊後の状態を第8図に示す.供試体4は試験荷重1 490 N,13 443サイクルで破壊した.以上の試験結果より,シュラウドフック部は十分な強度を有していることが確認された.
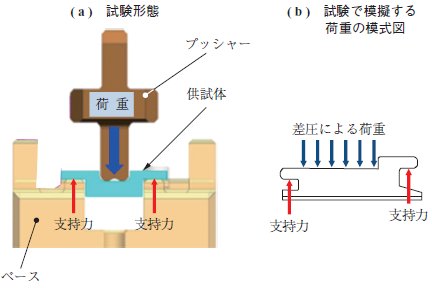
Fig. 7 Configuration of hook strength test
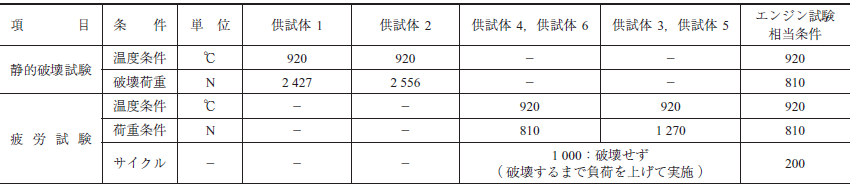
Table 1 Conditions and results of hook strength test
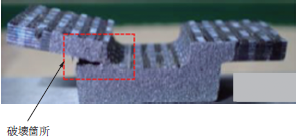
第8図 試験後の供試体4
Fig. 8 Appearance of specimen No. 4 after the test
4.2 シュラウド実体の熱サイクル試験
実部品の熱サイクルに対する健全性を確認するために,ガスバーナーを用いて繰返しシュラウドを加熱する試験を実施した.供試したCMCシュラウドを第9図に,試験形態を第10図に示す.CMCシュラウドの主流ガス流路面の最高温度が1 400℃となるように加熱し,約2分保持して放熱するサイクルを繰返し与えた.1 000サイクル後の供試体,および,2 000サイクル後の供試体を第11図に示す.試験後の供試体にはEBCの局所的な剥離以外の損傷は確認されなかった.EBCの剥離は局所的なものであり,エンジン試験で発生したとしても部品の機能に影響するものではないため,エンジン試験に進むことは問題ないと判断した.
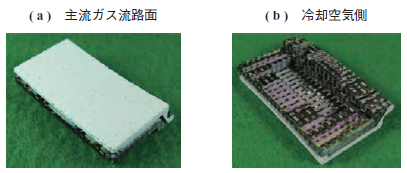
Fig. 9 Appearance of CMC shroud before the test
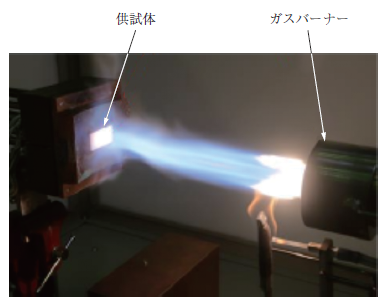
Fig. 10 Configuration of cyclic thermal test
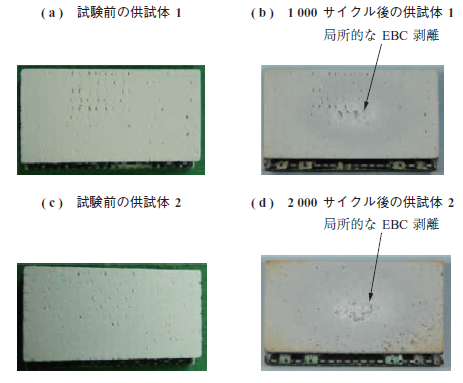
Fig. 11 Comparison of CMC shroud after the test with before the test
5. エンジン試験
IHIはNEDOの助成を受け,JAXAと共同で,1 400℃級CMCシュラウドをJAXA F7エンジンに搭載し,実証試験を実施した.JAXA F7エンジンに搭載したCMCシュラウドを第12図に示す.全周32個ある高圧タービン1段シュラウドのうち8個を,CMCシュラウドに組み替えてエンジン試験を実施した.タービンケースに組み付けたCMCシュラウドを第13図に示す.
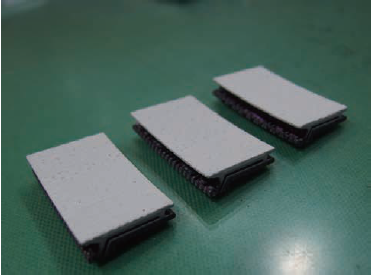
Fig. 12 CMC shrouds before the engine test
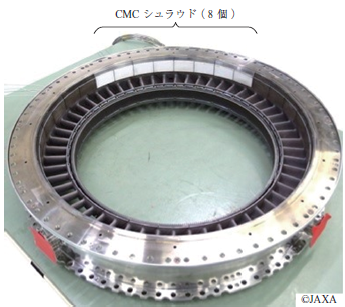
Fig. 13 CMC shrouds assembled into a turbine case
エンジン試験は2021年6月から7月にかけてJAXA調布航空宇宙センター (東京) の地上エンジン運転試験設備で行った.高出力状態での保持,加減速運転を含めた総運転時間は約80時間であった.試験条件の概要を以下に示す.
- 総運転時間:約80時間
- 高出力状態保持時間:37時間
- 始動回数:39回
- アイドルから高出力状態のサイクル数:227
- 高出力状態でのシュラウド部主流温度:1 300℃以上
おおむね10時間運転ごとにボアスコープによる観察を実施し,CMCシュラウドおよび周辺部品に異常がないことを確認しながら運転試験を進めていった.運転期間中にボアスコープを観察したときのCMCシュラウドの状態を第14図に示す.
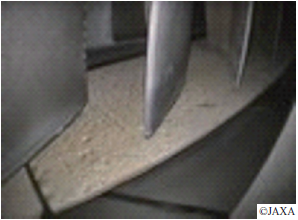
Fig. 14 CMC shroud observed by a borescope
エンジン試験終了後にCMCシュラウドを取り出して確認を行った.第15図,第16図に試験後のCMCシュラウドの外観を示す.試験後にシュラウドや周辺部品の脱落,固着などはなく,組付け状態はエンジン試験前と同様の状態であった.外観観察の主な結果を以下に示す.
- 主流ガス流路面のEBCに剥離などの損傷は確認されなかった.
- シュラウド全体に茶褐色の変色が見られ,成分分析の結果から主流ガスに含まれるCa,Mg,Al,Feなどが付着したものと判断した.
- フック部などの隣接部品との接触部に顕著な摩耗は見られなかった.
- シュラウド全体に焼損や欠け,割れなどの損傷は確認されなかった.
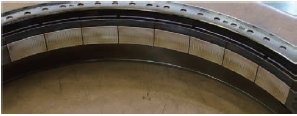
Fig. 15 CMC shrouds with turbine case after the engine test
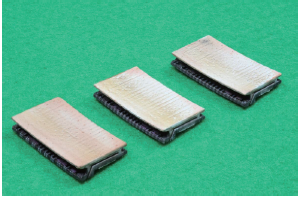
Fig. 16 CMC shrouds after the engine test
エンジン試験後のCMCシュラウドを切断して内部状態の変化を確認した.第17図にEBC部について切断面を拡大観察した結果を示す.第17図-(a)に示すようにCMC基材とアンダーコートの境界にクラックが確認された.第17図-(b)に示すようにトップコートにもクラックが確認された.これらのクラックはエンジン試験において発生した可能性があると判断している.CMC基材内部のミクロ構造についても拡大観察した.第18図に部品表面付近の切断面を拡大観察した結果を示す.その結果,部品表面付近の一部を除いて,内部ミクロ構造に有意な変化は確認されなかった.部品表面付近の一部では,繊維界面のBNコーティングの酸化が確認された.
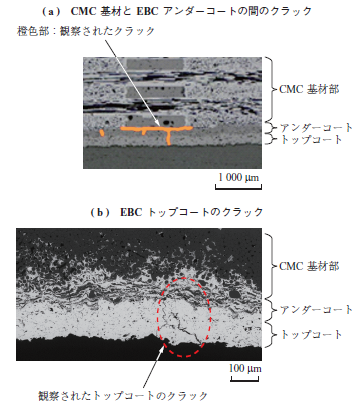
Fig. 17 Result of microscopic observation in cross section including EBC area
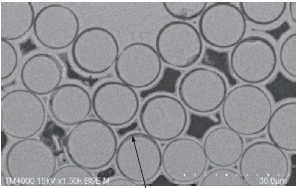
Fig. 18 Result of microscopic observation in cross section near the surface
以上のようにエンジン試験後のCMCシュラウドの状態を確認した結果,外観や内部組織に変化は見られたものの,部品の機能に影響を及ぼすものではなく,継続使用できる状態と判断した.
本エンジン試験によって,1 400℃級CMCシュラウドのエンジン実環境での健全性が実証された.
6. 結言
1 400℃級CMCシュラウドの研究・開発の概要とJAXA F7エンジンによるCMCシュラウドの実証試験について述べた.開発した1 400℃級CMC材料のタービンシュラウドについて,JAXA F7エンジンを活用することで部品単体での実証から一歩進んでエンジン実環境で実証することができた.実用化に向けて,今後は長時間耐久性の確認,製造性の改善に取り組んでいく.
CMCシュラウドに限らず,今後もJAXA F7エンジンを活用することで日本独自の技術開発が進展することが予想され,IHIとしても新技術開発によって航空機用エンジンのさらなる燃費改善,CO2削減に貢献していく.
- ― 謝 辞 ―
- JAXA F7エンジン導入は,国立研究開発法人宇宙航空研究開発機構 (JAXA) および防衛装備庁 (ATLA) の多大なるご尽力により実現したものである.1 400℃級CMCシュラウド開発およびJAXA F7エンジン試験は,国立研究開発法人新エネルギー・産業技術総合開発機構 (NEDO) より委託を受けて2015年から2019年に実施した研究成果,助成を受けて2020年から2022年に実施した研究成果,およびJAXAとの共同研究による成果である.本稿に述べたCMCシュラウド実証試験は多くの関係各位のご支援により実現したものであり,ここに記し,深く感謝いたします.
参考文献
- 国立研究開発法人宇宙航空研究開発機構ホームページ:航空エンジン技術の実証に向けたF7-10エンジンの運用開始について,https://www.jaxa.jp/press/2020/12/20201224-1_j.html, (参照2022. 3. 7)
- 中村武志,岡 尚志,今成邦之,篠原健一,石崎雅人:航空機エンジン用CMCタービン部品の開発,IHI技報,Vol. 53,No. 4,2013年12月,pp. 34-37(1.5MB)
- 坪本 卓,森脇暢彦:F7-10エンジンの設計,IHI技報,Vol. 57,No. 1,2017年3月,pp. 30-38(4.3MB)