プラント稼働データを活用した運転効率向上手法
茂木 悠佑,松田 一真,鈴木 由宇,河野 幸弘
茂木 悠佑 高度情報マネジメント統括本部DX推進部 主査
松田 一真 高度情報マネジメント統括本部DX推進部
鈴木 由宇 高度情報マネジメント統括本部DX推進部 グループ長
河野 幸弘 高度情報マネジメント統括本部 技監
IHIでは,設備の稼働データの活用に取り組んでおり,この一環としてMT法 ( Mahalanobis Taguchi method ) を用いたデータ分析も実施している.一般的なMT法は,正常状態は一つの群(単位空間)を成すという前提のもと,「正常」と「正常以外」の1 クラス分類を行う手法である.このため,設備の動作モードや外気温など動作環境の変化によって「正常」状態が変化する場合は,誤検知や未検知を生じることがある.この問題に対応するため,時々刻々と動作環境が変化する設備であっても,その環境に適した正常データ群を動的に選ぶことによって高い精度で分類を行うことができる動的単位空間を用いたMT法(以下,動的MT法)を開発した.本稿では,この動的MT法を応用し,発電プラントや生産設備の運転効率の向上を実現する手法の概要と模擬データを用いた検証結果を紹介する.
At IHI, we are working on leveraging operational data from equipment, and as part of this effort, we are also conducting data analysis using the Mahalanobis Taguchi (MT) method. The conventional MT method is predicated on the assumption that the normal state forms a single group (unit space), and it conducts a one-class classification to distinguish between “normal” and “abnormal” states. However, this approach may lead to false positives or missed detections when the “normal” state changes due to variations in operating modes, ambient temperature, or other environmental factors. To address this issue, a “Dynamic Unit Space MT Method” (hereinafter called “the dynamic MT method”) has been developed, which dynamically selects the appropriate normal data group according to the changing operating environment, thereby achieving high-accuracy classification even for equipment under fluctuating operating conditions. This paper outlines the application of the dynamic MT method to improve the operational efficiency of power plants and production facilities, and presents validation results using simulated data.
1. 緒言
IHIが製造する発電所や生産設備などの産業インフラには,運転効率を上げたり,環境への影響や運転コストを減らしたりすることがますます求められている.これらの産業インフラでは,運転効率を上げるために操作を変更する場合でも,設備の安定した運用を保つことが前提となる.
運転操作指示に機械学習を利用する制御システムも多いが,こういった背景から運転操作を変更しても安定運用を崩さないことの説明性が要求される.近年は説明可能な人工知能 ( XAI ) などの登場でこれらの要求に対応するものが整備されつつあるものの,XAIは発展途上であり,上記のような制御システムにおける導入障壁の一要因となっている.一方,説明性の高い物理モデルを用いる手法やグレーボックスモデリングなどのように物理モデルと統計モデルを統合し精度を向上させるアプローチもある.しかし,発電プラントのように,設置条件や補器類など考慮すべき要素が多く複雑性の高い設備について,物理モデルを精密に構築するコストが高く,同じく導入障壁となっている.このように,重要産業インフラの運転効率を向上させる場合には,判断結果に対して説明性を持ち,物理モデルのように設計知見を盛り込めつつも,構築コストは低い手法が求められる.
今回この問題に対応するためにMT法 ( Mahalanobis Taguchi method ) を発展させた動的MT法をプラントの稼働データに適用することによって,プラントの運転効率の向上を図った.本稿では,まずMT法および動的MT法の違いについて触れ,次に提案手法について説明する.その後,模擬データによる提案手法の検証結果を示す.
2. MT法および動的MT法
2.1 M T 法
MT法は機械学習手法の一つであり,多くのセンサを持つ設備から得られる多次元情報に対する異常診断を効果的に行うことができる.単位空間と呼ばれる設備の正常状態時のデータ群を基準とし,診断時の稼働データがその単位空間から離れている場合に異常と判断する.その乖離(かいり)度合いを,単位空間の分布を考慮して算出されるマハラノビス距離(Mahalanobis Distance,以下,MD値)を使って測定する ( 1 ),( 2 ).MD値が大きい場合は単位空間から離れている状態(異常状態)と判断する.各次元は,単位空間におけるばらつきで正規化されているため,単位系が異なるセンサ値のデータセットであっても意味のある単一の距離(MD値)を算出することができる.第1図に二次元の場合の,MT法による診断の概念図を示す.第1図において,黒い丸印は単位空間を構成するデータであり,赤いバツ印は診断対象の稼働データを表す.両者を結ぶ青い矢印はMD値を表しており,楕円(だえん)はMD値の等高線を示している.
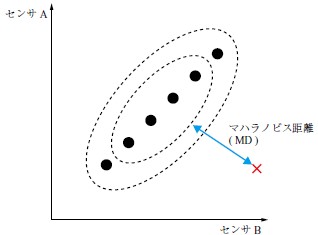
MT法による診断は,多次元の計測項目を一次元(MD値)に集約するため,「正常」「異常」の判定が容易,複数の計測項目間における相関関係の崩れによる異常も検知可能,正常状態のみを学習するため発生頻度の低い異常も検知可能などのメリットがある.
一方で設備の動作環境(外部環境や運転条件など)によって正常状態自体が変化する場合は誤検知や未検知が発生してしまうことがある.動作環境によって異なる正常状態のクラスタ一つ一つに単位空間を事前に割り当て,複数の単位空間で全ての正常状態を表現することで,このような動作環境による正常状態の変化に対応する手法も考えられる.しかし,正常状態が連続的に変化する場合や,正常状態を表すために必要なクラスタの数が多い場合には実用上の対応が難しい.そこで,2. 2 節に示す動的MT法を提案した.
2.2 動的MT法
動的MT法では,さまざまな動作環境下の正常状態のデータを事前に準備しておき,診断ごとにその設備の動作環境の近傍点のデータのみを都度抽出して単位空間を生成する.第2図に動的単位空間の概念図を示す.本稿ではこの各時点で生成される単位空間を動的単位空間と呼ぶ.第2図に示すように,赤いバツ印で示される時刻T = 2の稼働データを診断する際は,時刻T = 2に生成された動的単位空間をMD値の計算に用いる.
あらかじめ固定された単位空間構成データ群を利用する通常のMT法と異なり,動作環境が変化しても,診断時点ごとに動作環境近傍点のデータ群で単位空間を都度生成するため,正常状態が変化しても適切に診断することができる ( 3 ) ~ ( 6 ).
なお,動的単位空間を生成するためのデータ群の選定には,第2図中のセンサA,センサBのように単位空間を構成する項目ではなく,対象設備の動作環境に関する項目(外気温,大気圧,設定出力など)を使用する.選定条件(動作環境条件)は,対象設備の設計知見を活用して,使用する項目や近傍点とみなす値の範囲などを設定する.
動的単位空間の生成,および診断過程が明確であり,動作環境が変化する複雑な設備でも判断結果の説明性が高い.
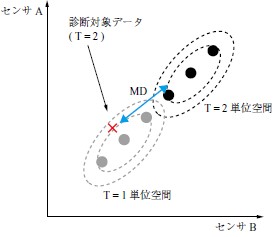
3. 動的MT法による運転効率の向上
3.1 動的単位空間の定義方法
プラントの稼働データから運転効率の向上を図る手法を提案する.異常診断の場合と同様にプラントの動作環境の影響を考慮する必要があるため,2 章で説明した動的単位空間の考えを用いる.
運転効率の指標として,ここでは熱効率を例に取り上げる.熱効率の改善幅の目標を定める事前準備フェーズと,診断時点ごとに熱効率の改善策を得る通常の診断フェーズに分けて説明する.第1表に事前準備フェーズ,診断フェーズで対象とするプラント環境条件,診断対象項目,処理の目的について示す.
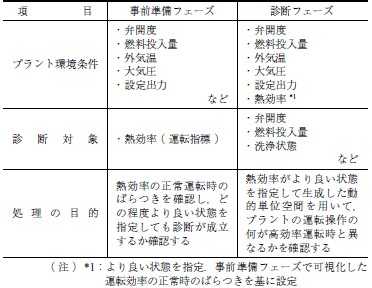
診断フェーズでの動的単位空間を構成する診断対象項目は,異常診断ではプラントの内部状態であるが,運転効率向上の場合は,弁開度や燃料投入量,熱効率を改善させるための洗浄など,プラントの運転操作に関する項目を用いる.プラント環境条件は,異常診断の場合と同様に対象設備の設計知見に基づき,プラントの動作を定める外部環境や運転条件などを設定する.ただし,熱効率を新たに項目に追加することとし,近傍点とみなす値の範囲は,診断時点の熱効率よりも高い範囲を設定する.この範囲が熱効率の改善幅としての目標値となる.この改善幅の設定は,望大特性となるため基本的には大きいほど好ましい.しかし,学習用データセットに存在しないほど高い値を指定すると単位空間が生成できなくなるため,学習用データセットの分布を基に値の範囲を適切に設定する必要がある.さらに,動作環境の変化の影響も考慮して設定する必要がある.そこで,類似の動作環境下で熱効率の値が通常どの程度の分布域を持っているかをあらかじめ把握するために,事前準備フェーズを用意する.
事前準備フェーズでは,プラントの環境条件は熱効率を除いて診断フェーズと同じである.このフェーズにおいて,熱効率のみが動的単位空間を構成する診断対象項目となる.動的単位空間内での熱効率の値を調べることにより,類似する動作環境条件下で熱効率の取り得る値の範囲が分かるため,この値の範囲を基に適切な改善幅を定めることができる.
診断フェーズにおいて,動作環境条件に熱効率を加え,動作環境近傍における熱効率の改善幅を設定する.この設定により,診断時点と類似の動作環境下で,かつ診断時点より熱効率が高く目標とすべきデータ群を動的単位空間として抽出できるようになる.
3.2 MD値による運転効率の向上対象期間の選定
第3図に熱効率改善のベクトル量を示す.第3図のXY座標は運転操作量を表しており,Z軸に熱効率の値を表示している.青色部分は全学習データ,黒丸の点は診断時点のデータ,緑色部分は抽出された動的単位空間内のデータをそれぞれ表している.黒丸のZより緑色部分のZの値が大きくなっていることから分かるように,緑色部分は類似の動作環境下で診断時点よりも熱効率が高いことが分かる.すなわち,青い矢印は,診断時点から熱効率を向上させるために必要な運転操作の修正量を表している.
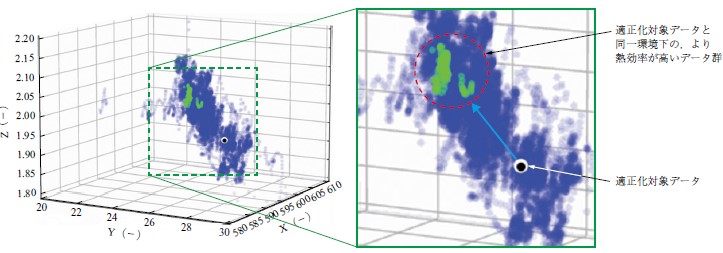
ただしプラントの運転操作項目は非常に多いため,第3図のように少ない次元数で表せることはほとんどなく,効率的に熱効率の改善可能な運転区間を判断することが難しい.そこで,MT法を用いて診断対象の各データに対して 算出したMD値を利用することとした.
MD値が高い運転区間では,類似した動作環境において,熱効率がより良い状態が存在し,さらに,運転操作量に大きな違いがあったことを示しており,運転操作量の修正で熱効率の改善の可能性が高い運転区間と考えられる.逆に,MD値が低い運転区間では,運転操作量に違いがあまり見られない区間であり,外気温や気象状況など他の外的要因によって熱効率が変化したと想定されるため,運転操作の修正での改善効果は期待できない運転中の一定区間(以降,運転区間)と考えられる.
MD値は一次元量であり,動的単位空間内のデータからMD値が高いデータを抽出することによって熱効率向上が可能な期間の選定を比較的容易に行うことができる.
3.3 貢献度による修正対象項目の確認
3. 2 節で示した方法で,MD値の大小のみで熱効率の改善可能性がある一定期間を検出することができるが,その一方で,MD値は多次元の情報を一次元に集約した値であるため,熱効率の差異に大きく関与している運転操作項目をそれだけでは明らかにはできない.
そこで,MT法における貢献度を利用することとした.貢献度は,各項目のMD値に寄与している度合いを示す値であるため,MD値が高い期間において,貢献度が高い運転操作項目を調べることで,熱効率に大きく関与している可能性の高い運転操作項目を容易に確認することができる.第4図に,改善対象運転操作項目の抽出の例を示す.第4図 - ( a ) に示されたMD値が高い874 ~ 886の運転区間において,- ( b ) に示された貢献度が高い緑色で表された運転操作項目である,MD 貢献度_24の操作が最も熱効率の改善に寄与する可能性が高い.
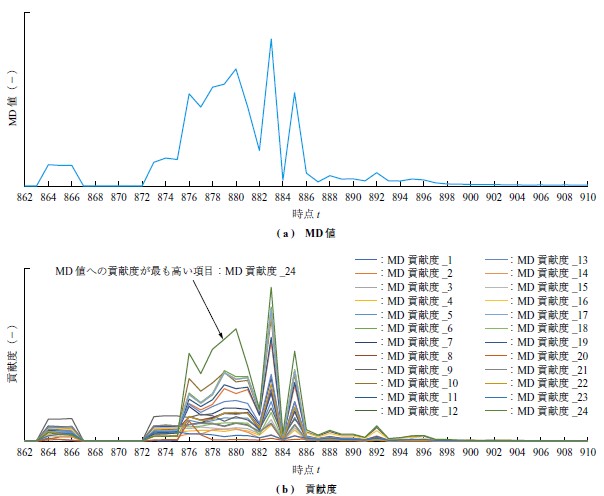
第5図に改善対象項目の修正量の可視化図を示す.これは,第4図で貢献度が高かった運転操作項目の動的単位空間内の分布(平均値と± 3σ)を緑色で,診断時点での計測値を黄色で時系列比較図としたものである.第5図から分かるように,表示されている運転操作項目の値の範囲は,学習フェーズ内で熱効率が目標となる高い値であった運転区間のものと診断フェーズ時点のもので大きく異なっており,この運転操作項目の値を見直すことで,運転効率向上が期待できる.
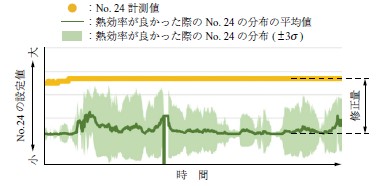
運転効率向上の対象期間や対象となる運転操作項目を選定する際には,MD値が時系列的に連続して高い運転区間において貢献度が連続して高い運転操作項目を選ぶことが望ましい.このような運転区間においては,プラントはほぼ定常状態であると推定されるため,動的単位空間を構成する診断対象項目が今回のように各時点のみの運転操作量だとしても,診断結果にそれほど大きな影響は生じないと想定される.
一方,プラントの内部状態は一般に,各時点の運転操作量だけではなく,過去の運転操作量にも影響を受けるため,プラントが過渡状態にあるような場合には,影響を与える過去の運転操作量も動的単位空間を構成する診断対象項目に追加するなどの留意が必要である.
本手法では,導き出される運転操作項目の修正量とその際に予想される効率改善量は,学習データセットにおいて実際に存在するデータから求めているため,実現の可能性が高いという点は大きなメリットである.
4. 検証
4.1 対象データ
模擬データを用いて,3 章で提案した手法の検証を実施した.今回は超臨界圧ボイラの時系列稼働データに関するオープンデータセット ( 7 ) を用いた.
主要な計測項目はGENERATOR MW(発電機出力),TOTAL COAL FLOW BEF CAL CORR(総石炭流量),TOTAL AIR FLOW ( t/h ) (総空気流量 ( t/h ) ),AA ( L ) CRNR 1 AA DMPR FB(ダンパ開度フィードバック)など,プラントの内部状態,動作環境,および運転操作を示す115 項目である.データ数は17,280 行(観測点数)であり,全て設備が正常な状態で計測されている.このうち,15,840 行を学習用(動的単位空間の抽出元)データ,1,440行を運転効率の向上のための検証用データとした.検証用データはランダムサンプリングはせず,元の時間的連続性を維持したままデータを分割した.
4.2 運転効率指標の計算
ボイラにおける熱損失の大部分は,排ガスによる損失熱量が占める.この熱損失は排ガスの比熱の計算が必要で,今回のオープンデータセットでは計算に必要な情報が得られないため,本稿では簡略し,( 1 ) 式を運転効率の指標として利用した(以下,G_C_RATIO).
G_C_RATIO = 発電機出力/総給炭量 ( MW·h/t ) …………………… ( 1 )
4.3 動的MT法の設定条件
動作環境近傍点を抽出するために使用する動作環境条件項目として,ボイラの設計知見に基づいて以下の第2表に示す項目を選定した.
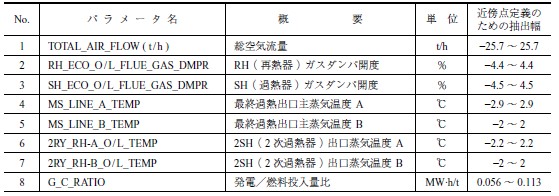
動作環境条件項目のうち,No. 1 ~7までは,プラント自体の動作環境の近傍点のデータを抽出するため,その抽出幅は± 同一の幅を設定する.この抽出幅は,設計的見地から設定した.
一方,No. 8のG_C_RATIOの抽出幅は,3. 1 節で述べたように,事前抽出フェーズで確認する類似する動作環境下での分布域を基にして,プラス側の範囲のみを使用する検証用データの値に対して+ 0.056以上から+ 0.113以下の範囲を抽出した.これは,検証データに対して,学習用データ群から動作環境が類似しており,かつ給炭量1 t当たり0.056 MW·h/t以上良かったデータのみを抽出して動的単位空間を生成し,検証データとの差異を比較することを意味している.
4.4 運転効率指標の抽出幅の設定方法
前述のG_C_RATIOの抽出幅は,事前抽出フェーズにおいて得られたG_C_RATIOの分布域から設定した.第6図に運転指標の改善幅設定を示す.第6図の分布幅は,標準偏差 ( 1σ ) を示している.類似した動作環境条件下での結果であることから学習データと同様の分布を持つと想定される検証データも正規分布にのっとると仮定し,実データが存在する水準で改善可能な運転効率指標として,+ 1σ ~ + 2σ ( 0.056 ~ 0.113 ) を抽出するための改善幅と設定した.
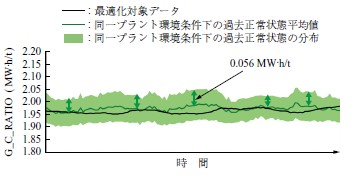
4.5 運転効率向上に向けた動的単位空間の生成
第7図に抽出された熱効率が良いデータ群の分布を,第8図に運転制御値の修正量を示す.第7図において,縦軸はG_C_RATIO,横軸は時間を表している.黒い線は検証データの値,緑色部分は運転効率指標 ( G_C_RATIO ) の抽出範囲を示している.
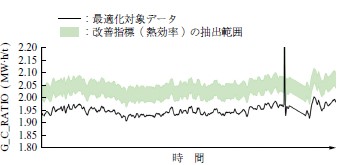
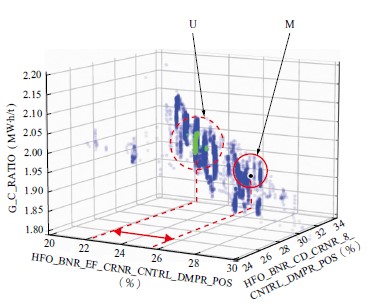
第8図では,第3図と同様に,G_C_RATIO以外に各運転操作値も含めて三次元で表示しており,時系列データではなく,ある一時点を取り出した図となる.このように,検証データを表す黒丸の計測点Mと,緑色部分で表される動的単位空間UとのMD値が高く,貢献度が高い(第8図ではMD値を構成する次元のうち,乖離が大きい赤い矢印方向を意味する)運転操作項目を改善対象としてその修正値を求める.
今回の事例では,貢献度が最も高いHFO_BNR_EF_CRNR_5_CNTRL_DMPR_POS(制御ダンパーの位置)が修正対象となった.第8図での可視化は一時点での瞬間値であるが,改善対象とした連続区間の動的単位空間Uの平均値と計測点Mの差について平均値を求めた結果,該当する制御ダンパーの位置を−2.4%変更することでG_C_RATIOを改善可能と推定した.
なお,当然ながら複数の運転操作項目に対して修正した方が良い場合もあるが,MT法の貢献度を利用することで,このような場合でも適切な複数の運転操作項目を抽出することが可能であると考える.
4.6 運転効率向上の期待値の算出
ここで,学習用のデータセットから改めて類似した動作環境,かつHFO_BNR_EF_CRNR_5_CNTRL_DMPR_POSが−2.4%になっていたデータを抽出し,G_C_RATIOがどのように変化するか比較した.第9図に修正量適用後の熱効率改善幅を示す.第9図 - ( a ) において,縦軸はG_C_RATIOの値,横軸は運転時間である.黒い線は検証データの時系列値であり,緑色部分は学習データから抽出されたデータの値の分布 ( ± 1σ ) を時系列で表したものである.第9図 - ( b ) は縦軸がG_C_RATIOの値,横軸がHFO_BNR_EF_CRNR_5_CNTRL_DMPR_POSの値であり,第8図と同様にある一時刻の散布図を表している.
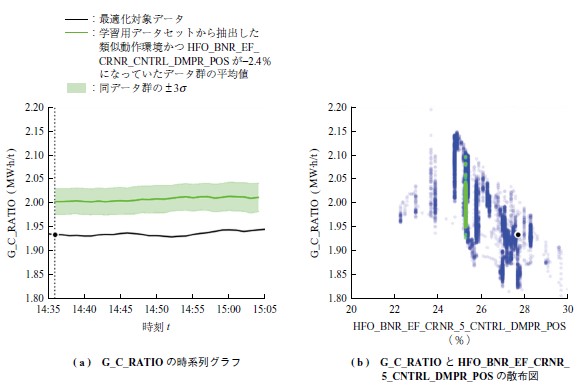
時系列情報のため,常に一定のG_C_RATIOの改善につながるものではないが,おおむね平均1.93 MW·h/tから平均2.01 MW·h/tに向上することが見込まれた.これは,改善率でいえば3.7%の効率改善に相当する.本データセットでは,学習用データ群と検証用データ群の間でボイラの動作環境,内部状態に大きな差異は見られなかったため,この改善策は実現可能なものと考えられる.
5. 結言
5.1 ま と め
プラントの稼働データに動的MT法を適用することによって,動作環境によって変化する複雑な内部状態を持つプラントに対して,運転効率の向上が期待できる運転区間や改善すべき運転操作項目とその修正量を,(修正)判断に対して説明性を持った形で明らかにする手法を提案した.本提案手法を模擬データに適用しデータ分析を行った結果,約3.7%の熱効率改善効果が見込めるなど,本提案手法が有効であることが分かった.
5.2 課 題
本提案手法では,単位空間を構成する診断項目に運転操作項目を設定しているため,同一の動作環境下でも異なる運転操作を行っているようなプラントでは,抽出された動的単位空間が幾つかのクラスタを構成することも考えられる.このような場合でも正しく改善が期待できる運転区間を抽出できるようにすることが課題である.また,過去の運転操作履歴が内部状態の変化に与える影響が大きいプラントに対して,定常状態だけでなく内部状態の変化が大きい過度状態への対応が課題である.さらに,本提案手法では,運転操作量の変更と熱効率向上との因果関係までは明らかにしていないため,因果関係まで説明できるようにすることが課題である.
5.3 今後の展開
現在,本提案手法の実プラントへの適用を進めており,実運用において,本手法が熱効率の向上に有効であることを実証していく.また,本稿ではプラントの熱効率を扱ったが,本手法は二酸化炭素の排出削減率,消費電力の削減率,製品の歩留率など,他の運転効率指標の向上にも適用が可能である.今後もさまざまな分野のIHI製品の運転効率向上に向けて本技術を展開し,ライフサイクル全体でお客さま価値の向上を実現していく.
参考文献
(1) 田口玄一著,矢野 宏編:田口玄一論説集第4巻,一般財団法人日本規格協会,2012 年2 月
(2) 袖子田志保,木村麻衣,鈴木由宇,近藤智佳子:データ分析による予防保全技術の開発,IHI技報,Vol. 54,No. 2,2014 年6 月,p. 26-31
(3) 茂木悠佑,袖子田志保,河野幸弘:単位空間の最適化によるプラント異常診断の精度向上,第48回信頼性・保全性シンポジウム,2018 年
(4) 茂木悠佑:単位空間を動的に生成することによる,機械設備・プラント異常診断の精度向上,第27回品質工学研究発表大会,2019年
(5) 長島 瞳,長谷川雄大,茂木悠佑,河野幸弘:機械学習の活用による異常診断技術の応用,IHI技報,Vol. 60,No. 1,2020 年3 月,p. 29-33
(6) 茂木悠佑:動的単位空間を適用したMT法による,産業設備の異常診断,第29回品質工学研究発表大会,2021 年
(7) kaggle:Power Plant Optimization Problemデータセット,https://www.kaggle.com/datasets/deepakburi062/power-plant-optimization-problem,(参照2024. 11. 1)